Exploring Additive Layer Manufacturing Innovations

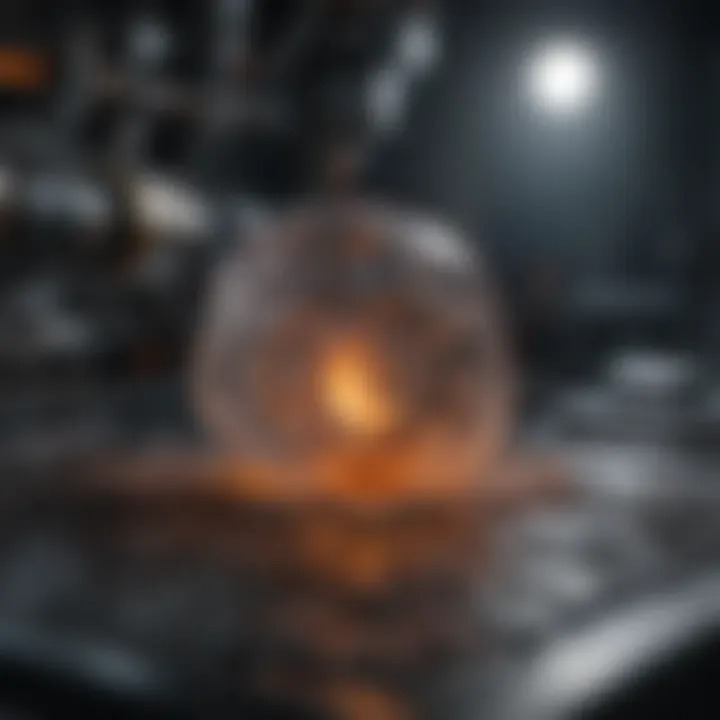
Background and Context
Additive layer manufacturing (ALM) represents a monumental shift in the manufacturing landscape. Unlike traditional subtractive manufacturing methods, which often involve cutting away material, ALM builds objects layer by layer. This fundamental difference opens up a plethora of possibilities, forging new pathways for innovation across various sectors.
Historically, ALM traces its roots back to the 1980s with the advent of 3D printing technologies. Initially confined to prototyping, it has matured into a core manufacturing process across industries. The transition from rapid prototyping to full-scale production reflects an accelerating transformation in how products are conceived, designed, and fabricated.
Key Findings and Discussion
In our exploration of additive layer manufacturing, several key findings emerge that exemplify its significance in contemporary manufacturing contexts.
Major Results of the Study
The study outlines three primary areas where ALM has made substantial headway:
- Customization: ALM enables unprecedented levels of customization, allowing businesses to tailor products to specific needs without altering the entire manufacturing process. For example, in healthcare, patient-specific implants are designed and manufactured to perfectly fit individual anatomies.
- Efficiency: With the ability to produce complex geometries and reduce material waste, ALM streamlines production. Industries such as aerospace benefit from lighter components that do not compromise strength, enhancing fuel efficiency and reducing costs in the long run.
- Sustainability: One of the striking advantages of ALM is its potential to improve sustainability within manufacturing. Traditional methods often lead to significant material waste, while ALM employs only the materials necessary for construction. The opportunity to use biodegradable or recycled materials further advances eco-friendly practices.
Detailed Analysis of Findings
As we delve deeper into the implications of these findings, it's clear that the transformative potential of ALM cannot be overstated.
"The capacity for high design freedom and the reduction of supply chain complexities is a game-changer."
The aerospace sector showcases a remarkable application of ALM. Boeing, for instance, is exploring the production of lightweight components that contribute to both performance and fuel savings. Moreover, in the automotive industry, companies like Audi are utilizing ALM to create intricate parts that would be challenging or impossible with traditional methods.
With the rise of ALM, challenges do persist. Issues around quality control, material properties, and certification pose significant hurdles that must be overcome as this technology continues to evolve.
Prelude to Additive Layer Manufacturing
In the realm of modern manufacturing, exploring additive layer manufacturing (ALM) is akin to stepping into an open door that leads to a new age of production possibilities. ALM presents a fundamentally different approach compared to traditional subtractive methods, which often involve cutting away materials to create a final product. This shift is not merely a technical adjustment but a re-imagining of how we conceive the design and fabrication of objects.
The significance of ALM lies in its ability to enable more complex geometries and intricate designs that were previously unimaginable. For instance, consider a turbine blade; with traditional methods, such a design might require extensive assembly or be limited by machining processes. But using ALM, we can fabricate intricate cooling channels directly into the blade, optimizing its performance while saving weight and materials.
This technique is particularly beneficial across various industries including aerospace, healthcare, and consumer goods, leading to enhanced customization and efficiency. As we delve deeper into ALM, we'll uncover its numerous advantages, such as reduced waste and faster production times, alongside considerations around materials and technology integration. By understanding the foundations of this innovative manufacturing process, professionals and students alike can appreciate its impact and potential.
Definition and Overview
Additive layer manufacturing, often known by its more common term 3D printing, is a process where material is added layer by layer to create a three-dimensional object based on digital models. This technique can employ a variety of materials such as plastics, metals, and even biological materials, making it incredibly versatile for different applications.
In contrast to conventional manufacturing, which typically requires the removal of material to shape an object, ALM builds items from the ground up. It allows for a high degree of control over the material distribution, resulting in optimal strength, durability, and efficiency. This process starts with a computer-aided design (CAD) model, which gets sliced into thin horizontal layers for the printing process, subsequently allowing for the seamless construction of complex shapes.
The technology behind ALM has evolved rapidly, facilitating advancements in both the types of available materials and the methods of execution. Companies and researchers are constantly exploring new avenues to enhance ALM processes, enabling shorter production cycles and broader application scopes.
Historical Development
To appreciate the importance of additive layer manufacturing today, it's essential to look back at its origins. The concept of additive manufacturing surfaced in the 1980s, with the introduction of stereolithography, a process that used ultraviolet light to cure layers of resin.
As the years progressed, numerous methodologies began to emerge, establishing footholds in various industrial sectors. In the mid-1990s, the introduction of Selective Laser Sintering (SLS) allowed for the use of powdered materials, further diversifying the types of products that could be created.
By the early 2000s, costs associated with 3D printers began to decline, making the technology more accessible for small businesses and individuals. This democratization of ALM technology spurred a wave of innovation and experimentation, allowing startups to flourish in the field of customized products and rapid prototyping.
"The future of manufacturing is not just about efficiency, it's about redefining what we can create."
Looking ahead, it is evident that additive manufacturing is not static; it is a dynamic and evolving field that is poised to redefine how industries approach design and production. The historical journey of ALM emphasizes its transformative potential and sets the stage for examining its principles, methods, and applications in greater depth.
Key Principles of Additive Layer Manufacturing
Understanding the key principles of Additive Layer Manufacturing (ALM) is crucial for comprehending how this technology works and its potential applications. This section discusses three fundamental aspects: layer-by-layer construction, material utilization, and digital modeling techniques. Each of these principles serves not only as a foundational pillar for ALM but also drives its advancements and implementations across various industries.
Layer-by-Layer Construction
The concept of layer-by-layer construction is at the heart of additive layer manufacturing. This process involves adding material in thin layers, one on top of the other, to create a 3D object. As straightforward as it sounds, the implications of this approach are profound. By allowing for intricate geometries and complex designs that would be nearly impossible with traditional subtractive methods, manufacturers can push the envelope of design creativity.
From the single-layer concept, products can be customized to specific needs. This kind of freedom is like having a blank canvas. For instance, engineers can design lightweight components for the aerospace industry, reducing fuel consumption and increasing efficiency. An aircraft part that has been optimized through layer-by-layer construction can enhance performance significantly.
Benefits of layer-by-layer construction include:
- Customization: Each iteration can be tweaked to suit particular requirements without the need for extensive retooling.
- Reduced Waste: As material is only used where needed, there is less scrap compared to traditional manufacturing methods.
- Speed: Rapid prototyping is achieved as layers can be printed quickly, allowing for faster feedback loops in product development.
Material Utilization
Material utilization in ALM involves the strategic selection and application of various materials, determined by the specific functional and structural needs of the final product. One striking feature of ALM is its capacity to use diverse materials such as polymers, metals, and ceramics.
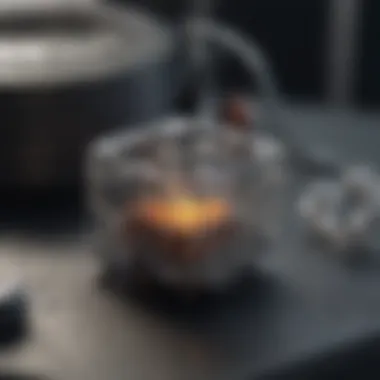
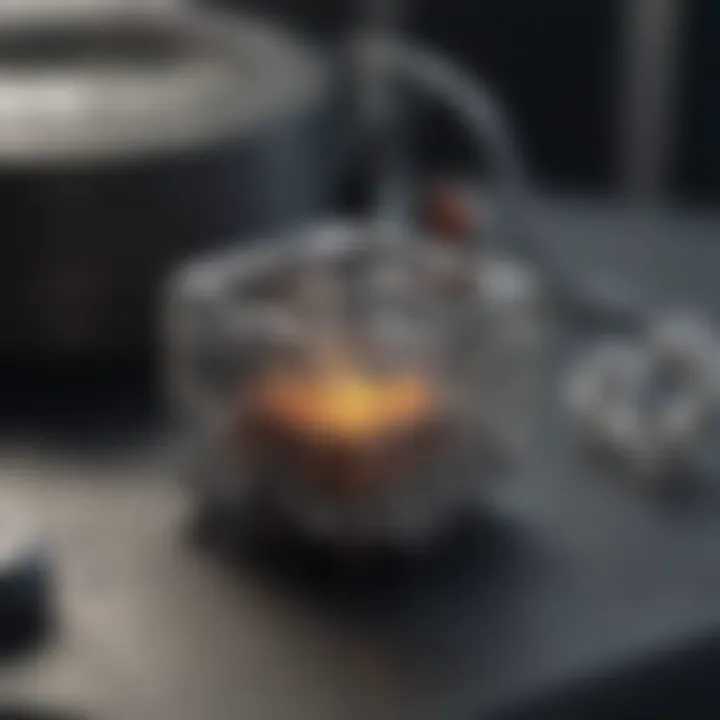
The efficiency of material usage is noteworthy. Instead of a lengthy milling process that cuts away what is not needed, ALM allows additive processes to grow parts directly from digital models, drastically reducing excess material. An example can be found in the medical field where custom implants can be produced from titanium powder, providing not only strength but also biocompatibility, ensuring a better integration with the human body.
Advantages of effective material utilization include:
- Eco-Friendly Production: Lesser waste translates to more sustainable manufacturing practices.
- Enhanced Performance: Tailored material properties can lead to improved end-product characteristics.
- Cost Reduction: By minimizing scrap, companies can significantly lower material costs, which is significant in industries with high material expenses.
Digital Modeling Techniques
Digital modeling techniques are the backbone of ALM, facilitating the transition from virtual designs to tangible products. The advent of advanced software has enabled designers to create complex models that can be directly fed into 3D printers. The precision in these models ensures that every detail anticipated in the design process is accurately represented in the final product.
Moreover, techniques such as CAD (Computer-Aided Design) and CAM (Computer-Aided Manufacturing) have evolved to enable simulations of how a product will behave under various conditions. This means that potential issues can be identified early, and adjustments can be made to avoid costly mistakes during print runs.
A compelling feature of digital modeling techniques is the ability for iterations. Unlike traditional methods that might require a substantial investment in time and resources for each revised model, digital technology allows for quick and easy revisions.
"Digital modeling techniques provide a bridge between imagination and reality, turning concepts into real-world solutions."
Benefits of digital modeling techniques include:
- Efficiency: Rapid adjustments can be made without extensive delays.
- Accuracy: Reduces errors, ensuring the product meets its intended specifications.
- Collaboration: Designers, engineers, and stakeholders can work on the same model, enhancing communication and reducing discrepancies.
By grasping these principles, industry professionals can harness the full potential of additive layer manufacturing, paving the way for innovation and improved processes in their respective fields.
Common Methods of Additive Layer Manufacturing
Understanding the various common methods of additive layer manufacturing (ALM) is essential for grasping how this technology unfolds in real-world applications. Each method comes with its own distinctive characteristics, advantages, and challenges while propelling forward innovation across sectors. Knowing these details paves the way for better selection in specific use cases, fostering advancements that meet particular engineering and design needs.
Fused Deposition Modeling (FDM)
Fused Deposition Modeling (FDM) holds a prominent position in the realm of 3D printing. In this technique, thermoplastic filaments are heated and extruded through a nozzle, where they are deposited layer by layer to create an object. The simplicity of the method is its hallmark; it allows users to easily adapt designs from software into physical models.
One notable strength of FDM is its accessibility. Many hobbyists and professionals alike rave about its affordability and versatility. For example, one can produce prototypes for product development without the hefty investment of an industrial setup. Nevertheless, it's vital to keep in mind its limitations, such as the surface finish and strength of the final product, which may not meet the demands of specialized industries.
Stereolithography (SLA)
Stereolithography (SLA) is a pioneering method that sets the stage for high-resolution 3D printing. This approach utilizes a UV laser to cure a liquid resin, solidifying it layer by layer. One of the remarkable qualities of SLA is its ability to produce incredibly intricate details and smooth finishes, making it ideal for industries that require high precision, like jewelry design and dental applications.
However, while SLA shines in quality, the materials used are often more costly, and the post-processing steps—such as cleaning and curing—can be somewhat tedious. This is something to consider when planning to implement SLA in a production pipeline, but for those needing accuracy, it’s hard to beat.
Selective Laser Sintering (SLS)
Selective Laser Sintering (SLS) is another robust method that opens doors to creating complex geometries. With SLS, a laser selectively fuses powdered materials—commonly nylon or polymers—into solid structures. This method stands out because it doesn't require support structures like some other printing techniques do, thanks to the surrounding powder that maintains the shape during the process.
The ability to create functional parts with durability is a clear advantage. In applications like aerospace and automotive, SLS allows for parts that have excellent mechanical properties. Yet, understanding the thermal properties of the materials is crucial for success in this method, as improper handling may lead to warping or decreased performance.
Binder Jetting
Lastly, binder jetting represents another fascinating method in the additive manufacturing toolkit. Instead of melting or curing materials, this technique selectively deposits a binding agent onto a powder bed. Once the printing finishes, the part is sintered in a furnace to achieve the lasting strength required for functional applications.
One of the standout benefits of binder jetting is its ability to produce multi-material and color parts, granting designers flexibility to a degree that is hard to find elsewhere. This can be particularly huge in rapid prototyping where visual appearances must match functionality. But, it's worth noting that the initial mechanical properties might be less robust, necessitating that firms consider use-case scenarios holistically.
"Additive layer manufacturing is not just about creating objects; it's about redefining the boundaries of what’s possible in design and production across various industries."
Applications of Additive Layer Manufacturing
Additive Layer Manufacturing (ALM) has rapidly gained traction across a myriad of sectors, transforming not just how products are made but also what they are made of. The applications of ALM extend beyond mere efficiency; they encompass innovations that bring personalization and new functionality to traditional manufacturing processes. From aerospace to healthcare, each application highlights distinct benefits. These advantages include resource conservation, design flexibility, and the capability to produce complex geometries that conventional methods would struggle to replicate. Through this section, we explore several key industries where ALM is making notable strides.
Aerospace Industry
Lightweight Components
In the aerospace realm, lightweight components are not just a luxury; they are a necessity. The reduction in weight can lead to significant fuel savings over time, which translates into substantial cost reductions for airlines. These components often utilize advanced materials that do not compromise strength, making them a popular choice in aircraft design. One unique feature of lightweight components produced through ALM is their ability to be tailored specifically to performance requirements without adding unnecessary bulk. However, the primary challenge lies in material science; some materials still face limitations in high-stress environments encountered in aviation.
Rapid Prototyping
Rapid prototyping in aerospace allows for swift iterations during the design phase. Engineers can create functional models rapidly, testing and refining designs before full-scale production. Notable here is the iterative nature of ALM, which lets teams explore a diversity of design concepts without incurring high costs associated with traditional prototyping methods. The key characteristic of rapid prototyping is speed — designers can have a model in hand within days instead of months. Nonetheless, this speed might come at the cost of not exploring all potential design avenues thoroughly.
Healthcare Innovations
Custom Implants
The medical field benefits greatly from the advent of custom implants produced through ALM. Each implant can be designed to fit the unique anatomy of a patient, maximizing comfort and efficiency. This capability represents a shift from one-size-fits-all solutions to personalized healthcare products. A distinctive feature of custom implants is their integration of patient imaging data into the production process, ensuring a precise match. A downside, however, is the regulatory challenges that can delay the implementation of such innovative solutions.
Bioprinting Applications
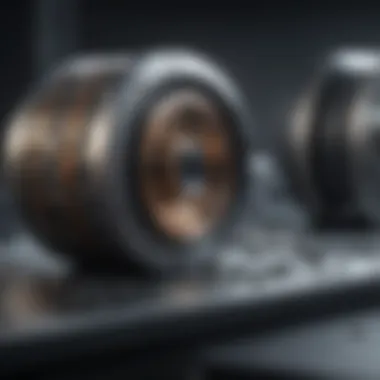
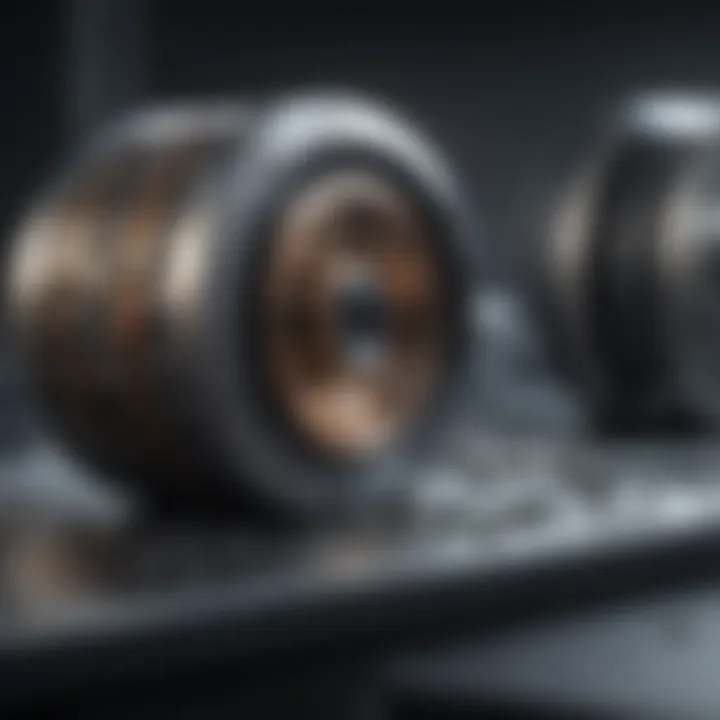
Bioprinting applications extend the possibilities of ALM into tissue engineering and regenerative medicine. This area focuses on creating living tissues that could one day replace damaged organs. Bioprinting is seen as a promising frontier in medicine, allowing for complex structures that mimic human tissues. One of the standout attributes of this technology is its ability to use bioinks composed of living cells, but there are notable challenges, such as ensuring the viability of cells during the printing process and navigating ethical concerns surrounding bioprinted tissues.
Automotive Advancements
Efficiency in Production
In the automotive industry, ALM significantly enhances efficiency in production. Traditional methods often involve multiple steps and considerable waste. In contrast, ALM builds parts layer by layer, reducing material waste and streamlining manufacturing processes. This efficiency can lower production costs and hasten the time-to-market for new vehicles. One challenge is the integration of ALM within existing production lines, requiring thoughtful consideration of logistics and existing equipment.
Custom Part Manufacturing
Custom part manufacturing has found a robust application in the automotive sector, where unique consumer preferences and specialized requirements are on the rise. ALM allows manufacturers to produce custom parts on-demand, eliminating the need for large inventories. A significant aspect of this process is its agility in responding to consumer demand. However, balancing customization with production volume can be tricky, often leading manufacturers to adjust their strategies.
Consumer Products
Personalized Goods
The consumer products marketplace is witnessing a trend towards personalized goods, thanks to ALM. Consumers today seek unique items that reflect their individual styles. With ALM, producers can easily create bespoke designs that cater to specific tastes while maintaining cost-effectiveness. A unique aspect is the opportunity for designers and consumers to collaborate directly. On the flip side, the mass production of highly customized products could lead to a dilution of brand identity.
Rapid Prototyping for Designers
Finally, rapid prototyping for designers in the consumer goods field allows for product development cycles that are faster than ever. Designers can produce prototypes that accurately depict the final product, enabling quick feedback and adjustments. This rapid approach fosters a culture of innovation as brands can enter the market with fresh ideas rapidly. However, the risk here is that speed might result in overlooking details that could enhance the final product's quality.
In summary, ALM applications are instrumental across various sectors, addressing unique challenges through innovative solutions. As technology advances, further possibilities will arise, propelling the idea of customization and efficiency into new dimensions.
Benefits of Additive Layer Manufacturing
Additive Layer Manufacturing (ALM) offers a plethora of benefits that significantly enhance modern production processes. Understanding these benefits is essential for anyone in the manufacturing sector or related fields. The unique approach of building objects layer by layer has revolutionized how products are designed and fabricated. This section explores the major advantages, focusing on design flexibility, material efficiency, and time savings that come with using ALM.
Design Flexibility
One of the standout features of ALM is its design flexibility. Unlike traditional manufacturing methods, which often impose constraints due to tooling and materials, ALM allows designers to push the creative envelope. The technology enables complex geometries that would have been impossible or prohibitively expensive to create otherwise. For instance, components with intricate internal structures can be designed to optimize weight without sacrificing strength.
The ability to create highly customized products is another appealing aspect. This is especially beneficial in industries like healthcare, where custom implants must fit the individual anatomy of patients. Designers can adapt models quickly based on specific needs, facilitating a more personalized approach to production. Simply put, the freedom to experiment with designs can lead to innovations that move the industry forward.
"With ALM, design is no longer held hostage by fabrication techniques. It’s the ultimate playground for engineers and designers."
Material Efficiency
Material efficiency is a significant advantage offered by Additive Layer Manufacturing. Traditional methods often involve subtracting material from a solid block, which can lead to substantial waste. In contrast, ALM builds objects layer by layer, using only the amount of material necessary for the finished product. This reduces scraps and resource consumption, making the process more environmentally friendly and cost-effective.
Moreover, ALM opens pathways for using advanced materials. Many techniques enable the blending of different materials in a single build process. For instance, aerospace components can utilize lightweight yet durable composites that wouldn't be feasible with conventional methods. The reduced material waste and innovation in materials translate into a clearer competitive edge for companies that adopt this manufacturing approach.
Time Savings
The third critical benefit is time savings in the production line. Traditional manufacturing often requires lengthy setup times and tooling changes, leading to prolonged production cycles. With additive manufacturing, the streamlined process can significantly cut down the time from concept to production.
Rapid prototyping is another facet contributing to time efficiency. Designers can quickly iterate on models, testing different variations with minimal delays. For example, a development team can create a prototype that can be modified overnight, ready for testing the next day. This agility in production is particularly advantageous in fast-evolving sectors like technology and fashion, where being first to market can dictate success.
Challenges in Implementing Additive Layer Manufacturing
Additive Layer Manufacturing (ALM) has undeniably revolutionized the way industries approach production and design. However, like any emerging technology, it carries its own set of challenges that must be navigated. Understanding these hurdles is crucial for organizations looking to adopt ALM for their projects, ensuring that they are well-informed and prepared for potential roadblocks. Three of the most pressing challenges include material limitations, regulatory concerns, and technology integration.
Material Limitations
The first hurdle, material limitations, can be likened to attempting to paint a masterpiece with only a handful of colors. While ALM offers a myriad of creative avenues, it does not currently provide an extensive range of materials suitable for all applications. Many widely used metals, polymers, and composite materials may not be easily compatible with existing additive processes. Each technique—be it Fused Deposition Modeling or Stereolithography—typically favors specific materials, which can impose constraints on design and functionality.
Moreover, the properties of the materials used in ALM can vary greatly from their traditionally manufactured counterparts. For instance, parts produced via Selective Laser Sintering may exhibit slightly lower tensile strength compared to those made through conventional methods. This inconsistency can be a sticking point in industries where specifications are extremely tight, such as aerospace or medical devices. Addressing these limitations involves continuous research into new materials and improving processing techniques, which often comes with a price tag.
Regulatory Concerns
Next up are the regulatory concerns that loom over ALM like a dark cloud. As businesses strive to push the envelope of innovation, they must also contend with an ever-evolving landscape of regulations and standards. Industries such as aerospace and healthcare have stringent guidelines in place designed to ensure safety and reliability. The challenge is often that these regulations were crafted when traditional manufacturing techniques reigned supreme, leaving gaps when it comes to the nuances of additively manufactured products.
The process of certifying 3D-printed components can be lengthy and complex. Manufacturers must produce a mountain of documentation demonstrating compliance with safety and quality standards, which can slow down the go-to-market timeline significantly. The lack of universally accepted regulations for ALM also complicates international trade. Businesses looking to expand must invest time and resources to navigate diverse regulatory frameworks, creating an additional barrier.
"Navigating the regulatory landscape is as sobering as it gets; a thorough understanding is needed to avoid potential pitfalls that can derail projects."
Technology Integration
Lastly, the integration of ALM technology into existing manufacturing systems poses a unique challenge. Companies are often reluctant to fully embrace this transformative technology if it doesn't seamlessly mesh with their current processes. The initial investment in additive machinery can be substantial, and this financial burden is complemented by the need for skilled personnel trained to operate the new equipment.
Integrating ALM into traditional workflows calls for a mindset shift. Employees may be accustomed to linear production processes, and introducing layer-by-layer additive techniques can require retraining and adjustment. Organizations need not only technological upgrades but also a cultural shift that promotes adaptability and a willingness to change established practices.
Ultimately, overcoming these challenges demands deliberate planning and strategic foresight. Companies must recognize that while Additive Layer Manufacturing presents tremendous opportunities, understanding and mitigating the challenges associated with its implementation is vital for ensuring successful adoption.
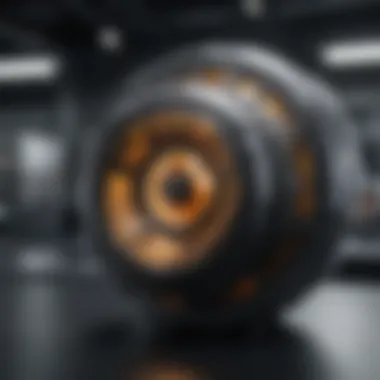

Future Trends in Additive Layer Manufacturing
The world of additive layer manufacturing (ALM) is evolving at a pace that can make your head spin. This section explores where the technology is headed and what it means for industries looking to integrate these advances into their operations. Keeping an eye on future trends is essential for companies aiming to innovate, remain competitive, and harness the full potential of ALM. With possibilities ranging from smarter processes to eco-friendly materials, the landscape of manufacturing is about to take a significant turn.
Advancements in Materials Science
At the heart of ALM's future lies materials science. The development of new materials gets folks in the industry really excited. Traditionally, additive manufacturing has relied on a limited range of plastics and metals. Now, we're seeing the emergence of cutting-edge materials that extend beyond the conventional.
These innovations include:
- Bio-compatible materials for medical applications, enabling the creation of implants and prosthetics that the human body can accept without issues.
- Composite materials that blend metals with polymers, enhancing strength without adding hefty weight, ideal for aerospace and automotive sectors.
- Thermal and electrical conductive materials opening up avenues for creating electronic components directly through 3D printing.
Such advancements aren’t just theoretical; they're currently impacting how products are designed and produced, pushing the envelope for customization in ways that were previously deemed impractical.
Integration with Smart Manufacturing
As manufacturing embraces smart technologies, the integration of ALM into this landscape is creating a fresh wave of potential. Think about the Internet of Things (IoT) and artificial intelligence (AI) meeting the capabilities of additive manufacturing. This synergy allows processes to become more efficient and adaptive.
For example:
- Real-time monitoring can track production quality, middleware facilitates immediate adjustments, and defect analysis with AI ensures that mistakes are caught before they escalate.
- Predictive maintenance using data from machines ensures down time is minimized, keeping production lines moving smoothly.
Ultimately, the fusion of smart manufacturing and ALM opens the door to a more collaborative and automated production environment, where human intervention is diminished, and productivity spikes.
Sustainability Initiatives
Sustainability is no longer just a buzzword; it’s an expectation. The manufacturing sector is witnessing a noticeable pivot towards greener practices. ALM shows promise in paving the road toward sustainability in various ways.
Consider these initiatives:
- Reduced material waste: Traditional subtractive manufacturing methods often lead to significant scrap. In contrast, additive manufacturing utilizes just the right amount of material, resulting in minimal waste.
- Recyclable materials play an important role, steering production choices toward eco-friendly options. Researchers are developing filaments and powders that can be reused or recycled.
- Localized production means parts can be manufactured nearer to their point of use, slashing the carbon footprint associated with transportation.
Incorporating these sustainability practices into ALM not only addresses environmental concerns but also aligns with consumer demand for more responsible production methods.
"Many industry leaders indicate that the future of manufacturing lies in a sustainable approach, taking into account economic, societal, and environmental impacts of production."
By keeping a finger on the pulse of these trends, businesses are better positioned to adapt and thrive in this dynamic field. The evolution of additive layer manufacturing will undoubtedly continue to reshape various industries, driving them forward with technology that is interconnected, efficient, and greener than ever before.
The Role of Additive Layer Manufacturing in Innovation
Additive Layer Manufacturing (ALM) serves as a cornerstone of innovation across multiple sectors, fundamentally changing the designs and production processes of various products. This section uncovers how ALM propels collaborative projects and fuels research and development, with an emphasis on its transformative contributions.
Driving Collaborative Projects
The dynamics of collaborative projects have shifted thanks to the versatile capabilities of ALM. When different entities such as universities, businesses, and research institutes come together, ALM provides a common platform that encourages experimentation and rapid iteration. Imagine a car manufacturer collaborating with a tech firm to create lightweight components. Using ALM, they can swiftly produce prototypes, test materials, and refine designs without the constraints of traditional manufacturing methods. This kind of synergy not only improves efficiency but also accelerates innovation timelines.
Moreover, collaborative projects are not limited to just two parties. By leveraging ALM in multi-stakeholder environments, teams can tap into diverse expertise from different fields. For instance, a healthcare initiative might bring together medical professionals, material scientists, and engineers to design custom implants specifically tailored for individual patients. The collaborative nature of ALM eliminates common bottlenecks, enabling faster decision-making and adaptability in the face of evolving challenges.
"The advancements in ALM technology are fostering a new era of collaborative innovation, where speed and efficiency go hand in hand."
Fueling Research and Development
Research and development (R&D) activities have received significant boosts from ALM technologies. Researchers seeking to test new hypotheses can employ Additive Manufacturing techniques to create complex geometries and structures that would be nearly impossible to realize through traditional methods. The ability to print intricate designs quickly allows scientists to explore concepts rapidly without spending copious amounts of resources.
In educational settings, ALM encourages hands-on learning and experimentation. Students can design and produce their own models, gaining firsthand experience with advanced manufacturing techniques. This practical knowledge is crucial as they prepare to enter a workforce increasingly reliant on innovative manufacturing practices.
A notable element of R&D in ALM is its applicability in diverse fields. For instance, in aerospace, engineers can utilize ALM to develop lightweight components that enhance fuel efficiency. In the biomedical field, researchers might focus on bioprinting to create tissue-like structures, thus paving the way for groundbreaking medical therapies.
In summary, ALM stands as a vibrant catalyst for innovation. By actively driving collaborative projects and enhancing R&D capabilities, it reshapes how industries approach design and development challenges, making the impossible tangible.
Closure
The conclusion of this article serves as a critical moment to reflect on Additive Layer Manufacturing (ALM) and its multifaceted role in modern industry. By appraising the various aspects discussed throughout the guide, including its fundamental principles, methods, and applications, one can appreciate the sweeping changes ALM has initiated across diverse sectors.
Assessment of Additive Layer Manufacturing's Impact
Additive Layer Manufacturing has fundamentally altered the landscape of manufacturing, leading to not only substantial advances in efficiency but also in customization and sustainability. This technology's build-up layer by layer offers exceptional freedom in design, enabling more complex geometries that were once infeasible with traditional methods. In the aerospace sector, for example, manufacturers have successfully created lightweight components that enhance fuel efficiency and performance. Similarly, in healthcare, the production of custom implants tailored to an individual's anatomy highlights ALM’s adaptability.
Yet, these benefits come with their own set of challenges. The material limitations faced by ALM can pose hurdles in ensuring quality and durability across different applications. Furthermore, varying regulations across industries must be navigated carefully to ensure compliance.
In summary, the impact of Additive Layer Manufacturing stretches beyond mere operational improvements; it redefines what is possible within manufacturing paradigms, offering new levels of design innovation and production efficiency.
Future Outlook
Looking ahead, the future of Additive Layer Manufacturing seems promising yet unpredictable. Ongoing advancements in materials science are likely to pave the way for new potential applications. With the development of biocompatible materials, the healthcare sector could soon expand its use of ALM beyond implants to creating tissues or even organs.
Additionally, integrating ALM with smart manufacturing systems could revolutionize supply chain dynamics, enabling on-demand production scenarios that significantly reduce waste. Sustainability initiatives will likely become central to future developments, as companies increasingly prioritize eco-friendly practices and reduce their carbon footprint.
Ultimately, the trajectory of Additive Layer Manufacturing suggests a continually evolving technology that will be instrumental in addressing the demands of tomorrow's manufacturing challenges. Its ability to promote innovation, efficiency, and sustainability marks it out as a cornerstone of future industrial practices.