An In-Depth Examination of Conical Bearings
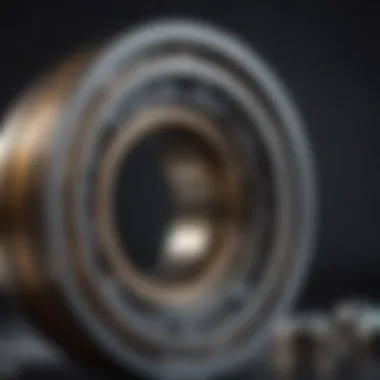
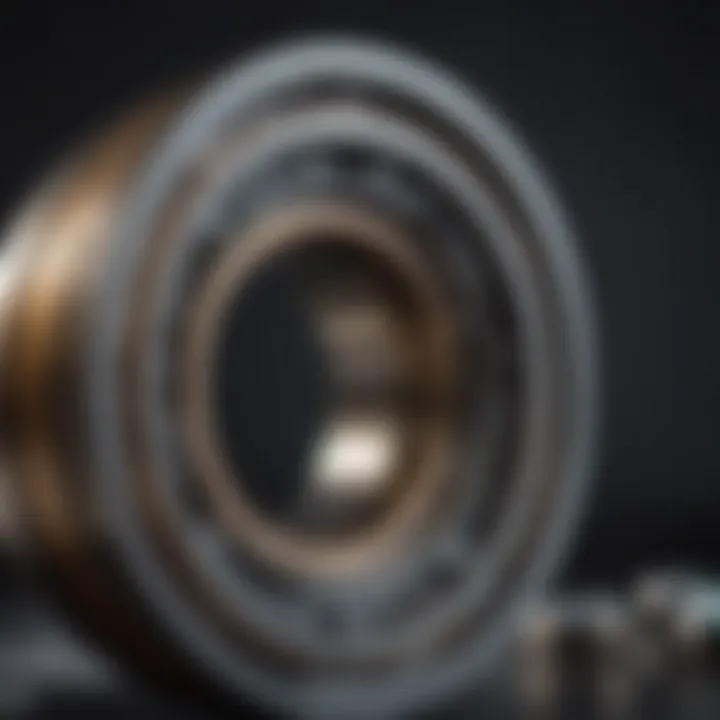
Intro
Conical bearings play a crucial role in various mechanical systems. They are designed to handle both radial and axial loads, making them essential for various applications. Understanding how these bearings work, their design, and their function is vital for anyone involved in engineering or mechanical maintenance.
This article explores the complex nature of conical bearings. It will provide insight into their historical development, materials used in their manufacture, and their applications across different industries. By the end of this article, readers will gain a profound comprehension of conical bearings and their practical importance.
Background and Context
Overview of the Research Topic
Conical bearings, also known as tapered roller bearings, are a specific type of rolling-element bearing. They consist of an inner and an outer race, with tapered rollers in between. This geometric design allows for effective load management, especially in scenarios where heavy loads are present. Their ability to accommodate combined loads makes them a preferable choice in applications such as automotive, aerospace, and industrial machinery.
Historical Significance
The invention of conical bearings dates back to the early 20th century. Initially used in industrial machinery, their application expanded rapidly with advancements in vehicle technology. The design has evolved significantly since its inception. Today, these bearings are produced with innovative materials and manufacturing processes, enhancing their performance and durability. The historical evolution of conical bearings is an important aspect of mechanical engineering, as it reflects the need for better performance in an increasingly demanding industrial landscape.
"Conical bearings are not just mechanical components; they represent a significant leap in engineering practices, facilitating advancements across multiple industries."
Key Findings and Discussion
Major Results of the Study
The study of conical bearings reveals several key insights:
- Load Distribution: The tapered shape allows for more effective load distribution, reducing wear and tear.
- Alignment: They provide better alignment and stability, which is critical in high-speed applications.
- Material Efficiency: The choice of materials, such as high-carbon chromium steel, contributes to their longevity and reliability.
Detailed Analysis of Findings
The advantages afforded by conical bearings stem from their design. The tapering geometry not only aids in load distribution but also minimizes friction. This feature is particularly beneficial in high-load scenarios. Furthermore, advancements in material science have led to the utilization of stronger and lighter materials, resulting in bearings that are both efficient and durable.
In terms of applications, conical bearings are widely used in automotive wheel hubs, conveyor systems, and even in high-precision machinery. Their versatility highlights their importance across various sectors.
Ending
Understanding conical bearings is essential for students, researchers, and professionals. Their design, function, and applications reflect significant advancements in mechanical engineering. This article aims to bridge theoretical knowledge with practical application, ensuring readers are well-equipped to utilize conical bearings effectively in their respective fields.
Prolusion to Conical Bearings
Conical bearings are an essential component in various mechanical systems, enabling effective load handling and ensuring smooth operation in moving parts. Understanding this type of bearing is pivotal for engineers and designers who aspire to achieve optimal performance in machinery. They offer unique features that differentiate them from other bearing types. Consequently, their significance cannot be overstated in any discussion focused on bearing technologies.
Definition and Overview
Conical bearings, also known as tapered roller bearings, consist of tapered inner and outer raceways. The rolling elements are shaped like truncated cones or rollers, allowing them to accommodate both radial and axial loads. This distinctive design enhances load distribution, enabling the bearing to endure greater weight and stress compared to standard designs.
These bearings are particularly notable for their versatility across various applications, making them a crucial choice in industries ranging from automotive to aerospace. Understanding their physical structure and mechanical functions provides insight into their performance criteria and applications, proving essential for academic and professional audiences alike.
Historical Context and Evolution
The origin of conical bearings dates back to the early days of modern engineering. They emerged as a solution to the limitations faced by traditional bearings when it came to load capacity and alignment. Historical records indicate that the first patents for tapered roller bearings were filed in the early 20th century. These designs evolved through innovation and advancements in materials science, leading to today's highly specialized conical bearings.
Over the years, the manufacturing processes have refined, incorporating precision techniques that further increase the reliability and efficiency of conical bearings. This evolution is intrinsic to the modern engineering landscape. Understanding these historical developments allows one to appreciate the complex engineering principles behind the designs we utilize today.
The Structure of Conical Bearings
The structure of conical bearings plays a vital role in their performance and functionality. Understanding the elements that compose these bearings allows for better appreciation of their application across various industries. This section elaborates on the composition and design of conical bearings, including their different types. Specific elements such as the inner and outer races, rolling elements, and cage design are critical parts that contribute to the effectiveness of these bearings in load distribution and alignment.
Composition and Design
Inner and Outer Races
The inner and outer races are essential components of conical bearings. They provide the surface along which the rolling elements operate. The inner race has a conical surface that allows for effective load distribution. This design is beneficial because it can accommodate both axial and radial loads effectively. An important characteristic of this setup is the precise shape and alignment, which minimizes friction and wear. This is crucial for longevity and efficiency in applications.
One unique feature of the inner and outer races is their taper design. This allows for smooth interaction with the rolling elements, promoting better contact and durability. However, improper alignment during installation can lead to premature failure. Therefore, precise installation and maintenance processes are vital.
Rolling Elements
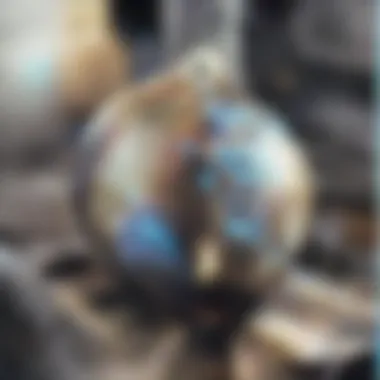
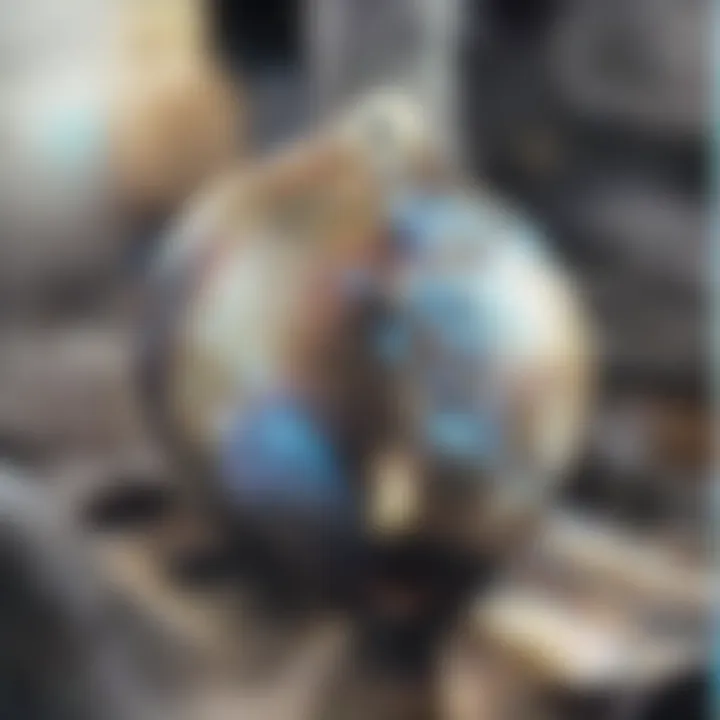
The rolling elements in conical bearings, typically balls or rollers, are responsible for the movement and load-bearing capacity. Their shape and surface quality directly affect how loads are distributed. These elements are designed to minimize friction, allowing for smoother operation. A notable characteristic of rolling elements is their ability to handle both axial and radial loads efficiently. This versatility makes them ideal for many engineering applications.
Rolling elements often vary in size and material, with each choice affecting performance. For instance, larger rolling elements can support heavier loads, but they may also increase friction under certain conditions. Thus, selecting the appropriate rolling elements is essential for achieving the desired performance.
Cage Design
Cage design is another critical aspect of conical bearings. The cage, or separator, maintains the spacing between the rolling elements and guides them as they move. This design helps in reducing friction and increasing the stability of the bearing. A key characteristic of the cage is its material and shape, which influence the overall weight and efficiency of the bearing.
In many cases, modern cages are made from lightweight materials that withstand high temperatures and pressures. They ensure consistent performance over time, which is vital for operational efficiency. However, if the cage becomes damaged, it can lead to misalignment and uneven load distribution, which can compromise the bearing's performance.
Types of Conical Bearings
Conical bearings come in several types, designed to meet different mechanical needs. The key types include single row, double row, and four row conical bearings, each with unique characteristics and applications.
Single Row Conical Bearings
Single row conical bearings are the simplest type, consisting of one row of rolling elements between the inner and outer races. Their primary advantage is their ability to withstand moderate axial and radial loads, making them a popular choice for many applications. They are particularly effective in setups with limited space where the load is not excessive.
However, their capacity is limited compared to other designs. In applications with higher loads, they may not perform as efficiently.
Double Row Conical Bearings
Double row conical bearings incorporate two rows of rolling elements. This design allows for a greater load capacity and more stability. This is a beneficial option for heavy-duty applications where space is still a consideration. The enhanced load-carrying capability makes them suitable for industries such as automotive and manufacturing.
Nonetheless, the increased complexity can lead to higher manufacturing and maintenance costs.
Four Row Conical Bearings
Four row conical bearings have four rows of rolling elements, providing even greater load capacity. They are primarily used in specialized applications, such as in heavy machinery and construction equipment. Their design leads to improved stability and load distribution, which can enhance the lifespan of machinery.
However, they are more expensive and complex, making them less common in typical settings.
Conical bearings are crucial for ensuring efficient performance in various mechanical systems, with their structure directly influencing load handling capabilities.
Functionality and Mechanics of Conical Bearings
Conical bearings are crucial components in various machinery, playing an essential role in load support and motion transmission. By understanding their functionality and mechanics, one can appreciate their significance in ensuring the efficiency and reliability of mechanical systems. This section explores the load distribution characteristics and the methods for handling both radial and axial loads, key aspects of conical bearing performance.
Load Distribution Characteristics
Conical bearings are designed to handle loads effectively. Their unique geometric arrangement allows for a balanced distribution of forces. The conical shape facilitates a contact line between the rolling elements and the races, which spreads the load across multiple points. This is particularly significant in applications requiring high precision and stability.
One of the main advantages of conical bearings is their ability to manage combined loads. The tapered design allows for transmitting both radial and axial loads. This capability is paramount in scenarios such as automotive and aerospace applications, where fluctuating loads can adversely affect performance.
"The effectiveness of load distribution is a key factor in the longevity and reliability of conical bearings."
In addition, the load capacity of conical bearings can vary depending on the design and construction materials. The efficiency of load sharing among the rolling elements helps in reducing wear and increasing the lifespan of the bearings.
Radial and Axial Load Handling
Efficiently managing radial and axial loads is critical in any bearing’s functionality, and conical bearings excel in this area. Radial loads are perpendicular to the shaft, and axial loads are parallel. This dual capability makes conical bearings versatile in various mechanical contexts.
The inherent design allows conical bearings to stabilize both load types while minimizing friction. When installed correctly, these bearings support a significant amount of radial load while also accommodating axial forces. For instance, in automotive wheel hubs, these bearings allow for smooth rotation of the wheel while supporting the vehicle's weight.
Moreover, the arrangement of the rolling elements helps maintain alignment, which is vital for high-speed applications. This alignment reduces misalignment issues and potential failures, ultimately contributing to the machinery's operational integrity.
Materials Utilized in Conical Bearings
Understanding the materials used in conical bearings is crucial because they significantly influence the performance and durability of these components. Each material offers distinct advantages and drawbacks, which can affect the overall efficiency of the machinery. When selecting materials, considerations such as strength, wear resistance, and environmental factors come into play. The choice of material can determine the operational life of the bearing and its effectiveness in handling loads.
Common Materials
Steel
Steel is one of the most common materials used in the production of conical bearings. It possesses a high tensile strength, which allows it to withstand significant loads without deformation. The key characteristic of steel is its ability to resist wear, making it a popular choice for applications where longevity is essential. A unique feature of steel is that it can be heat-treated to enhance its hardness and fatigue resistance. However, steel can be prone to corrosion if not properly protected, which is a significant consideration in environments where moisture is present.
Bronze
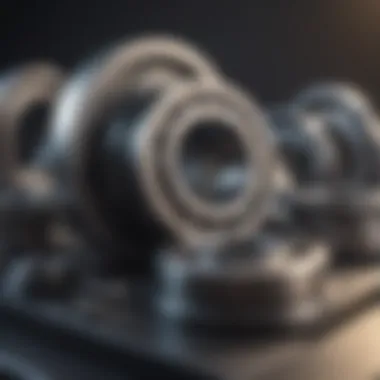
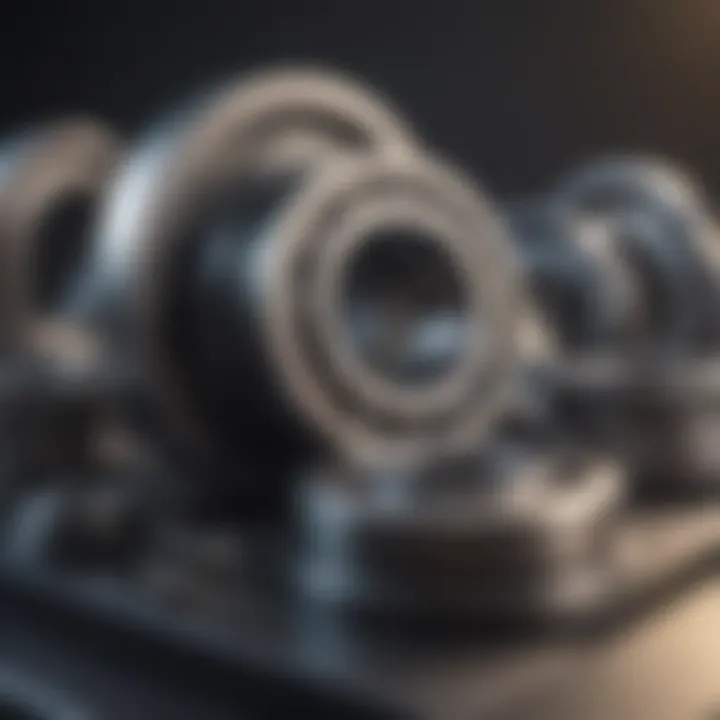
Bronze is another material used in conical bearings. It offers excellent corrosion resistance and has superior lubricating properties compared to steel. This makes bronze particularly favorable in marine and other humid applications. The key characteristic of bronze is its ability to operate effectively at higher temperatures without losing structural integrity. One disadvantage is that bronze tends to be less strong than steel, which could limit its use in certain high-load scenarios. However, its beneficial properties make it an ideal choice for specific applications where corrosion resistance is paramount.
Polymer Composites
Polymer composites are gaining popularity in the manufacturing of conical bearings due to their lightweight nature and excellent corrosion resistance. They can be tailored to meet specific performance criteria, including resistance to various chemicals and temperature fluctuations. A significant advantage of polymer composites is their ability to operate quietly, reducing noise in machinery. However, a unique disadvantage is their generally lower load-bearing capacity compared to metals. This can restrict their use in heavy-duty applications.
Material Selection Criteria
When selecting a material for conical bearings, several criteria should be considered:
- Load capacity: The material should withstand the operational loads.
- Environmental resistance: Consideration of factors like temperature changes and exposure to corrosive elements.
- Manufacturability: The ability to produce the material cost-effectively without compromising performance.
- Longevity: Predicting the life span of the material under expected operational conditions.
Choosing the right material for conical bearings is essential. It affects everything from performance to maintenance needs. Each material has its role, and the right choice is imperative for optimal functioning.
Applications of Conical Bearings
Conical bearings play a significant role in various fields of engineering and technology. Their design allows them to manage both axial and radial loads efficiently, making them essential for applications that require high precision and stability. These unique bearings are often chosen for their ability to handle thrust and load distribution effectively. This section will explore specific industries that utilize conical bearings and the benefits they derive from these components.
Automotive Industry
In the automotive sector, conical bearings are widely used due to their superior load-carrying capacity and durability. They are primarily found in wheel hubs and drive shafts where they manage the complex loads that arise during vehicle operation. A well-designed wheel bearing assembly can enhance vehicle stability, performance, and safety.
The integration of conical bearings in automotive applications brings several advantages:
- Enhanced Reliability: They are designed to operate for extended periods under challenging conditions, thus reducing maintenance needs.
- Precision Alignment: Conical bearings maintain precise alignment during operation, which is critical for vehicle performance.
- Noise and Vibration Reduction: Their design helps minimize vibrations, contributing to a smoother ride for passengers.
Aerospace Applications
In aerospace engineering, the demands for precision and reliability are particularly critical. Conical bearings are commonly employed in various aircraft components like landing gear and engine mounts. These bearings are subjected to extreme conditions and must maintain operational integrity under high stresses.
Several factors contribute to their significance in aerospace applications:
- Weight Efficiency: The lightweight nature of certain materials used in conical bearings can significantly reduce overall aircraft weight, improving fuel efficiency.
- Load Distribution: They efficiently distribute loads in multiple directions, which is crucial for maintaining the structural integrity of aerospace components during flight.
- Heat Resistance: Many conical bearings are designed to withstand high temperatures, which is essential in the harsh environment of engine components.
Industrial Machinery
Industrial machinery relies heavily on conical bearings for their performance and reliability. They are widely used in manufacturing equipment, conveyor systems, and heavy machinery where consistent load handling is paramount. The advantages of utilizing conical bearings in industrial settings include:
- Increased Lifespan: Quality conical bearings can last longer than traditional bearings in heavy-duty applications, reducing downtime and maintenance costs.
- Versatile Applications: They can be adapted to various machinery types, making them a flexible solution for different industrial needs.
- Optimized Performance: By enabling smoother operations, conical bearings help improve the efficiency of industrial processes, ultimately leading to higher productivity.
Conical bearings are integral to the performance and safety of machinery across multiple industries. Their ability to handle loads effectively makes them a smart choice for engineers.
Advantages of Conical Bearings
Conical bearings, known for their unique design, offer several advantages that make them a preferred choice in various applications. Understanding these benefits is essential for engineers and technicians involved in selecting and utilizing bearings in machinery. The advantages can significantly influence performance, reliability, and overall efficiency in systems where they are implemented.
Enhanced Load-Carrying Capacity
One of the most compelling features of conical bearings is their enhanced load-carrying capacity. The conical design allows for efficient distribution of loads, particularly in applications where both radial and axial forces are present. This geometry enables the bearings to handle high loads with minimal deformation.
- Load Distribution: The tapered raceways facilitate a wider area for load application. Forces can be shared across multiple rolling elements, which reduces stress on any single point. This characteristic is critical in high-load applications, such as automotive wheel hubs or heavy machinery.
- Durability: The ability to carry larger loads contributes to the longevity of these bearings. With reduced wear and tear, maintenance intervals can be extended, leading to cost savings over time.
- Performance Reliability: Enhanced load capacity ensures stable performance under variable conditions. This consistency is particularly valuable in industries where equipment uptime is essential, such as aerospace and industrial machinery.
Improved Axial and Radial Stability
Another significant advantage of conical bearings is their improved axial and radial stability. Stability is crucial for maintaining alignment within mechanical assemblies, preventing premature failure due to misalignment or shifting loads.
- Axial Load Handling: Conical bearings are designed to support substantial axial loads, which makes them ideal for applications involving thrust or directional forces. The conical shape provides a better fit for these loads, allowing for smoother operation and reducing the risk of components jamming or seizing.
- Radial Stability: The contact angle inherent to conical bearings promotes superior radial stability. This means that as loads increase, the bearings maintain their position without excessive movement. It results in less vibration and noise, leading to more comfortable operation.
- Alignment Considerations: Proper alignment during installation can lead to increased bearing life and efficiency in operation. Conical bearings are often easier to align correctly compared to their cylindrical counterparts.
"The correct selection and installation of conical bearings ensure optimal performance and longevity in mechanical systems."
Finale
Installation and Maintenance of Conical Bearings
The correct installment and ongoing care of conical bearings are crucial for their performance and longevity. Proper installation ensures that the bearings perform efficiently, contributing to the overall function of the mechanical systems in which they are integrated. Neglecting the installation and maintenance processes can lead to premature failure, increased wear, and costly downtimes.
Installation Procedures
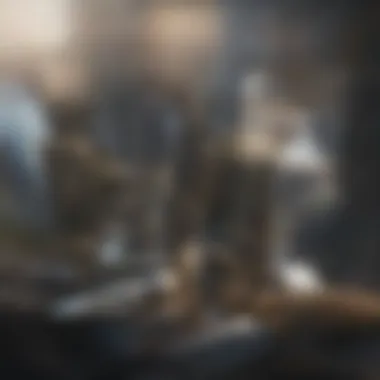
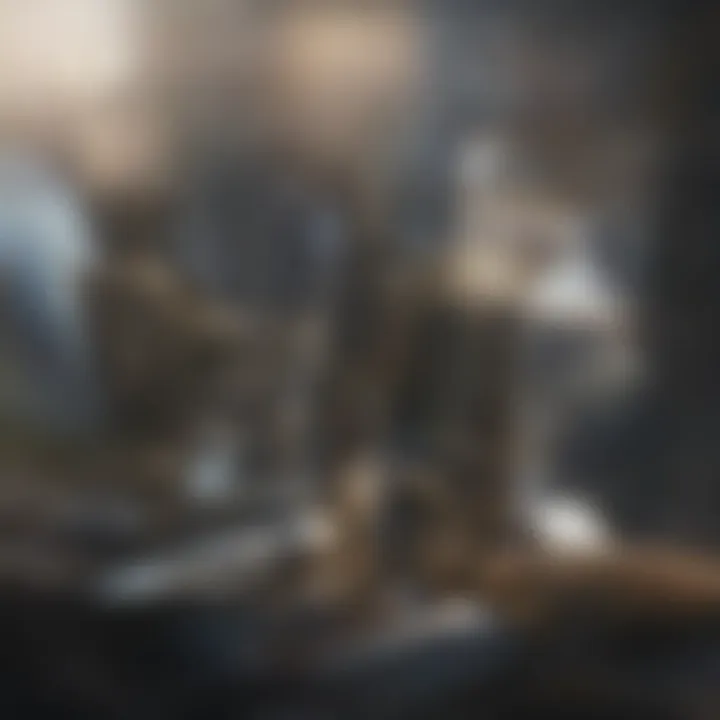
Installing conical bearings requires precision and attention to detail. The steps generally include:
- Preparation of Components: Ensure all components are clean and free of contaminants. Dirt or debris can lead to damage during installation.
- Checking the Fit: Verify that the bearing fits properly within the designated housing. This requires measuring both the inner and outer diameters, ensuring no discrepancies exist.
- Alignment of Bearings: Conical bearings must be aligned accurately. Misalignment can introduce excess stress and uneven wear. Use appropriate tools like dial indicators for precision.
- Pressing the Bearings: Bearings are often pressed into place using hydraulic press machines. Ensure that the force applied is uniform and does not exceed the specifications outlined by the manufacturer, as overpressing can result in damage.
- Lubrication: Correct lubrication is vital at this stage. Using the right type of lubricant helps reduce friction, providing smooth operation. Always follow the manufacturer's recommendations for lubricant type and quantity.
Maintenance Best Practices
Implementing effective maintenance practices ensures the reliable operation of conical bearings. Consider the following best practices:
- Regular Inspection: Frequent checks for wear, deformation, or anomalies in performance should be conducted. This proactive approach can identify issues before they escalate.
- Temperature Control: Monitor the operating temperature of the bearings. Excessive heat may indicate insufficient lubrication or misalignment.
- Lubrication Maintenance: Periodic reapplication of the lubricant is necessary. The intervals depend on operating conditions but should always adhere to the guidelines provided by the bearing manufacturer.
- Contamination Control: Keep the working environment clean. Contaminants can severely impair bearing function. Use seals and shields to protect against external particles.
Remember, proper care is essential for the longevity of conical bearings. Small maintenance tasks can prevent significant issues.
By understanding the installation and maintenance processes, users can greatly enhance the performance and reliability of conical bearings.
Challenges and Limitations
Understanding the challenges and limitations of conical bearings is crucial for various stakeholders in the mechanical engineering field. With their widespread applications, these bearings must perform reliably. However, specific factors can lead to their underperformance or failure. This section focuses on potential failure modes of conical bearings and the comparative limitations that users should consider.
Potential Failure Modes
Conical bearings can experience several potential failure modes due to improper usage, material fatigue, and contamination. Some of the most common failure modes include:
- Wear: Over time, the rolling elements can wear down, reducing the bearing’s efficiency. This wear can be accelerated by lubrication issues.
- Fatigue: Repeated stress cycles can lead to fatigue cracking of the races or rolling elements. Such cracks might not be visible immediately.
- Contamination: Dust, dirt, or other particles in the lubricant can result in abrasive wear. This damages both the races and rolling elements, decreasing the bearing life.
- Misalignment: Incorrect installation can cause misalignment, leading to uneven loading and premature failure of the bearing.
Preventing these failures requires regular maintenance and proper installation techniques to ensure the longevity and reliability of conical bearings.
Comparative Limitations
When compared to other types of bearings, conical bearings have certain limitations that users must recognize. These limitations can impact their suitability in different applications:
- Load Capacity: While conical bearings excel in certain load situations, they may not handle loads as effectively as spherical bearings in all scenarios. Users need to assess the specific load requirements of their applications.
- Complexity of Design: The design of conical bearings can be more intricate than that of simpler bearing types, which might necessitate more careful handling and installation practices.
- Maintenance Needs: Conical bearings generally require more frequent maintenance compared to sealed or self-lubricating bearings. This can lead to increased downtime for machinery.
- Cost Factors: The initial cost of high-quality conical bearings often exceeds that of other bearing types. While they provide enhanced performance, budget considerations may limit their use in less demanding applications.
In summary, while conical bearings offer distinct advantages, understanding their challenges and limitations is essential for optimizing performance in specific applications.
Future Trends in Conical Bearings Technology
The evolution of conical bearings is pivotal to various industries, reflecting ongoing innovations in both materials and designs. This section examines future trends in conical bearings technology, underscoring how advancements can enhance performance and extend their applicability across different sectors. Critical developments in this domain are not only geared towards improving the mechanical efficiency of these components but also focus on addressing the environmental concerns associated with their manufacture and use.
Advancements in Material Sciences
The progression of material sciences plays a significant role in the future of conical bearings. Researchers are exploring new materials that can provide higher strength, lower weight, and enhanced resistance to wear and corrosion. For example, advances in the development of ceramic and composite materials show promise in these aspects. These materials can reduce friction and increase the lifespan of bearings in demanding environments such as aerospace or heavy machinery.
Some noteworthy trends in material sciences that affect conical bearings include:
- Nanotechnology: The incorporation of nanomaterials can significantly enhance the mechanical properties and performance metrics of traditional bearing materials.
- Sustainable Materials: There is a growing emphasis on utilizing environmentally friendly materials that do not compromise performance. Examples include bio-based polymers that maintain structural integrity under varying loads.
- Smart Materials: These materials have the ability to adapt to changing conditions, providing real-time data on performance, wear, or potential failures through embedded sensors.
Advancements in material sciences enable manufacturers to meet the dual challenge of enhancing performance while adhering to sustainability practices.
Innovative Designs and Configurations
The design of conical bearings is also undergoing transformation due to technological advancements. Innovative approaches are being employed to increase their efficiency and performance across various applications. New configurations are being developed that optimize load distribution, which results in better stability and lower friction.
Key trends in design include:
- Modular Designs: These designs allow for easier customization and replacement of individual components without requiring the entire bearing assembly to be substituted. This ensures better adaptability to different machinery.
- Hybrid Configurations: Combining conventional materials with advanced composites is becoming more common, allowing for bearings that offer the best of both worlds. This approach improves load capacity while reducing overall weight.
- Advanced Geometries: Utilizing computer-aided design (CAD) and simulation tools leads to the creation of more complex shapes, which can better accommodate specific load requirements or application demands.
The future of conical bearings technology lies in the synergy of materials science and design innovation, promising increased efficiency and performance in the field.
Epilogue
The conclusion of this article serves as an essential synthesis of the various aspects related to conical bearings. It is vital to understand the cumulative insights gained throughout the discussion. Conical bearings play a critical role in multiple mechanical systems, which highlights their significance across industries such as automotive and aerospace. Their design factors, material properties, and load distribution characteristics have a direct impact on the performance of machinery.
Summary of Key Points
- Definition and Role: Conical bearings are pivotal in managing both radial and axial loads efficiently.
- Materials and Design: The selection of materials is underpinned by performance requirements, leading to innovations in both steel and polymer composites.
- Applications: From automotive vehicles to heavy industrial machinery, these bearings are ubiquitous in systems where stability and load management are crucial.
- Installation and Maintenance: Proper installation and maintenance protocols significantly enhance the lifespan and efficacy of conical bearings.
- Challenges and Future Trends: Awareness of potential limitations and trends in material science can guide future developments for performance enhancements.
The importance of concluding this article solidly lies in reaffirming the continuous need for improved designs and applications. Considerations such as advancements in technology, evolving materials, and the growing demand for more sophisticated machinery will guide researchers and engineers in optimizing conical bearings further.
The Future of Conical Bearings
Looking ahead, the conical bearing technology seems poised for innovations that promise improved functionality and efficiency. As industries continue to strive for higher performance, new materials may emerge that offer better wear resistance and lower friction coefficients. This could lead to bearings that not only perform better under heavy loads but also contribute to reducing energy consumption in various machinery.
Moreover, further research in nanotechnology and smart materials could yield bearings equipped with monitoring capabilities. This will provide real-time data on their operational conditions and health, thus allowing for proactive maintenance measures.