Manufacture of Sulfuric Acid: Insights and Trends
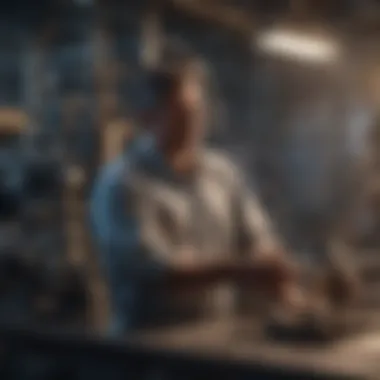

Intro
The manufacture of sulfuric acid holds a pivotal place in numerous industrial processes, making it one of the most vital chemical commodities worldwide. Its significance stems from its versatile applications across various sectors, including fertilizer production, petroleum refining, and metal processing. Understanding the complexities involved in its production sheds light on both the challenges encountered and the innovations being pursued.
Background and Context
Overview of the Research Topic
Sulfuric acid, known chemically as SO4, is produced through two primary processes: the Contact Process and the Lead Chamber Process. Each method has its own set of reactions and operational guidelines. The transformation of sulfur into sulfuric acid involves several steps, showcasing the importance of temperature and pressure control.
Historical Significance
Historically, sulfuric acid has played a critical role in chemical manufacturing. The Lead Chamber Process, developed in the 19th century, revolutionized production methods before the introduction of the more efficient Contact Process. As industries have evolved, the methodologies of sulfuric acid production have consistently advanced.
Key Findings and Discussion
Major Results of the Study
The analysis indicates that the Contact Process is predominantly used today due to its efficiency and lower environmental impact. Studies show that with advancements in technology, the yield and purity of the acid produced have significantly improved.
Detailed Analysis of Findings
Operational parameters such as catalysts, temperature, and pressure are crucial in the Contact Process. Vanadium pentoxide acts as a catalyst, enhancing the conversion of sulfur dioxide to sulfur trioxide. Environmental concerns also arise, particularly regarding emissions of sulfur oxides and their contribution to acid rain. Strategies for mitigating these effects are essential for sustainable production.
"The transition to greener methodologies in sulfuric acid production not only addresses environmental concerns but also enhances economic viability."
Efforts to minimize the carbon footprint of sulfuric acid manufacturing are gaining traction. Capturing and reusing emissions in the production cycle is one proposed solution.
Applications Across Industries
The applications of sulfuric acid extend beyond production; it is a key reagent in numerous chemical reactions. In agriculture, it is primarily used to manufacture fertilizers. In metallurgy, sulfuric acid facilitates the extraction of metals such as copper and nickel from their ores. The versatility of sulfuric acid renders it indispensable in modern industry.
Future Trends
Looking forward, research and innovation will guide the development of more sustainable production techniques. Enhanced monitoring and automated processes promise greater efficiency and reduced waste in sulfuric acid production.
Prologue to Sulfuric Acid
Sulfuric acid is an essential industrial chemical that serves a multitude of purposes in various sectors. Understanding its significance and production processes is crucial for both scholars and professionals. By examining sulfuric acid's definition, historical context, and diverse applications, readers gain insight into its pivotal role in modern industry.
Definition and Importance
Sulfuric acid, with the chemical formula H₂SO₄, is a dense, colorless liquid known for its strong acidic properties. It is hygroscopic and highly reactive, making it vital in chemical manufacturing, mining, and many other industries. Its versatility offers numerous benefits, such as:
- Chemical Manufacture: Sulfuric acid acts as a key ingredient in the production of fertilizers, explosives, and petrochemicals.
- Resource Extraction: It is used in processes like metal refining and mineral processing.
- Industrial Applications: Sulfuric acid finds use in batteries, waste treatment, and pulp manufacturing.
The relevance of sulfuric acid in industrial settings cannot be understated, given that it supports infrastructure and agriculture crucial to economic development.
Historical Context
The journey of sulfuric acid dates back to ancient times. Initially, it was produced by alchemists in the Middle Ages who inadvertently created it through the distillation of sulfate-containing minerals. The recognized process for synthesizing sulfuric acid emerged in the 18th century, leading to the formalization of its production techniques.
By the 19th century, with the advent of the Industrial Revolution, sulfuric acid gained prominence in heavy industries. The Lead Chamber Process was one of the first techniques employed for large-scale production. Later, the more advanced Contact Process provided a significant enhancement in efficiency and yield.
Today, sulfuric acid is recognized as a cornerstone of chemical industrialization, underscoring its importance not merely as a chemical but as a catalyst for technological advancement and sustainability in manufacturing. As society progresses, the challenge remains to produce it more efficiently while minimizing environmental impacts.
Chemical Properties of Sulfuric Acid
Understanding the chemical properties of sulfuric acid is fundamental for various applications and production methods. This section will delve into its chemical composition and physical properties, both of which are crucial for professionals in the chemical industry, researchers, and students. Recognizing these properties allows for the optimization of production processes, safety in handling, and effective usage in practical applications.
Chemical Composition
Sulfuric acid is a strong mineral acid with the chemical formula H₂SO₄. It is composed of two hydrogen atoms, one sulfur atom, and four oxygen atoms. The molecular structure features the sulfur atom at the center, bonded to two hydroxyl (–OH) groups and double bonded to two oxygen atoms. This configuration contributes to its highly reactive nature. The acid is typically produced from sulfur dioxide, which is oxidized to form sulfur trioxide, followed by the reaction of sulfur trioxide with water.
- Molecular Weight: The molecular weight of sulfuric acid is approximately 98.08 g/mol.
- Acidity: It is categorized as a diprotic acid, meaning it can donate two protons per molecule. This behavior is key in various chemical reactions, especially in neutralization processes.
The chemical stability of sulfuric acid at ambient conditions makes it widely used in laboratories and industrial settings. However, its corrosive nature poses risks, demanding careful handling and safety measures during production and use.
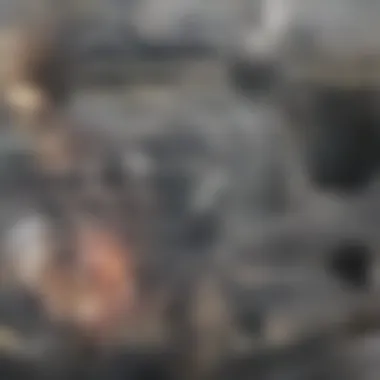

Physical Properties
Sulfuric acid is a dense, oily liquid at room temperature, often appearing colorless to slightly yellow in pure form. Some important physical properties include:
- Density: It has a high density of about 1.84 g/cm³, which is significantly greater than water. This property is essential for calculating concentrations in solutions.
- Boiling Point: The boiling point of sulfuric acid is around 337 °C (639 °F), indicating that it can remain in liquid form under various processing conditions.
- Solubility: Sulfuric acid is highly soluble in water but releases a significant amount of heat during dilution. This exothermic reaction necessitates caution during mixing with water.
- Viscosity: It has a high viscosity, which can affect the flow in industrial processes.
"The versatility of sulfuric acid in chemical reactions stems from its ability to act as both an acid and an oxidizing agent."
In various applications, such as fertilizer production, resource extraction, and chemical manufacturing, understanding these properties is essential for effective utilization and safe handling. The combination of sulfuric acid's chemical composition and physical properties underlines its relevance across multiple industries. By mastering these fundamentals, industry experts can enhance productivity while ensuring adherence to safety protocols.
Production Methods
The production methods of sulfuric acid are crucial to understanding its large-scale manufacture. These methods determine not only the efficiency of acid production but also impact the overall cost and environmental footprint. In this section, we will examine two prominent méthodes: the Contact Process and the Lead Chamber Process. Each method serves specific industrial needs and has unique advantages and disadvantages that are essential for professionals to consider in the field of sulfuric acid production.
The Contact Process
Overview of the Process
The Contact Process is the dominant method for producing sulfuric acid. It involves the catalytic oxidation of sulfur dioxide (SO2) to sulfur trioxide (SO3), followed by the absorption of SO3 in water. The key characteristic of this process is its use of vanadium(V) oxide as a catalyst, which makes it highly efficient.
This process is beneficial due to its relatively high yield and lower energy requirements compared to older methods. A unique feature of the Contact Process is the ability to control the operating conditions, enhancing the overall production rate. Its advantages include better economic viability for large scale operations, while the disadvantage could be the initial setup cost, which may be higher than some alternative methods.
Chemical Reactions
The major chemical reactions involved in the Contact Process are:
- 2 SO2 + O2 ⇌ 2 SO3
- SO3 + O → SO4
These reactions are important as they are not only fundamental to the production of sulfuric acid, but they also highlight the significance of catalyst and temperature control. The high conversion rate of sulfur dioxide to sulfur trioxide is a key characteristic of the process that enhances its popularity. However, the reactions must be managed carefully to avoid the formation of unwanted by-products, which can complicate the process.
Operational Parameters
The operational parameters of the Contact Process, including temperature and pressure, play significant roles in the efficiency of acid production. Typically, the process operates at temperatures between 400 °C and 600 °C and pressures of 1 to 2 bars. A notable characteristic of these parameters is that optimizing them can lead to increased conversion rates and improved yields. The ability to adjust these conditions is a major advantage, but it also requires sophisticated equipment and constant monitoring, which adds to operational complexity.
The Lead Chamber Process
Overview of the Process
The Lead Chamber Process is one of the oldest methods for producing sulfuric acid on an industrial scale. It relies on the reaction of sulfur dioxide with nitric acid in the presence of water. An important characteristic of this method is its reliance on large chambers made of lead, which are used to contain the chemical reactions. This process was widely used until the advent of the Contact Process.
Despite its historical significance, many modern plants have moved away from this method due to its lower efficiency. The unique feature of the Lead Chamber Process is its relatively simple setup compared to the Contact Process, making it easier to operate at a small scale. However, the disadvantages include much lower acid concentration and output, limiting its competitiveness today.
Chemical Reactions
The chemical reactions in the Lead Chamber Process primarily involve:
- 3 SO2 + 2 O + 4 NO → 2 SO4 + 4 NO2
This reaction showcases the method's reliance on the interplay of nitric oxide and sulfur dioxide to produce sulfuric acid. The chemical reactions are less efficient compared to the Contact Process. It may not yield as much sulfuric acid in a shorter time frame, which is a significant drawback in contemporary production contexts.
Operational Parameters
In the Lead Chamber Process, the operational parameters include temperature, pressure, and the concentration of reactants. This process generally occurs at lower temperatures and pressures than the Contact Process. An essential characteristic is that this lower range requires more extended reaction times to achieve satisfactory yields. While the method’s simplicity might seem advantageous for some small-scale operations, the protracted duration of production results in time and cost inefficiencies.
Comparison of Methods
Efficiency
When considering efficiency, the Contact Process is remarkably superior. It achieves higher concentrations of sulfuric acid in a shorter time frame with better yield rates. The Lead Chamber Process, although historically significant, often struggles to meet modern production demands due to its lower efficiency. However, it can be beneficial in specific contexts where infrastructure is limited or initial costs must be minimized.
Scale of Production
The scale of production is a determining factor when choosing between processes. The Contact Process is well-suited for large-scale operations, providing economies of scale that are essential for meeting industrial demands. Conversely, the Lead Chamber Process may be more appropriate for limited production needs where high-level investment in technology is not feasible.
Environmental Impact
The environmental impact of each method is another important consideration. The Contact Process has evolved to adopt more environmentally friendly practices, significantly reducing emissions. On the other hand, the Lead Chamber Process often produces higher emissions and is less compliant with modern environmental regulations. Thus, while the historical context of the Lead Chamber Process is significant, its environmental considerations are increasingly problematic in today’s context.
"Understanding these production methods highlights the critical considerations in the manufacture of sulfuric acid, driving both efficiency and environmental responsibility in the chemical industry."
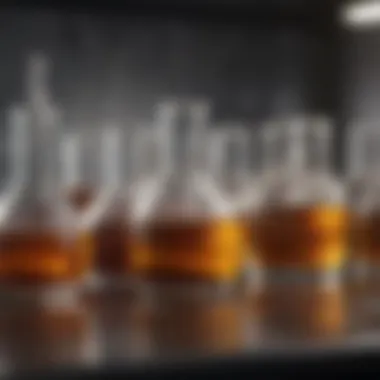

Given the distinct characteristics and environmental implications of both production methods, professionals must carefully evaluate their choices based on operational context and desired outcomes.
Raw Materials in Sulfuric Acid Manufacture
The selection and management of raw materials play a crucial role in the manufacture of sulfuric acid. This section outlines the significance of sourcing appropriate materials, emphasizing the benefits and considerations through three main components: sulfur, oxygen, and water. These elements form the backbone of the production process, impacting both the efficiency and quality of the final product.
Sulfur Sources
Sulfur is the primary raw material in the production of sulfuric acid. It can be sourced from various natural and industrial processes, influencing not only the production flow but also environmental compliance. The most common sources include:
- Elemental Sulfur: Extracted from sulfur mines and often found near volcanic regions.
- Sulfur Containing Fossil Fuels: Oils and natural gas contain sulfur which can be recovered during refining processes.
- Byproducts from Industrial Processes: In many chemical manufacturing sectors, sulfuric acid is produced as a byproduct, notably in the smelting of metal ores. For instance, copper production generates sulfur dioxide, which can be transformed into sulfuric acid.
By leveraging these sulfur sources, manufacturers can ensure a steady supply for large-scale production while considering potential fluctuations in market availability.
Oxygen Sources
Oxygen is another essential raw material used mainly in the conversion of sulfur dioxide into sulfur trioxide, a key step in producing sulfuric acid. The sources of oxygen vary, with the two primary methods being:
- Air: This is the most common source. Ambient air undergoes processing in an oxidation step to provide the necessary oxygen.
- Pure Oxygen Enrichment: In some advanced production facilities, pure oxygen is extracted for use. This method increases the reaction efficiency but requires more elaborate systems for oxygen supply.
Understanding the impact of these oxygen sources is important. High purity oxygen typically results in a more efficient production cycle, allowing for better yields of sulfuric acid. However, it also raises concerns about cost and supply logistics.
Water Usage
Water is fundamental in the sulfuric acid manufacturing process. It is utilized for various purposes including:
- Cooling Systems: Large quantities of water are required to manage heat during the production process, ensuring that equipment operates within safe temperature limits.
- Dilution: Sulfuric acid is extremely concentrated and must be diluted for safe handling and application. Water must be added carefully to avoid exothermic reactions.
- Cleaning Processes: Maintaining equipment is vital for efficiency, and water serves as a primary cleaning medium for reactors and other tools used in production.
Excessive water usage can raise operational costs and pose environmental concerns. Manufacturers need to monitor water consumption and recycling methods carefully. This not only helps in minimizing waste but also aligns with sustainability practices that improve operational efficiency.
Managing the raw materials effectively contributes to both economic benefits and environmental sustainability in sulfuric acid production.
Environmental Considerations
The manufacture of sulfuric acid is not only a significant industrial process but also one that presents various environmental challenges. This section examines the critical considerations related to the environmental impact of sulfuric acid production. Efforts to control pollution and implement sustainability practices are essential in mitigating the adverse effects on ecosystems and public health. Understanding these aspects is crucial, especially as the global demand for sulfuric acid continues to rise across diverse applications.
Pollution Control Measures
Pollution control measures are essential in the sulfuric acid manufacturing process. The emissions from production facilities can pose severe risks to air and water quality. Key strategies to manage these emissions include:
- Scrubber Systems: These systems are used to remove harmful gases like sulfur dioxide before they are released into the atmosphere. They work by passing exhaust gases through a liquid that absorbs the pollutants.
- Emission Limits: Regulatory bodies set strict emission limits. Compliance with these regulations is critical. Facilities often monitor their emissions to ensure they remain within permissible limits.
- Waste Management: By recycling wastewater and minimizing waste generation, producers reduce the risk of contamination to surrounding environments. This can involve treating and reusing process water.
These measures not only protect the environment but also enhance the sustainability of sulfuric acid production. Companies that prioritize pollution control can benefit from compliance credits and positive public perception.
Sustainability Practices
Integrating sustainability practices into sulfuric acid production has become more important as industries seek to minimize their ecological footprint. Some notable practices include:
- Energy Efficiency: Optimizing energy use in the production processes can significantly reduce both operational costs and greenhouse gas emissions. Implementing advanced technologies that require less energy contributes to a more sustainable operation.
- Renewable Resources: Investment in renewable energy sources, such as solar or wind, can provide cleaner energy for production processes. This shift not only reduces reliance on fossil fuels but also minimizes overall carbon emissions.
- Green Chemistry: Applying green chemistry principles in the production of sulfuric acid results in less hazardous substances being used. This approach promotes safer alternatives throughout the chemical manufacturing process.
"Incorporating sustainability practices is not just beneficial for the environment; it also paves the way for long-term economic viability."
By focusing on these sustainability efforts, manufacturers of sulfuric acid can better align their operations with global environmental goals, enhancing their standing in an increasingly eco-conscious market.
Challenges in Sulfuric Acid Production
The manufacture of sulfuric acid is a critical component of various industries, but it is not without its challenges. Understanding these challenges is pivotal for improving production methods while maintaining environmental and financial sustainability. In this section, we focus on three crucial elements: process efficiency, cost management, and regulatory compliance.
Process Efficiency
Efficiency in the production of sulfuric acid directly impacts operational costs and environmental footprint. The processes used in manufacturing must maximize output while minimizing energy usage and waste. One of the key aspects of improving efficiency is optimizing the operational parameters of the production methods. These include temperature, pressure, and the concentration of reactants. By ensuring that these factors are finely tuned, manufacturers can enhance yield and reduce the resources required.
Moreover, the implementation of technology, such as advanced sensors and real-time monitoring systems, can lead to better efficiency. These technologies enable proactive adjustments during production, thus avoiding downtime.
Cost Management
Cost management presents a complex challenge given the volatile nature of raw material prices and operational expenses. The primary materials used, such as sulfur and oxygen, can fluctuate in cost due to market demand and geopolitical factors. Therefore, it is essential for producers to develop strategies for procurement that mitigate risk.
Furthermore, energy efficiency is also a critical component of managing costs. Higher energy efficiency lowers electricity demands and reduces overall operational costs. This can be achieved through improved process technology and heat recovery systems. Manufacturers must regularly assess their energy usage and identify areas for potential savings.
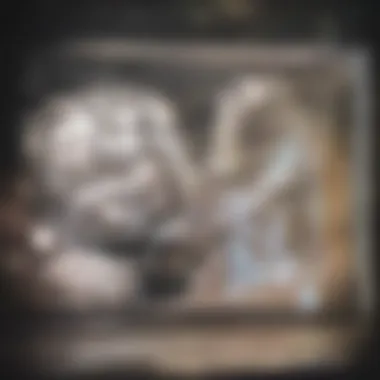

Regulatory Compliance
Regulatory compliance refers to the adherence to laws and guidelines governing sulfuric acid production and its environmental impact. The production of this acid often involves hazardous materials, which necessitate strict regulations to protect workers and the environment. Failure to comply can result in fines, legal issues, and damage to a company's reputation.
To ensure compliance, manufacturers must stay abreast of changing regulations and invest in necessary technologies and training for their employees. This can include pollution control technologies that limit emissions and waste. Additionally, proper documentation and reporting processes are essential, as they provide transparency and accountability.
"Effective management of production challenges in sulfuric acid manufacture is vital not just for profitability, but also for sustainable operations that align with environmental standards."
In summary, the challenges in sulfuric acid production are multi-faceted, involving a keen focus on process efficiency, cost management, and regulatory compliance. Addressing these issues head-on is essential for manufacturers aiming to thrive in an ever-changing industrial landscape. By investing in modern technologies and best practices, they can better navigate these challenges and position themselves for success.
Applications of Sulfuric Acid
Sulfuric acid plays a crucial role in various industries, showcasing its versatility and significance. It is not merely a widely used industrial chemical, but it also serves as a cornerstone for many chemical processes. The wide range of applications is due to its unique properties, ability to react with a multitude of substances, and its role in the synthesis of various compounds. As industries evolve, the applications of sulfuric acid continue to expand, making it an ever-relevant topic to study and understand.
In the Chemical Industry
Sulfuric acid is one of the most important substances in the chemical industry. It is primarily used as a reactant in various chemical reactions. It functions as a dehydrating agent, catalyst, and acid in many synthesis processes. Some of the crucial applications in this sector include:
- Production of Other Chemicals: Sulfuric acid is essential in producing phosphoric acid, hydrochloric acid, and nitric acid, among others. These acids are vital for fertilizers, explosives, and other important chemicals.
- Water Treatment: It is utilized in the pH adjustment of wastewater, neutralizing alkaline substances. Its effectiveness in this process helps improve the quality of water discharged into the environment.
- Battery Manufacturing: In lead-acid batteries, sulfuric acid acts as the electrolyte. This application is significant in the production of batteries used in vehicles and for energy storage.
Sulfuric acid stands as an essential reagent and catalyst, powering the chemical reactions that drive much of modern industry.
In Fertilizer Production
The agricultural sector heavily relies on sulfuric acid for fertilizer production. Specifically, it is a key component in producing phosphate fertilizers.
- Phosphate Fertilizers: The process of creating superphosphate involves reacting sulfuric acid with phosphate rock. The resulting products provide essential nutrients to various crops, enhancing yield and fostering agricultural growth.
- Sulfur Coated Urea: This fertilizer combines sulfur and nitrogen, where sulfuric acid assists in the coating process. It ensures a slow release of nitrogen, benefiting crop development over time.
The ability of sulfuric acid to convert raw materials into fertile products underscores its importance in ensuring food security globally.
In Resource Extraction
Sulfuric acid is integral to resource extraction industries, particularly in mining operations. Its applications include:
- Metallurgy: In the extraction of metals such as copper and zinc, sulfuric acid is employed to leach the metals from their ores. This process increases efficiency and yield during metal recovery.
- Mineral Processing: It is used in the processing of various minerals where chemical reactions with acids facilitate the separation of valuable resources from waste materials.
As global demand for metals and minerals continues to rise, sulfuric acid's role in resource extraction becomes even more vital.
In summary, the applications of sulfuric acid are extensive and impact several key industries. Its role in chemical productions, fertilizer manufacturing, and resource extraction highlights its versatility and necessity in modern society.
Future Trends in Sulfuric Acid Manufacturing
The future of sulfuric acid manufacturing presents various new opportunities and challenges. This section highlights significant advancements and shifts in this field. Staying abreast of these trends is crucial for industry stakeholders, including manufacturers, researchers, and environmentalists. Innovations foster efficiency, sustainability, and economic viability.
Technological Innovations
Advancements in technology are reshaping how sulfuric acid is produced. Here are notable innovations:
- Automation and AI: The integration of automated systems enhances production efficiency. AI can analyze operational data to optimize processes in real-time. This reduces material waste and energy consumption.
- Process Intensification: This concept involves the redesign of conventional processes to make them more efficient. Using compact equipment can lead to lower energy input and higher output. This results in significant cost savings.
- Enhanced Catalyst Development: New catalysts improve reaction rates, lowering temperatures and pressures needed for production. For example, recent research has resulted in more effective vanadium-based catalysts. These innovations contribute to improved sustainability and reduced emissions.
"Technological innovations in sulfuric acid production can lead to reduced operational costs and lower environmental impact."
Each of these innovations underscores a trend toward making sulfuric acid manufacturing not just more efficient, but also more eco-friendly. It allows industries to meet stricter environmental regulations.
Alternative Production Methods
Alternative methods of producing sulfuric acid are gaining research interest. These methods aim to reduce dependence on traditional processes and lessen environmental impacts. Such methods include:
- Hydrometallurgical Processes: These techniques utilize aqueous solutions to extract metals and produce sulfuric acid as a byproduct. It's a more sustainable approach, especially in resource recovery from mining waste.
- Biotechnological Approaches: Utilizing microorganisms in acid production is an emerging field. These bioprocesses may offer lower energy requirements compared to traditional methods.
- Electrochemical Methods: Electrolytic processes can produce sulfuric acid while minimizing carbon emissions. This technique focuses on direct sulfur oxidation, which can lead to improved energy efficiency.
Exploring these alternative production methods can lead to a more resilient and adaptable sulfuric acid industry. Adapting to these new approaches is vital in aligning with global shifts toward sustainability.
Epilogue
In the realm of industrial chemistry, the manufacture of sulfuric acid stands as a cornerstone of various chemical processes and applications. This article elucidated the intricate methods and challenges associated with sulfuric acid production, as well as its extensive uses across multiple industries. Understanding the manufacturing processes and their implications fosters a deeper appreciation for sulfuric acid's role in modern society.
Summary of Key Points
The key insights presented in this article include the following:
- Production Methods: Two main production methods have been examined—the Contact Process and the Lead Chamber Process. Each method has unique operational parameters and chemical reactions that determine their efficiency and environmental impact.
- Environmental Considerations: Pollution control measures and sustainability practices are paramount in minimizing the environmental footprint of sulfuric acid manufacturing. Regulatory compliance ensures that production aligns with safety and ecological standards.
- Challenges in Production: The challenges faced in sulfuric acid production include process efficiency, cost management, and navigating complex regulations.
- Applications: Sulfuric acid is indispensable in the chemical industry, fertilizer production, and resource extraction, showcasing its versatility and importance.
Implications for the Future
The future of sulfuric acid manufacturing is likely to be shaped by several trends and innovations. Technological advancements may lead to enhanced production efficiency and reduced emissions. Companies might adopt alternative production methods that utilize renewable resources or minimize waste. Additionally, a growing awareness of environmental sustainability drives the need for cleaner production practices.