Understanding Piston Thermal Barrier Coating
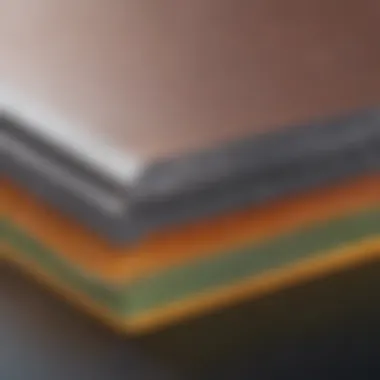
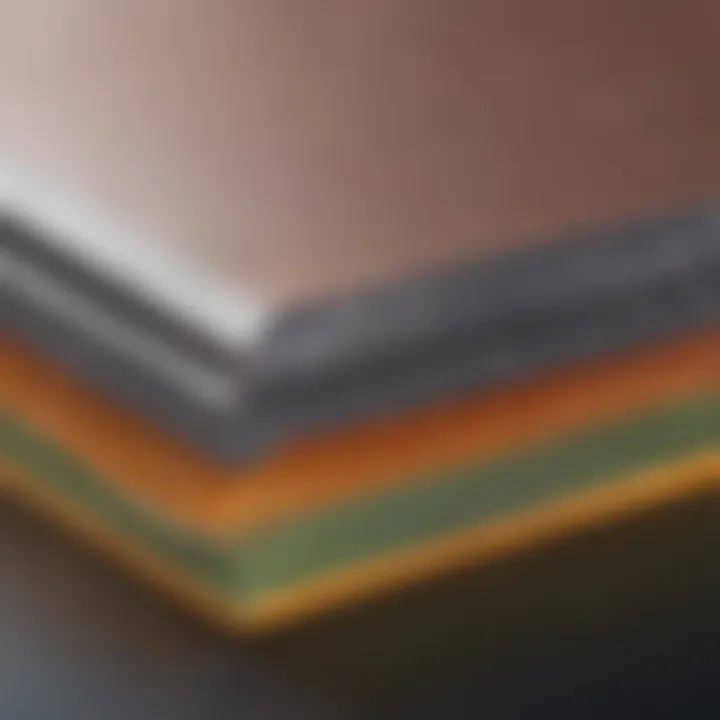
Background and Context
Overview of the research topic
Piston thermal barrier coatings play a crucial role in modern engine technology. These coatings are designed to improve engine efficiency and durability by controlling heat transfer within combustion chambers. In essence, a thermal barrier coating (TBC) acts as an insulator that minimizes heat loss to the piston structure while allowing for better combustion efficiency. Such advancements in technology are essential given the increasing demands for higher performance and lower emissions in automotive and aerospace industries.
Historical significance
The concept of enhancing engine performance through coatings is not recent. Historically, various materials have been experimented with to protect engine components from excessive thermal stress. The introduction of ceramic-based coatings marked a significant shift, which began in the late 20th century. These ceramic TBCs made it possible to enhance performance while addressing challenges related to durability and thermal management. Understanding the evolution of these coatings helps clarify their current use and potential future developments.
Key Findings and Discussion
Major results of the study
Research indicates that piston thermal barrier coatings can significantly reduce heat loss and improve thermal efficiency. Various studies have shown that the use of zirconia-based coatings leads to better overall performance metrics, including fuel efficiency and reductions in harmful emissions. The findings emphasize the importance of material selection and its effect on coating performance, longevity, and wear resistance.
Detailed analysis of findings
The application methods of these coatings differ, employing techniques such as plasma spraying, cold spraying, and chemical vapor deposition. Each method has its own set of advantages and challenges, depending on the substrate and desired properties. For example, plasma spraying is widely used due its ability to create dense and adherent coatings, whereas cold spraying offers lower thermal impact on substrates.
Furthermore, it is essential to consider the impact of the surrounding environment on the coating's performance. Studies indicate that factors like engine operating temperatures, types of fuels, and the presence of contaminants can greatly influence coating performance over time.
"To capitalize on the benefits of thermal barrier coatings, extensive testing must be conducted to ensure compatibility with various engine configurations and fuel types."
In the context of maintenance, coatings can also affect service intervals and the overall cost of engine upkeep. As coatings continue to innovate, they offer a pathway to not only enhanced performance but also sustainable practices in engine manufacturing.
In summary, the advancements in piston thermal barrier coatings reflect a significant development in engine technology. The integration of these coatings provides a dual advantage of improved efficiency and reduced environmental impact, which is aligned with contemporary engineering challenges.
Prologue to Piston Thermal Barrier Coatings
Piston thermal barrier coatings are critical to enhancing the performance of internal combustion engines. These coatings are strategically applied to piston surfaces to manage heat effectively. The control of thermal properties directly influences engine efficiency and longevity. As engines operate at high temperatures and pressures, it is vital to maintain optimal thermal conditions. The coating serves as an insulator, reducing heat transfer from the combustion chamber to the piston, which ultimately protects the piston material and improves its durability.
Understanding piston thermal barrier coatings involves a multi-faceted approach. There is a need to examine the materials used in their formulation, the methods of their application, and the impact on overall engine performance. Each aspect plays a crucial role in the efficacy of these coatings. The presence of these coatings can lead to a noticeable enhancement in engine efficiency, as they allow for higher compression ratios and more effective combustion cycles.
The significance of this topic is underscored by the growing demands for more efficient and environmentally friendly engines. With advancements in coating technology, the challenges associated with application, cost, and durability are being addressed. Recognizing these coatings' potential has broad implications not just for automotive manufacturers but also for environmental sustainability.
"Thermal management through coatings is not just about protection; it's about unlocking potential in engine technology."
Understanding the scope of piston thermal barrier coatings provides insights essential for students, researchers, and professionals. It offers clarity on how these coatings contribute to engine efficiency and the challenges in their application.
By diving deeper into the elements defining thermal barrier coatings, the historical context surrounding their development, and their practical application in today's engines, we create a comprehensive narrative on this vital topic.
Importance of Thermal Management in Engines
Thermal management in engines is crucial for optimal performance and longevity. Efficiency hinges on effectively controlling the heat generated during operation. Without proper management, excessive heat can lead to various mechanical failures, impacting the engine's overall functionality and effectiveness. This underscores the significance of thermal barrier coatings, which actively contribute to achieving desirable thermal conditions.
Good thermal management ensures that the engine operates within predefined temperature ranges. This oversight prevents overheating and promotes reliability. When the engine operates too hot, it can lead to excessive wear on components and increase the risk of failure. On the other hand, engine temperatures that are too low can hinder performance, leading to incomplete combustion and increased emissions.
The benefits of effective thermal management extend to several dimensions:
- Increased Durability: By maintaining optimal temperature levels, the wear and tear on engine components can be minimized. This prevents costly repairs and maximizes the lifespan of the engine.
- Enhanced Performance: Engines running at ideal temperatures perform better, providing more power and smoother operation.
- Environmental Impact: Proper thermal management can help lower emissions by ensuring efficient fuel combustion.
- Cost Efficiency: Reduced wear ultimately translates to lower maintenance costs over time.
Role of Temperature Control in Engine Performance
Temperature control is fundamental in defining engine performance. An engine that effectively regulates its internal temperatures not only runs more efficiently but also achieves higher power outputs. In this context, thermal barrier coatings offer an advanced solution to maintain optimal thermal conditions. They provide the insulation necessary to reduce heat transfer to surrounding components.
This capability enhances the combustion efficiency, as the hotter combustion chamber leads to more complete fuel burn and increased power output. Moreover, improved temperature control leads to reduced thermal stresses on engine components, contributing to long-term reliability and performance fidelity.
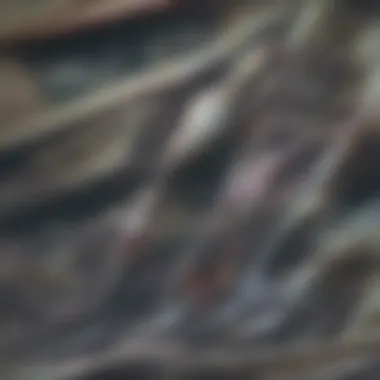
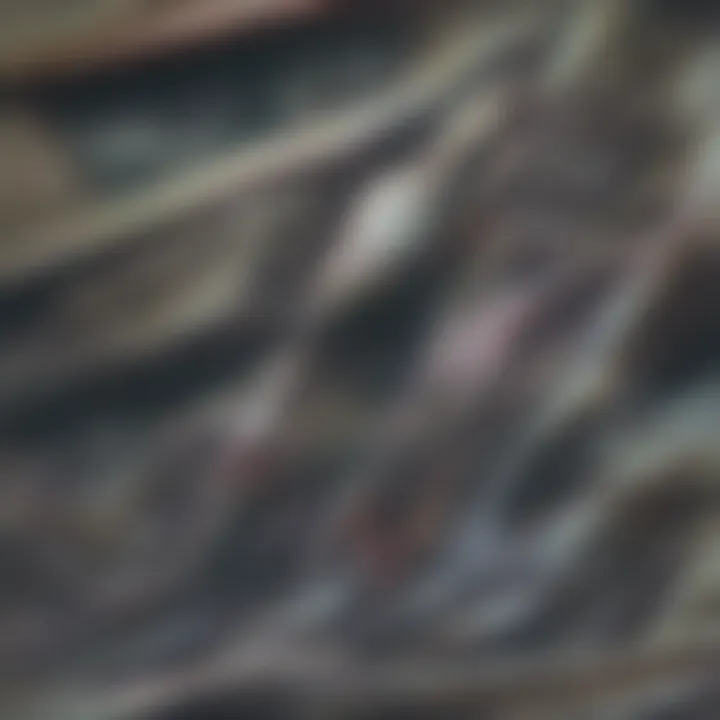
Impact on Fuel Efficiency
Fuel efficiency is directly tied to how heat is managed within the engine. An engine that loses excess heat without utilising it will burn more fuel than necessary. Thermal barrier coatings help reduce this thermal dissipation, ensuring more energy is utilized effectively. When the operating temperature remains high, fuel combustion becomes more efficient, leading to greater energy extraction from every drop of fuel.
In practical terms, this means lower fuel costs and a reduced environmental footprint. Improved fuel efficiency consequently contributes to enhanced engine performance and sustainability. Overall, managing temperatures through coatings has significant implications for both economy and ecology.
Materials Used for Piston Thermal Barrier Coatings
The selection of materials for piston thermal barrier coatings is crucial in enhancing engine performance. The choice of coatings determines not just the efficiency but also the longevity and reliability of engines. Understanding these materials helps in evaluating their operational benefits and the complexities in their deployment. Each type of coating offers distinct advantages and poses unique challenges. Thus, a thorough examination of ceramic, metallic, and composite coatings is essential in grasping their role in thermal management for performance optimizations.
Ceramic Coatings
Ceramic coatings are notable for their exceptional thermal resistance. They are primarily composed of zirconium dioxide, which has a high melting point. This property allows engines to operate at higher temperatures without suffering from thermal fatigue. The thermal barrier effect of ceramics reduces heat transfer deeper into the piston, protecting components from excessive thermal stress. Additionally, ceramic coatings can lower wear and tear, which significantly contributes to engine durability.
However, one must regard the adhesion of ceramic materials to the substrate. This challenge requires precise application techniques and surface preparation to ensure their long-term effectiveness.
Metallic Coatings
Metallic coatings, often comprising nickel or titanium alloys, provide a different set of benefits. They offer good thermal conductivity compared to ceramics, making them excellent choices for applications where heat removal and distribution are necessary. These coatings can enhance the strength of the piston, which is critical in high-performance environments such as racing or heavy machinery.
That being said, metallic coatings present their issues, primarily in high-temperature environments where they may oxidize or wear away faster than ceramics. Continuous development in alloy formulations is aimed at addressing these concerns, enhancing their overall utility in thermal barrier applications.
Composite Coatings
Composite coatings integrate materials from both ceramic and metallic categories. These coatings aim to blend the beneficial properties of both types while minimizing their weaknesses. For instance, a composite coating might provide a robust thermal barrier akin to ceramics while retaining better adhesion or stress distribution characteristics typical of metals.
The complexity of producing composite coatings can also be a challenge, as this involves sophisticated techniques and precise control over the manufacturing process. However, when done correctly, composite coatings can result in significant improvements to engine performance. This versatility makes them increasingly appealing to researchers and engineers alike looking for tailored solutions in thermal barrier technology.
The choice of coating material is not merely a question of preference, but a critical decision that impacts the performance and durability of engine components.
In summary, understanding the materials used for piston thermal barrier coatings lays the foundation for appreciating their impact on engine efficiency. Each of these materials contributes uniquely to how thermal management is achieved and the overall functionality of engines across various applications.
Application Techniques for Thermal Coatings
The significance of application techniques for thermal barrier coatings cannot be overstated in the context of piston technology. These techniques determine not only the effectiveness of the coatings in enhancing performance but also their long-term durability and adherence to engine components. Selecting the right technique can influence the properties of the coatings, such as their thickness, surface finish, and thermal resistance. It is essential to understand these techniques to appreciate their contribution to modern engine designs and methodologies.
Plasma Spray Coating
Plasma spray coating is one of the most widely used methods for applying thermal barrier coatings to pistons. This technique involves the creation of a high-temperature plasma arc, which melts the coating material and accelerates it toward the piston surface. The molten particles then adhere to the substrate, forming a cohesive layer.
This method offers several advantages:
- High Bond Strength: The intense heat allows for strong adhesion between the coating and substrate.
- Customizable Thickness: Operators can adjust the spray parameters to achieve desired thickness levels, which is crucial depending on the specific engine application.
- Wide Range of Materials: It can effectively use various ceramic and metallic materials, which broadens the scope of potential coatings.
However, plasma spraying does come with challenges. The process can create rough surface finishes if not controlled correctly, which may require additional machining. Furthermore, the heating and cooling cycles can introduce thermal stresses, potentially affecting both the coating and the piston material.
Physical Vapor Deposition
Physical vapor deposition (PVD) represents a more controlled approach to applying thermal barrier coatings. This method employs physical processes, such as evaporation or sputtering, to deposit thin films onto the surface of the piston. Unlike plasma spray, PVD typically operates at lower temperatures, minimizing the thermal stress on the substrate.
The benefits of PVD include:
- Uniform Coating: It often results in even coating thickness, ensuring enhanced performance.
- Good Adhesion: The bonding at the atomic level leads to improved adhesion properties.
- Low Material Waste: The process is efficient and produces less waste compared to other methods.
Yet, PVD has its limitations. It may not be suitable for very large components due to its scale limitations, and the cost of equipment can be prohibitive for some applications.
Cold Spray Technology
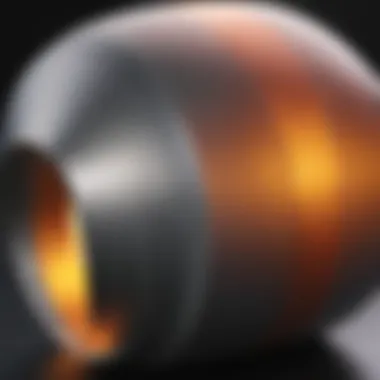
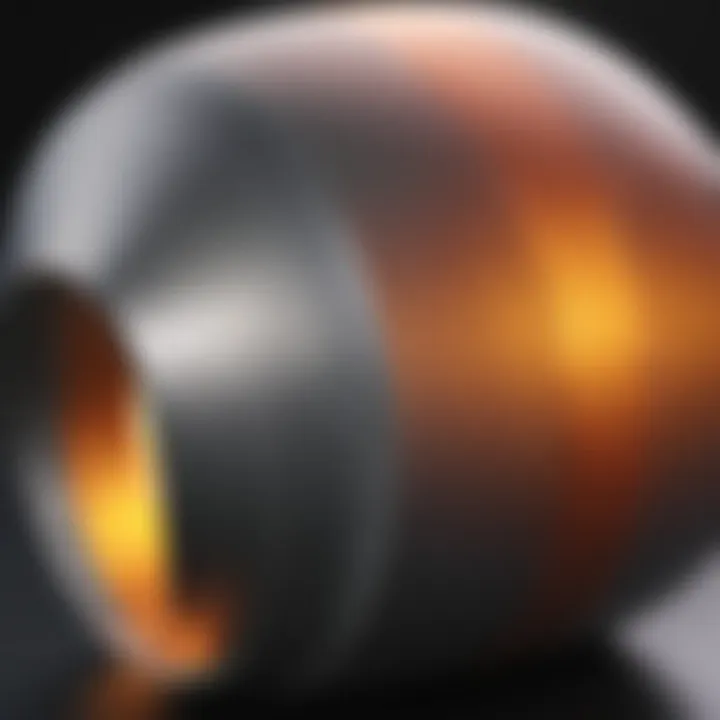
Cold spray technology is an innovative technique that has gained traction in recent years. It involves the acceleration of powdered materials at high speeds without melting them. Instead, the particles deform on impact and bond to the substrate through kinetic energy.
Key advantages of cold spray include:
- Low Thermal Impact: Since it does not involve melting, there is virtually no thermal damage to the substrate, preserving the integrity of the piston.
- Ability to Coating Complex Shapes: Cold spray can effectively coat intricate geometries, making it suitable for various piston designs.
- Minimal Oxidation and Reaction: The low temperatures reduce the risk of oxidation, ensuring that the coating’s properties remain intact.
On the downside, cold spray may have limitations in achieving very high coating densities, depending on the materials used and the parameters of the spray process.
Performance Benefits of Thermal Barrier Coatings
Thermal barrier coatings (TBCs) have become essential in modern engine design and optimization. They play a pivotal role in enhancing performance metrics like durability, efficiency, and heat management. Understanding these benefits is crucial for engineers and researchers focused on improving engine technologies.
Enhanced Engine Durability
One of the most significant advantages of thermal barrier coatings is the increase in engine durability. TBCs protect engine components from extreme temperatures and corrosive environments. By minimizing wear caused by thermal fatigue, these coatings extend the lifespan of critical parts, such as pistons and cylinder heads.
A durable engine reduces the frequency of repairs and downtime, ultimately leading to lower operational costs. This durability is achieved through the unique properties of the materials used in the coatings, which can withstand cyclic thermal loads more effectively than uncoated metals. Therefore, engineers must prioritize the selection of high-quality TBCs to realize maximum durability benefits in engine applications.
Reduction in Heat Transfer
Thermal barrier coatings significantly reduce unwanted heat transfer within internal combustion engines. This characteristic is vital for maintaining optimal engine temperatures and preventing overheating. The ceramic materials commonly used in TBCs possess low thermal conductivity, allowing them to act as effective insulators.
By diminishing heat transfer, TBCs also help in managing engine temperatures during operation. This aspect is particularly useful in high-performance engines, where excessive heat can compromise performance and reliability. Additionally, the reduction of heat transfer may result in less stress on cooling systems, improving overall engine efficiency.
"The application of TBCs in engines not only improves longevity but also aids in thermal management, leading to enhanced overall performance."
Improvement of Engine Efficiency
The implementation of thermal barrier coatings can lead to a marked improvement in engine efficiency. By limiting heat losses through the cylinder walls, TBCs enable engines to achieve higher thermal efficiency. This enhancement directly correlates to better fuel economy and reduced emissions.
Moreover, efficient thermal management allows engines to operate at higher compression ratios without the risk of knocking or pre-ignition. This capability can boost the performance characteristics of engines, making them more powerful and responsive without needing to escalate fuel consumption significantly. As fuel efficiency gains importance in automotive engineering, understanding the contribution of TBCs has become more relevant.
Challenges in Implementing Thermal Barrier Coatings
In the pursuit of enhancing engine performance and durability, piston thermal barrier coatings have emerged as a noteworthy technology. However, their implementation is not without challenges. Understanding these challenges is crucial for engineers and manufacturers looking to optimize the use of thermal barrier coatings. Several factors, including adhesion issues, thermal cycling effects, and financial considerations, play a significant role in the successful application and efficacy of these coatings.
Adhesion Issues
Adhesion is a primary concern in the application of thermal barrier coatings. The success of any coating largely depends on its ability to bond effectively with the substrate material. If adhesion fails, the coating may delaminate over time, leading to a decrease in performance and potentially causing engine failure. Factors influencing adhesion include surface preparation, coating application methods, and the inherent properties of the coating material itself. Proper surface treatment, for example, can significantly enhance the bonding strength.
It is essential for engineers to consider methods such as grit blasting or chemical etching to ensure a roughened surface, improving mechanical interlocking between the coating and the substrate. Moreover, the choice of coating material can further affect adhesion; while some materials may naturally bond better, they may lack other desirable properties.
Thermal Cycling and Fatigue
Thermal cycling refers to the repeated heating and cooling of materials, which can lead to fatigue over time. For piston thermal barrier coatings, this cycling can create stresses that may eventually result in cracks or fissures within the coating or at its interface with the substrate. These failures are particularly problematic as they can lead to increased thermal conductivity, negating the benefits of the thermal barrier.
Understanding the thermal expansion coefficients of the coating and the substrate is vital. Mismatched coefficients can exacerbate stress during temperature changes. Therefore, selecting materials with compatible thermal expansion rates can mitigate the adverse effects of thermal cycling.
Cost Considerations
Cost is a significant factor that impacts the adoption of thermal barrier coatings in the industry. Developing high-quality coatings often requires advanced materials and sophisticated application techniques, which may drive costs up. Manufacturers need to balance the initial investment against potential long-term benefits, such as enhanced engine performance and longevity.
Moreover, ongoing maintenance and the need for replacement or repair of thermal barrier coatings add to the financial considerations. It is important for decision-makers to conduct a thorough cost-benefit analysis, assessing both immediate and future expenses associated with these coatings.
For industries to maximize the benefits of thermal barrier coatings, it is essential to address these challenges comprehensively.
Future Trends in Piston Thermal Barrier Coatings
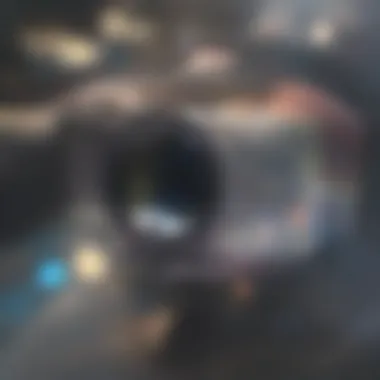
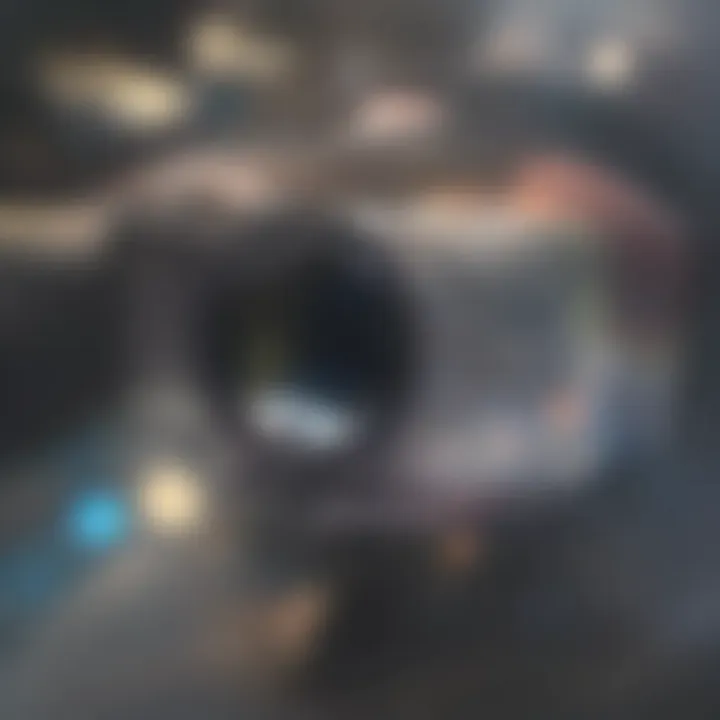
The exploration of future trends in piston thermal barrier coatings is crucial for understanding the trajectory of engine technology. Advances in materials science and engineering practices are paving the way for innovations that are likely to enhance the performance and sustainability of engines. Key trends include the development of novel materials and enhanced application techniques, alongside concerns related to environmental impact.
Emerging Materials and Technologies
The evolution of piston thermal barrier coatings often hinges on the availability of new materials and advanced technologies. Researchers are investigating alternative compositions beyond traditional ceramics and metals. For instance, innovative nanostructured coatings present unique advantages like improved thermal resistance and reduced thermal cycling damage. Using such materials enhances durability while maintaining optimal temperature control.
Furthermore, additive manufacturing is being applied to create complex geometries in thermal coatings, improving their bonding and effectiveness on engine surfaces. This technique allows for customization, which is essential for meeting specific engine design requirements.
Ultimately, the synthesis of these emerging materials could lead to a new era for thermal barrier coatings, offering superior performance at reduced weights and costs.
Environmental Considerations
As the world shifts towards more sustainable practices, the environmental impacts of piston thermal barrier coatings cannot be ignored. The production and disposal of these materials often raise ecological concerns. Future trends will likely focus on developing bio-based or recycled materials, minimizing the carbon footprint associated with fabrication and application.
Moreover, regulatory standards regarding emissions are becoming more stringent. Innovations in thermal barrier coatings can support compliance with these regulations by reducing fuel consumption and improving combustion efficiency. Coating technologies that promote cleaner emissions would become vital in automotive and aerospace sectors as environmental awareness grows.
Real-World Applications of Thermal Barrier Coatings
Thermal barrier coatings (TBCs) have gained significant traction across various industries due to their ability to improve performance and efficiency. This section examines their real-world applications in the aerospace sector, automotive engineering, and industrial machinery. Understanding these applications underscores the importance of thermal barrier coatings in enhancing operational capabilities and longevity of critical components.
Aerospace Sector
In the aerospace industry, thermal barrier coatings are vital for protecting components in extreme environments. Airplane engines, for example, operate under challenging conditions, with high temperatures and pressures. TBCs are used to insulate components such as turbine blades and combustors, providing thermal protection and preventing oxidation.
Benefits of TBCs in aerospace applications include:
- Increased Engine Efficiency: By reducing the heat transfer to the substrate, TBCs allow engines to operate at higher temperatures, resulting in better overall performance.
- Weight Reduction: The use of lightweight ceramic coatings helps to minimize weight, which is crucial in the aerospace sector.
- Longevity and Reliability: TBCs enhance the lifespan of critical components, reducing the necessity for replacements and maintenance.
Automotive Engineering
Automotive engineering heavily relies on thermal barrier coatings to improve engine efficiency and reliability. Thermal barrier coatings are commonly applied to pistons, cylinder heads, and exhaust valves. These coatings help manage temperature fluctuations, preventing overheating and extending the life of these components.
Key points regarding automotive applications include:
- Enhanced Performance: TBCs optimize combustion chamber temperatures, leading to improved fuel combustion and engine performance.
- Fuel Efficiency Gains: Engines with thermal barrier coatings typically demonstrate increased fuel efficiency, which is essential in today’s eco-conscious market.
- Reduced Emissions: By promoting more complete combustion, TBCs contribute to lower emissions, aligning with regulatory standards.
Industrial Machinery
In the realm of industrial machinery, thermal barrier coatings are applied to a variety of high-temperature components, such as turbines, exhaust systems, and heat exchangers. The need for effective thermal management in these applications cannot be overstated, as prolonged exposure to heat can lead to material degradation.
Advantages of using TBCs in industrial machinery include:
- Protection Against Wear: TBCs shield components from thermal stress and oxidation, enhancing durability.
- Operational Efficiency: By maintaining optimal temperature ranges, TBCs allow machinery to function more efficiently, reducing operational costs.
- Maintenance Reduction: With added protection, the frequency of maintenance can be decreased, saving time and resources.
"Thermal barrier coatings not only protect critical components but also enhance their performance and lifespan in extreme conditions."
In summary, thermal barrier coatings play a crucial role across various sectors by providing thermal protection, improving efficiency, and extending the life of essential components. Their real-world applications underscore their significance in advancing technology and operational productivity.
Closure
The conclusion of this article serves a critical role in synthesizing the complex discussions surrounding piston thermal barrier coatings. This section emphasizes the key elements discussed throughout, detailing the significance, benefits, and future considerations of this technology in the context of engineering and materials science.
Summary of Key Insights
Piston thermal barrier coatings have emerged as essential components in enhancing engine efficiency and performance. Throughout this article, various aspects have been addressed, including:
- Definition and Significance: Understanding what thermal barrier coatings are and their purpose in controlling engine temperatures.
- Materials and Application Techniques: A look at the various types of materials used, such as ceramic, metallic, and composite coatings. The article also highlighted application techniques, such as plasma spray and cold spray technologies.
- Performance Benefits: The advantages of using thermal barrier coatings, including enhanced engine durability, reduced heat transfer, and improved fuel efficiency.
- Challenges and Future Trends: Challenges such as adhesion issues and thermal fatigue are significant. The exploration of future materials and technologies also presents a promising frontier in this sector.
These insights underscore that the employment of piston thermal barrier coatings can lead to tangible improvements in engine reliability and operation, optimizing performance under various conditions. Emphasis on precise engineering and material selection remains a fundamental takeaway for practitioners in this field.
Future Research Directions
The evolution of piston thermal barrier coatings continues to be an area ripe for exploration. Future research directions may include:
- Advanced Material Compositions: Investigating newer materials that could further enhance the properties of coatings, such as multi-layered structures or nanocomposite materials.
- Sustainability Concerns: As environmental pressures mount, research into sustainable coating processes and materials will likely gain traction. This includes the development of eco-friendlier manufacturing techniques and reusable materials.
- Long-term Performance Studies: Continued testing is essential to understand the long-term durability and performance metrics of these coatings under varying operational stresses and environmental conditions.