Calibration of Wind Tunnel: Ensuring Precision in Aerodynamics
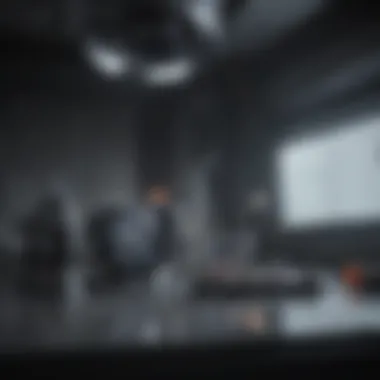
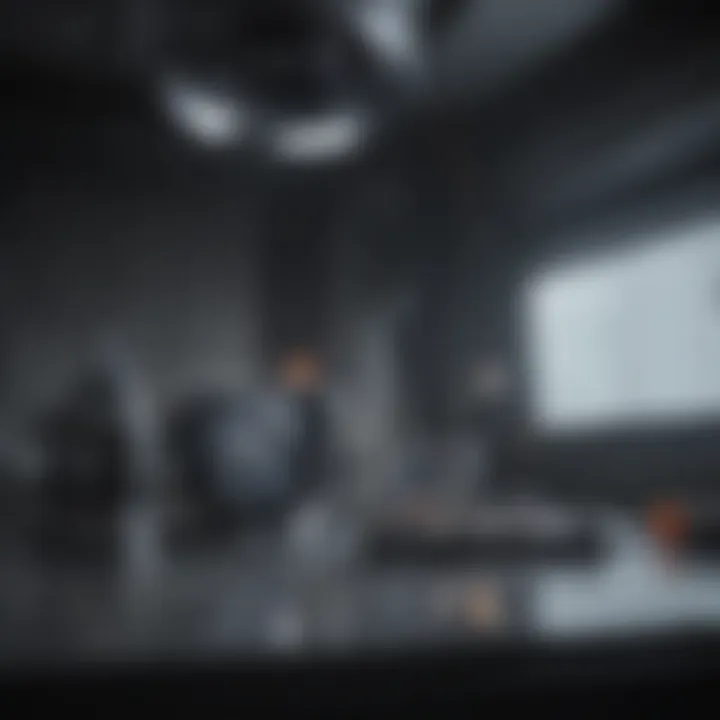
Intro
In the field of aerodynamic research, the calibration of wind tunnels holds significant importance. Wind tunnels are essential tools for testing models under controlled conditions, providing insights that cannot be acquired through computational methods alone. Accurate calibration ensures that the data obtained from these tests reflect true aerodynamic properties. Any deviations or inaccuracies can lead to flawed conclusions, which may ultimately impact designs and applications in various industries, such as aerospace and automotive.
This article delves into the processes and methods used for calibration, discusses challenges faced, and offers practical guidance for achieving the most reliable results. A thorough examination of fluid dynamics principles further enriches the understanding of the impact calibration has on aerodynamics.
Background and Context
Overview of the Research Topic
The calibration process in wind tunnel testing involves various parameters, such as airspeed, pressure, and temperature. These need to be accurately measured to ensure the environment mimics real-world conditions as closely as possible. As models are subjected to airflows, measuring the forces acting on them helps gauge their performance and stability. Calibration serves as a cornerstone for reliable and valid test results, influencing experimental integrity.
Historical Significance
Wind tunnels have evolved since their inception in the early 20th century. The original infrastructure was rudimentary, leading to the development of better techniques and technologies over time. The need for accurate flight simulation brought attention to calibration practices, which have been refined through numerous studies. Researchers have made significant contributions to enhance methodologies, enabling more precise aerodynamic research and development.
Key Findings and Discussion
Major Results of the Study
Throughout the analysis, it became evident that accuracy in calibration directly affects data quality. Variations in conditions or measurement errors can result in data that does not represent the actual performance of an object in flight. Effective calibration techniques, such as static and dynamic calibration methods, have shown to improve result reliability.
Detailed Analysis of Findings
- Static Calibration Methods: These involve adjusting the wind tunnel settings and measuring properties under fixed conditions. This method is fundamental for assessing baseline performance.
- Dynamic Calibration: This technique simulates actual flight conditions, capturing how models behave under varying speeds and angles.
- Common Challenges: Calibration often faces issues such as sensor drift, environmental variations, and model interference. Addressing these concerns is key in obtaining trustworthy data.
"Accurate calibration is the linchpin of effective wind tunnel testing, fundamentally influencing experimental outcomes and subsequent engineering decisions."
By synthesizing findings and offering insights into the calibration processes, this discussion aims to equip students, researchers, and professionals with the knowledge required to navigate this complex landscape efficiently. Understanding these key aspects is crucial for advancing aerodynamic testing methodologies and improving overall results.
Prelude to Wind Tunnel Calibration
Wind tunnel calibration is a critical process in the field of aerodynamic testing. It ensures the accuracy and reliability of the data obtained during experiments. Calibration involves correlating the measurements taken in the wind tunnel with known standards. This step is essential to validate the performance of models tested within these facilities.
The importance of calibration cannot be overstated. Without proper calibration, the results derived from wind tunnel experiments may lead to erroneous conclusions. Engineers and researchers rely on these results for the design and improvement of various applications, such as aircraft, automobiles, and even wind energy systems. An accurate representation of aerodynamic characteristics influences everything from safety regulations to energy efficiency, underscoring the necessity of rigorous calibration protocols.
In this analysis, we will explore the purpose of calibration. We will also review the historical context that shapes current practices in wind tunnel calibration. By understanding these elements, readers can gain insights into how these practices have evolved and why they remain foundational in aerodynamic research.
Purpose of Calibration
The primary purpose of wind tunnel calibration is to ensure that measurements taken are accurate and consistent. Calibration allows researchers to assess the performance of instruments and techniques used within the wind tunnel environment. This process typically includes several objectives:
- Validation of Measurement Devices: Instruments like Pitot tubes and anemometers must be tested against known standards to verify their precision.
- Correction of Systematic Errors: Calibration identifies any systematic errors related to environmental influences or equipment malfunctions.
- Enhancement of Experimental Accuracy: By calibrating, researchers can ensure that the data they collect is representative of actual aerodynamic conditions.
In wind tunnel testing, the results not only affect immediate experimental goals. They have long-lasting implications for broader aerodynamics fields. Reliable calibration procedures can lead to better design iterations and innovations.
Historical Context
The history of wind tunnel calibration can be traced back to the early developments in aerodynamics during the 19th and early 20th centuries. Pioneers like Sir George Cayley and Ludwig Prandtl laid the groundwork for theoretical aerodynamics, while practical applications began to emerge with the advent of dedicated wind tunnel facilities.
In the early days, calibration techniques were rudimentary. Basic measurement devices lacked sophistication and were often subject to significant errors. However, as understanding of fluid dynamics advanced, so did the approaches to calibration.
The introduction of modern measurement tools transformed calibration practices. Developments such as hot-wire anemometers and computerized data acquisition systems have dramatically enhanced measurement precision. As technology has advanced, ongoing research continues to refine calibration methods, allowing for high-fidelity data essential for today’s complex aerodynamic analysis.
"Accurate calibration fosters innovation in aerodynamics and shapes the future of engineering solutions."
Engaging with the processes of calibration has become more rigorous. Today’s professionals are tasked with not only calibrating instruments but also ensuring that their methodologies comply with international standards. This emphasis on quality assurance reflects the growing recognition of the importance of accurate aerodynamic data.
Understanding Wind Tunnel Dynamics
Understanding wind tunnel dynamics is crucial for effective aerodynamic testing and analysis. A comprehensive grasp of these dynamics allows engineers and researchers to optimize designs, enhance performance, and ensure safety in various applications. Wind tunnels serve as controlled environments where the behavior of air over various surfaces can be studied in detail, leading to insights that are often not achievable through other testing methods.
The dynamics within a wind tunnel involve the relationship between airspeed, pressure, and forces acting on models placed inside the tunnel. Knowledge of these interactions enables professionals to interpret results correctly and apply that information to real-world scenarios. Additionally, understanding how different factors affect airflow can greatly improve testing accuracy.
Basic Principles of Aerodynamics
Aerodynamics is the study of how air interacts with solid objects. The fundamental principles include the concepts of lift, drag, and thrust.
- Lift: The force that acts perpendicular to the direction of airflow, allowing aircraft to rise and stay airborne.
- Drag: The resistance force that acts in the opposite direction of airflow, which must be overcome for an object to move efficiently through air.
- Thrust: The force that propels an object forward, crucial in understanding how vehicles and aircraft move through the air.
These principles form the foundation of aerodynamics and are essential for comprehending how wind tunnel tests can predict real-world performance.
Types of Wind Tunnels
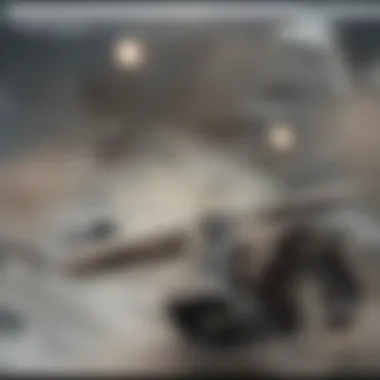
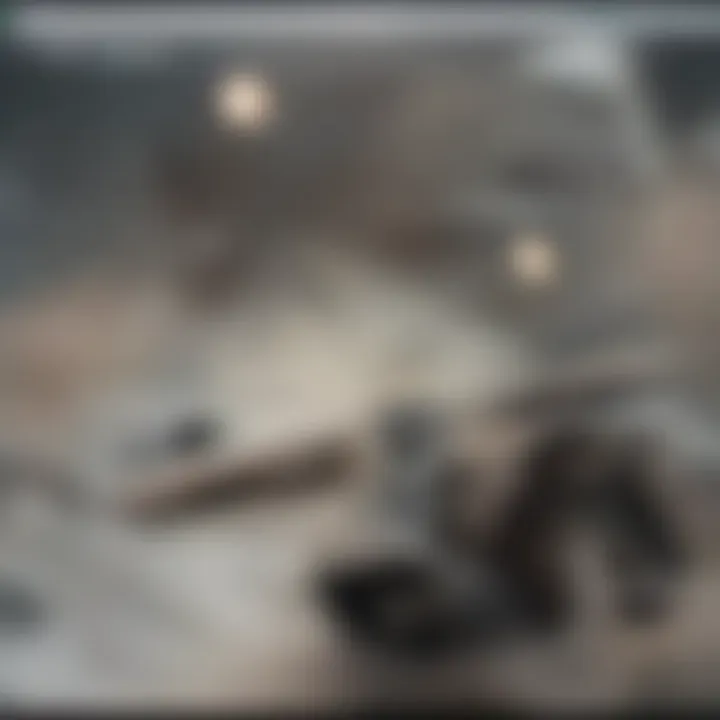
Wind tunnels can be categorized into two main types: open-circuit and closed-circuit.
Open-Circuit Wind Tunnels
Open-circuit wind tunnels are characterized by air flowing from the atmosphere into the test section and then exhausting back into the environment. This design allows researchers to test models with minimal interference from recirculated air, which can lead to cleaner data.
A key characteristic of open-circuit wind tunnels is their simplicity in construction. They are often less costly to build and maintain compared to closed-circuit systems. This makes them a popular choice for educational institutions and smaller research facilities.
However, the unique feature of open-circuit tunnels is their potential for fluctuating environmental conditions, as they are directly exposed to the external atmosphere. This can affect the consistency of test results, leading to challenges in calibration and data interpretation.
Closed-Circuit Wind Tunnels
Closed-circuit wind tunnels are designed to recycle air within a closed loop, which creates a stable testing environment. This design ensures that the conditions remain relatively constant, allowing for high-precision measurement and repeatability in tests.
The key characteristic of closed-circuit wind tunnels is their ability to manage flow more effectively. This results in less noise and turbulence, translating to more reliable data. They are therefore preferred for advanced research, especially in aerospace applications, where accuracy is paramount.
However, the unique feature of closed-circuit systems is the added complexity in their construction. They often require a higher initial investment and ongoing maintenance. But in many cases, the benefits outweigh the costs, particularly in contributions to aerospace engineering and automotive testing.
Understanding these types of wind tunnels is pivotal for selecting the right method for specific aerodynamic research objectives, shaping the future of engineering advancements.
Calibration Techniques and Procedures
Calibration techniques and procedures are critical components in the accurate functioning of wind tunnels. These processes ensure that the measurements obtained during tests are reliable and repeatable. Reliable data underpins any aerodynamic research, assisting engineers and scientists in making informed decisions. Various techniques are employed, each with its own distinct advantages and challenges. This section delves into the primary measurement instruments and standard calibration methods utilized in wind tunnel calibration.
Measurement Instruments and Devices
Pitot Tubes
Pitot tubes are essential instruments for measuring fluid flow velocity. Their main function is to assess dynamic pressure, which can be converted to velocity measurements. The key characteristic of pitot tubes is their simplicity and directness. They are popular in aerodynamic testing because of their durability and ease of use.
A unique feature of pitot tubes is their ability to provide continuous measurements, making them highly beneficial during long-duration tests. However, one disadvantage is their inherent susceptibility to flow disturbances, which can impact accuracy. Ensuring proper positioning within the test section is vital to mitigate errors arising from this factor.
Hot-Wire Anemometers
Hot-wire anemometers serve as advanced tools for measuring small variations in air velocity. They operate by detecting heat transfer from a heated wire to the surrounding fluid as it flows past. The notable characteristic of hot-wire anemometers is their high sensitivity, allowing for precise measurements even in low-speed wind conditions. This sensitivity makes them a favored choice for research requiring fine resolution of velocity profiles.
The unique feature of hot-wire technology lies in its capability to detect rapid fluctuations in velocity, which is especially useful in turbulent flow studies. On the downside, they require careful calibration and frequent maintenance, as the heated wire can degrade over time, affecting measurement accuracy.
Force Balances
Force balances are critical for measuring the aerodynamic forces acting on models in the wind tunnel. They provide an accurate assessment of lift, drag, and side forces, which are essential for understanding aerodynamic performance. The primary characteristic of force balances is their precision in measuring forces across a wide range of conditions. This makes them indispensable in both academic and industrial applications.
A standout feature of force balances is their ability to integrate with various data acquisition systems, facilitating real-time analysis. However, one limitation is the complexity involved in their setup and calibration, which necessitates a sophisticated understanding of the required configurations.
Standard Calibration Methods
Static Calibration
Static calibration is a foundational method employed to ensure that measurement devices provide accurate readings under zero airflow conditions. This technique is vital for establishing a reference point for further measurements. The primary characteristic of static calibration is its straightforward methodology, allowing for easy replication across different setups.
The unique feature of this method is that it effectively isolates the measurement device from dynamic influences, providing pure static pressure readings. However, static calibration does not account for changes in conditions that may arise during actual operational scenarios, thus limiting its comprehensive application.
Dynamical Calibration
Dynamical calibration, as opposed to its static counterpart, involves the evaluation and adjustment of measurement systems under operational conditions. This method is crucial for testing the response of instruments during practical applications. The key characteristic of dynamical calibration is its ability to simulate real-world flow conditions, making it particularly valuable for validating performance.
A critical advantage of dynamical calibration is its relevance to everyday testing scenarios, ensuring that the instruments perform effectively in dynamic environments. However, it is often more complex and time-consuming, requiring extensive resources and careful planning to execute properly.
Correct calibration practices are necessary to guarantee that data generated in wind tunnel tests are valid and valuable for aerodynamic research, which highlights the significance of both static and dynamical calibration techniques.
Challenges in Calibration
Calibration of wind tunnels encompasses various challenges, all of which can influence the accuracy of aerodynamic testing results. Understanding these challenges is crucial for improving methodologies and enhancing the reliability of data obtained from such tests. In this section, we will delve into three primary challenges: environmental influences, instrument variability, and user handling errors. Each of these elements presents unique considerations that merit attention as researchers and engineers seek to optimize their processes.
Environmental Influences
Environmental factors play a significant role in wind tunnel calibration. Temperature, humidity, and pressure fluctuations can alter measurements taken during testing. For instance, changes in temperature can affect air density, which in turn influences airflow velocity and aerodynamic forces experienced by the model. Variations in humidity can modify the viscosity of the air, leading to discrepancies in wind speed measurement.
To mitigate the impact of these external conditions, it is essential to maintain a controlled environment within the wind tunnel. This can involve employing advanced climate control systems to stabilize temperature and humidity levels during testing. Additionally, utilizing real-time monitoring systems can help detect environmental changes, allowing for quick adjustments to calibration parameters.
Instrument Variability
Another significant challenge in calibration stems from instrument variability. Different instruments may have varied sensitivities and inherent inaccuracies that can skew results. For example, even identical Pitot tubes can yield different measurements if they are manufactured with subtle differences in design or material.
To address instrument variability, it is vital to perform regular maintenance and calibration checks of all measurement devices. Establishing a standardized protocol for calibration can minimize discrepancies across instruments. Moreover, adopting high-precision instruments such as digital instruments over analog ones can improve measurement reliability.
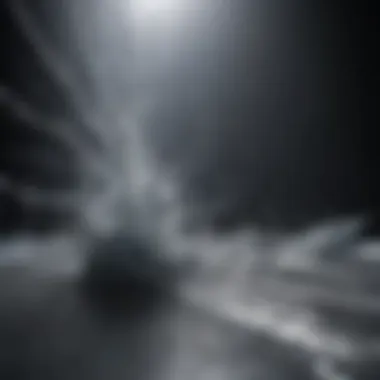
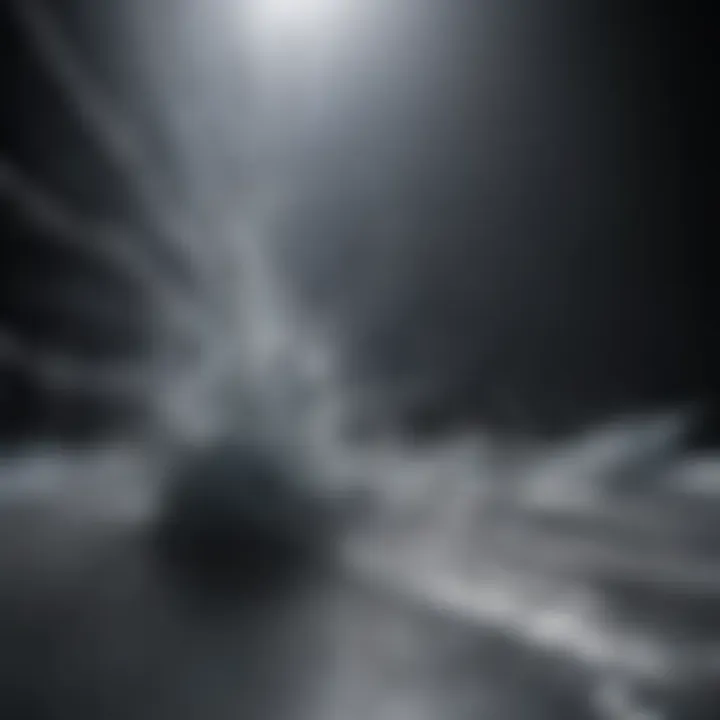
User Handling Errors
User handling errors are often an overlooked challenge in wind tunnel calibration. The way instruments are operated and maintained can introduce human error into the calibration process. Misalignments, incorrect settings, and improper data recording can significantly impact test outcomes. Researchers must ensure that individuals handling instruments are well-trained and adhere strictly to established protocols.
Organizing regular training sessions and implementing checklists can enhance accuracy during data collection. Additionally, promoting a culture of attention to detail and fostering a collective understanding of potential errors can substantially minimize the likelihood of user-induced complications.
"Challenges in calibration are not just minor hurdles; they are critical barriers to achieving precision in aerodynamic research. Addressing them effectively is a step towards advancing the field."
Overcoming these challenges requires a multifaceted approach that encompasses technical, procedural, and human factors. By understanding and addressing these issues, researchers and engineers can enhance the calibration process and ultimately produce more accurate aerodynamic data.
Mathematical Models in Calibration
Mathematical models play a critical role in the calibration of wind tunnels. They help researchers and engineers understand complex fluid dynamics and predict airflow behavior accurately. In this section, we will delve into the significance of mathematical models, examining their benefits and implications in the calibration process.
Through modeling, it is possible to simulate various conditions that might be challenging to reproduce in live tests. This flexibility can lead to cost and time savings while ensuring high accuracy in results.
By employing well-established models, engineers can refine their calibration techniques, approaching precision in measurements. Moreover, they provide a framework for understanding the interactions between different elements within the wind tunnel, such as the effects of test section geometry on flow characteristics.
Mathematical models thus serve as invaluable tools in improving the efficiency and reliability of wind tunnel calibrations.
Governing Equations of Fluid Dynamics
The governing equations of fluid dynamics form the foundation upon which mathematical models are built. These fundamental equations include the Navier-Stokes equations, which adapt to various flow conditions. Each equation accounts for factors such as viscosity, pressure, and velocity.
Understanding these equations allows engineers to predict how air moves over surfaces, which is crucial during calibration. Accurate results from wind tunnel tests aid in the validation of experimental data and the optimization of designs. It is essential to grasp these principles to ensure the success of any aerodynamic testing endeavor.
In addition, the continuity equation ensures mass conservation, while the momentum equations focus on force balance in the fluid. Together, they highlight how alterations in one variable can affect overall system dynamics, emphasizing the need for precise calibration.
Numerical Simulation Techniques
Numerical simulation techniques utilize computational methods to solve the governing equations of fluid dynamics. These techniques, such as Computational Fluid Dynamics (CFD), allow the analysis of wind tunnel flows under various scenarios. Through simulations, one can visualize airflow and investigate how different designs perform without needing extensive physical testing.
Some common numerical methods include:
- Finite Volume Method (FVM): This method divides the fluid domain into smaller control volumes, conserving fluxes across each volume's boundaries.
- Finite Element Method (FEM): Leveraging mesh elements, FEM is particularly useful in complex geometries, providing detailed flow field insights.
- Lattice Boltzmann Method (LBM): This method simulates fluid dynamics on discrete lattice points, allowing for intricate flow interactions and behaviors.
These numerical techniques aid in enhancing the accuracy of calibration, often identifying potential discrepancies that might remain undetected during experimental measurements.
"Numerical simulations are not just a support tool; they are integral to making informed decisions in wind tunnel testing, bridging theory and practical application."
Quality Assurance and Best Practices
In wind tunnel calibration, Quality Assurance and Best Practices are crucial for ensuring reliability and accuracy of test results. It is essential to follow systematic processes that validate the calibration methods employed, which ultimately affects the integrity of aerodynamic research. Quality assurance entails defining a set of standards and procedures that are consistently followed during the calibration process. This systematic approach contributes to consistent and repeatable results, allowing researchers to draw valid conclusions from their experiments.
Documentation and Protocols
Documenting every calibration step ensures that no critical information is lost. Maintaining detailed records helps in tracking adjustments made to the calibration methods. It enables repeatability and serves as a reference for future calibrations. Proper documentation includes:
- Calibrated Equipment List: All instruments used must be recorded, including their calibration status.
- Calibration Dates: Regular logs of when calibrations are completed help in scheduling future checks.
- Calibration Procedures: Clear descriptions of each step in the calibration process allow others to replicate the methods.
- Results: Documenting outputs from each calibration test is essential to monitor trends over time.
Additionally, these protocols allow for easier identification of discrepancies. They provide a framework for accountability among the personnel involved.
Routine Calibration Checks
Routine calibration checks are necessary to maintain the reliability of the wind tunnel's performance. The frequency of these checks depends on several factors, such as the type of wind tunnel and the specific demands of the testing program. Common practices for routine checks include:
- Weekly Inspections: Regular visual checks can identify visible wear and tear on instruments.
- Monthly Calibration: For high-precision measurements, monthly calibration ensures ongoing accuracy.
- Post-Modification Checks: Anytime there is a change in setup, a calibration check must be performed.
These checks not only ensure the operational state of the instrumentation but also provide assurance to the researchers regarding the data being collected. By adhering to a schedule, teams can detect issues before they lead to substantial data errors, thereby maintaining trust in the research outcomes.
"A systematic approach in documenting and routine checks eliminates ambiguity and enhances the reliability of wind tunnel data."
Case Studies and Practical Applications
Examining case studies in the realm of wind tunnel calibration reveals critical insights into the practical applications of aerodynamic testing. These real-world examples not only demonstrate the significance of calibrated environments but also underscore the attention needed when applying theoretical principles in practical scenarios. The benefits of referencing case studies in calibration processes include a deeper understanding of challenges faced, methods employed, and outcomes achieved, which can guide future research efforts and industrial practices. By linking calibration techniques to distinct applications, researchers and engineers enhance their methodologies and address specific industry needs.
Aerospace Engineering
In aerospace engineering, precision in performance testing is crucial. Wind tunnels serve as essential tools for analyzing how air flows around aircraft designs. Case studies focused on wind tunnel calibration in this sector exemplify how the fidelity of aerodynamic data directly influences design and safety outcomes. A significant example arises from the calibration efforts at NASA Langley Research Center, where advancements in static and dynamic calibration improved the accuracy of drag and lift force measurements. This, in turn, led to enhanced flight performance criteria, reducing the incidence of design flaws and promoting aircraft safety.
Points of focus in these case studies often include:
- The calibration process of different test conditions, recreating real-flight scenarios.
- The integration of advanced sensor technology to boost measurement accuracy.
- The iterative testing phases that lead to the refinement of prototypes based on wind tunnel results.
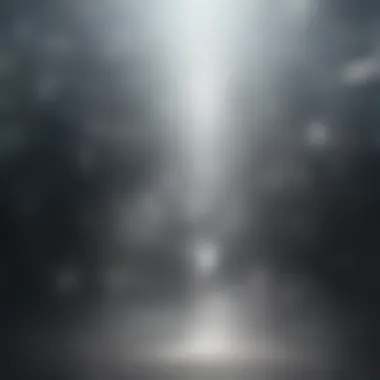
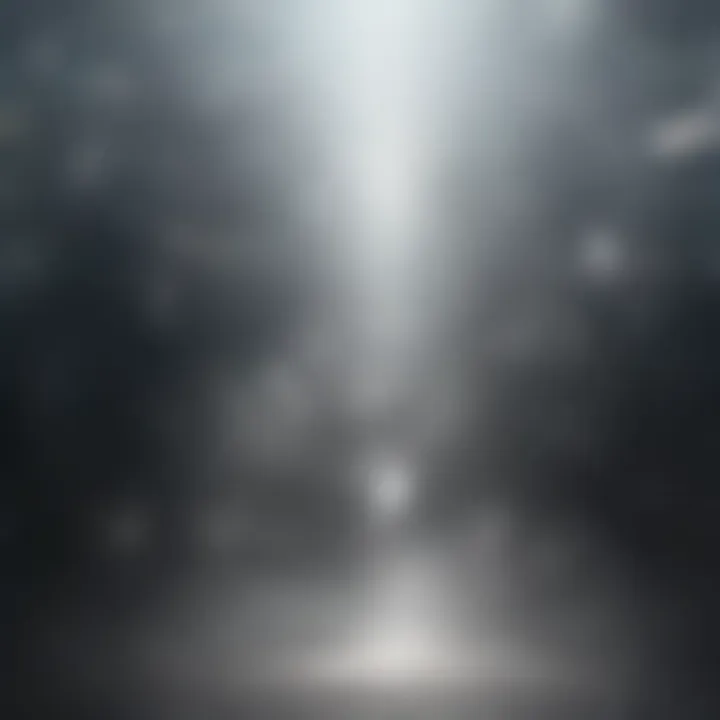
Results derived from practical applications influence future aircraft designs and optimize aerodynamic profiles, thus contributing to significant advancements in the aerospace sector.
Automotive Testing
Automotive testing employs wind tunnels primarily to refine vehicle designs for maximum aerodynamic efficiency. Case studies in this domain illustrate the importance of calibration in achieving precise measurements of drag coefficients and lift forces—key factors in vehicle performance and fuel efficiency. A notable instance is seen in the calibration strategies utilized by Volkswagen in the development of their ID.4 electric vehicle, where accurate wind tunnel testing played a pivotal role in achieving desired aerodynamics for energy efficiency.
Some vital elements considered in automotive testing case studies include:
- The calibration of closed-circuit wind tunnels that minimize external disturbances, ensuring focus on the vehicle under test.
- The use of laser-based measurement systems to capture air flow patterns with high fidelity.
- The adaptive calibration techniques that adjust for varying vehicle sizes and shapes, allowing for broader applications across various vehicle types.
These case studies not only validate the calibration processes but also highlight the economic benefits derived from improved aerodynamic designs, directly correlating to better fuel consumption and performance metrics.
"Effective calibration in both aerospace and automotive applications leads to innovations that significantly enhance safety and efficiency."
Through rigorous testing and precise calibration methods, engineers can adapt quickly to evolving design standards and consumer demands, thus advancing the fields of aerospace and automotive engineering.
Emerging Technologies in Wind Tunnel Calibration
Emerging technologies play a pivotal role in enhancing the accuracy, efficiency, and effectiveness of wind tunnel calibration. As researchers continue to push the boundaries of aerodynamic testing, these new developments offer substantial benefits. They not only refine existing techniques but also introduce innovative methodologies that address the complexities of modern aerospace and automotive testing.
Advances in Sensor Technology
The rise of advanced sensor technology is transforming wind tunnel calibration. Traditional sensors, while effective, often have limitations in precision and data integration. Modern innovations, such as micro-electromechanical systems (MEMS) and advanced pressure sensors, provide enhanced accuracy.
- Precision Measurement: These new sensors minimize errors in data collection by providing high-resolution measurements. For example, Pitot tubes paired with advanced sensors deliver more reliable velocity readings.
- Real-Time Data Acquisition: With the advancement in wireless technology, it is possible to collect data in real-time, enabling immediate adjustments during the testing phase. This increases the efficiency of the calibration process.
- Integration Capabilities: New sensors can easily integrate with calibration software, allowing researchers to visualize and analyze data instantaneously. This capability maximizes the effectiveness of the calibration effort.
The implications of these advancements are profound. Enhanced sensor technology leads to more accurate models and improved predictive capabilities in aerodynamic studies, resulting in better designs in aerospace and automotive engineering.
Integration of Machine Learning
Machine learning is another transformative element in wind tunnel calibration. This field of artificial intelligence is utilized to analyze complex datasets and optimize calibration procedures.
- Data Analysis: Machine learning algorithms can sift through vast amounts of calibration data to identify patterns and anomalies. This capability is essential for refining calibration processes and strategies.
- Predictive Modeling: By leveraging historical calibration data, machine learning models can predict outcomes under various testing conditions. This predictive power allows researchers to anticipate issues and make necessary adjustments in advance.
- Adaptive Calibration: Machine learning can contribute to adaptive calibration techniques that adjust parameters in real time based on feedback from the system. This dynamic capability enhances overall accuracy and reduces time spent on calibration draws.
As emerging technologies continue to evolve, both sensor advancements and machine learning integration will become integral to wind tunnel calibration practices. They streamline processes, enhance data precision, and ultimately support innovations that shape the future of aerodynamic research.
Future Directions in Wind Tunnel Research
The calibration of wind tunnels is a rapidly evolving field. As technology advances, so does the need for innovative methodologies in research and testing. Future directions in wind tunnel research are significant not only for improving experimental accuracy but also for enhancing the overall understanding of aerodynamics. This section aims to highlight essential elements, benefits, and considerations that will shape the future of wind tunnel calibration.
Interdisciplinary Approaches
Interdisciplinary approaches are crucial in advancing wind tunnel research. Fields such as mechanical engineering, physics, computer science, and materials science converge to enhance aerodynamic testing. By integrating insights from various disciplines, researchers can develop more sophisticated models and tools.
Consider a collaborative project between mechanical engineers and data scientists. The engineers bring a wealth of knowledge about the physical properties of airflow, while the data scientists provide expertise in processing large datasets from test runs. Together, they can create predictive models that allow for better analysis of wind tunnel experiments.
Adopting interdisciplinary techniques leads to:
- Improved accuracy in simulation results
- Enhanced analytical methods for data interpretation
- More robust methodologies for experimental design
As researchers continue to break down the barriers between disciplines, the potential for innovation in wind tunnel calibration becomes limitless.
Global Collaborations
In today’s interconnected world, global collaborations are more vital than ever in advancing wind tunnel research. By pooling resources and expertise from institutions around the world, researchers can tackle complex challenges that exist in the aerodynamics field. International partnerships can lead to standardization efforts across different facilities, which enhances the consistency and reliability of calibration processes.
Collaboration between universities, research institutions, and industries can result in:
- The sharing of best practices and methodologies
- Development of standardized procedures for calibration
- Increased funding opportunities for large-scale projects
As the complexities of aerodynamics grow, so does the necessity for a unified global approach to research. Greater collaboration may yield insights that would otherwise remain undiscovered in isolated environments.
The integration of interdisciplinary approaches and global collaborations is essential for the next phase of wind tunnel calibration research, fostering innovation and improving the reliability of aerodynamic testing.
Epilogue
In summary, the conclusion of this article encapsulates essential insights gained throughout the exploration of wind tunnel calibration. Calibration is not just a procedural necessity; it is a critical element that shapes the accuracy and reliability of aerodynamic research. A well-calibrated wind tunnel provides data that is foundational for any aerodynamic study, impacting everything from aircraft design to automobile performance assessments. The significance of calibration extends beyond mere compliance with protocols; it speaks to the integrity of research outcomes and influences practical applications in engineering.
Summary of Key Insights
The key takeaways from this article on wind tunnel calibration encompass various vital aspects:
- Calibration Importance: It ensures reliable results, which are indispensable for informed engineering decisions.
- Techniques and Methodology: A gamut of methods is available, including static and dynamical calibration, each with specific use cases.
- Challenges: Factors like environmental influences and instrument variability can significantly affect calibration results, thus requiring vigilant monitoring.
- Emerging Technologies: Advances in sensor technology and the integration of machine learning can potentially revolutionize calibration processes, making them more efficient and accurate.
These insights underline how crucial proper calibration is to the field of aerodynamic research, influencing both theory and practice.
Implications for Future Research
Future research in wind tunnel calibration holds numerous promising avenues. As technology progresses, researchers must strive to harness cutting-edge tools to improve calibration accuracy. The potential integration of machine learning represents a significant leap forward, allowing for real-time data analysis. Additionally, interdisciplinary approaches, which combine insights from multiple fields, could enrich the calibration process itself.
- Investigating New Materials: Exploring innovative materials for wind tunnel construction may lead to advances in measurement accuracy.
- Global Collaborations: Encouraging international partnerships can facilitate knowledge sharing and standardization in calibration methods.
- Focus on Sustainability: Research should also consider the environmental impact of wind tunnel operations, emphasizing sustainable practices in testing.