Measuring Wall Thickness: Techniques and Considerations

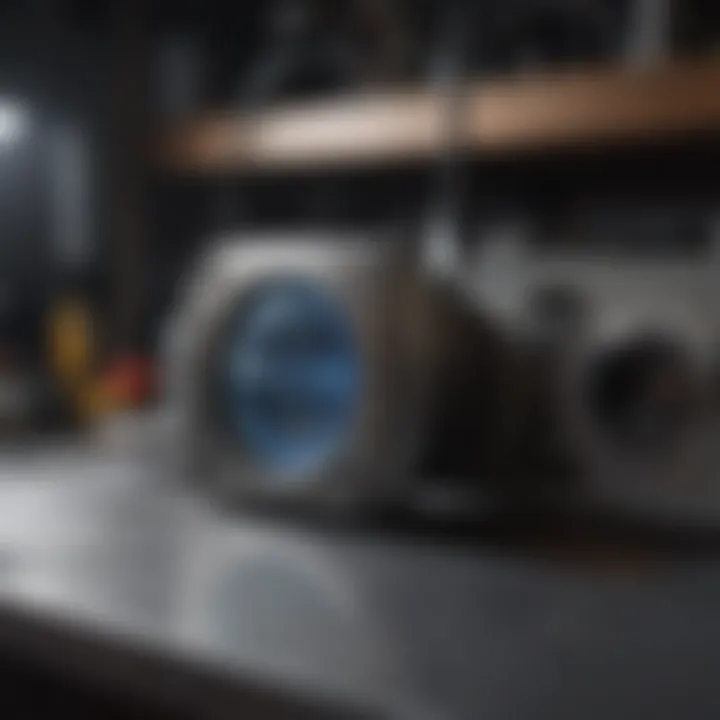
Intro
In the realm of engineering and manufacturing, measuring wall thickness is a fundamental aspect that is often overlooked. The importance of precise measurements cannot be understated, especially when materials are used in critical applications. Incorrect wall thickness measurements can lead to structural failures, inefficiencies in production, and safety hazards. Hence, understanding the methodologies available for measuring wall thickness is crucial for professionals in various fields.
This article aims to provide an in-depth exploration of several techniques utilized for measuring wall thickness across diverse materials. We will discuss how each method functions and examine the factors influencing measurement accuracy. Additionally, we will delve into the considerations one must take when selecting appropriate techniques based on specific material properties. Professionals, researchers, and students will find this article valuable as it synthesizes important insights related to material assessment.
Preamble to Wall Thickness Measurement
Wall thickness measurement is a crucial aspect in various fields such as engineering, manufacturing, and construction. Understanding wall thickness is essential for ensuring the durability and safety of structures and components. This section provides an overview of the significance of measuring wall thickness accurately and highlights some specific elements that professionals should consider.
Definition and Importance
Wall thickness refers to the distance between the two outer surfaces of a material. Accurate measurement of this parameter is vital for several reasons:
- Structural Integrity: Thin walls might compromise the strength of a structure or vessel, leading to potential failures under stress. Conversely, excessively thick walls can increase material costs without additional benefit.
- Safety Compliance: Many industries are governed by strict regulations regarding wall thickness in construction and manufacturing to ensure safety and reliability.
- Cost Efficiency: Accurately assessing the wall thickness can lead to optimized use of materials, reducing unnecessary expenditures while maintaining strength requirements.
Applications Across Industries
Measuring wall thickness finds application in various sectors, including:
- Construction: Wall thickness is critical in reinforcing walls and ensuring the structural support of buildings.
- Manufacturing: In the production of pipes, tanks, and pressure vessels, the precise measurement of wall thickness is crucial for determining the longevity and functionality of products.
- Aerospace: Components in aircraft must adhere to stringent wall thickness specifications to withstand aerodynamic forces.
- Automotive: In vehicle manufacturing, wall thickness can influence weight, performance, and safety features such as crashworthiness.
"Accurate wall thickness measurement is essential across multiple industries, as it directly impacts performance, safety, and reliability."
Overall, the measurement of wall thickness underlines the intersection of engineering principles and practical applications, reminding professionals of the importance of diligence and precision in their work.
Factors Influencing Wall Thickness Measurements
Understanding the factors influencing wall thickness measurements is essential for achieving precision in various applications. The accuracy of wall thickness measurements can significantly impact the integrity of structures and the quality of manufactured products. Factors such as material type, environmental conditions, and surface preparation play critical roles in determining measurement outcomes. An awareness of these elements is paramount for professionals engaged in manufacturing, construction, and engineering. This section aims to dissect these factors to offer a comprehensive understanding of their implications in wall thickness measurement.
Material Type Considerations
Different materials exhibit unique properties that can significantly affect how wall thickness is measured. For instance, metals, plastics, and composites respond differently to various measurement techniques. All materials possess distinct acoustic properties, thermal conductivity, and surface characteristics.
- Density and Composition: Denser materials often yield more accurate readings with ultrasonic testing due to better sound wave conduction. Conversely, some plastics may absorb sound waves, leading to erroneous thickness assessments.
- Elasticity and Flexibility: Materials with high elasticity may compress during the measurement process, influencing the recorded thickness. It is essential to select a measurement technique that aligns with the materialโs behavior under stress.
- Manufacturing Variability: Variations in manufacturing processes can introduce inconsistencies in wall thickness. Understanding the material's origin and processing history can provide insights into its wall consistency.
Temperature Effects
Temperature is another crucial factor affecting wall thickness measurements. Temperature fluctuations can alter the physical dimensions of materials, leading to measurement inaccuracies.
- Thermal Expansion: Most materials expand when heated and contract when cooled. This behavior can cause changes in wall thickness readings under varying temperatures. Measurements taken at ambient temperature conditions are typically more reliable.
- Instrument Calibration: Measuring instruments may require temperature compensation to ensure accurate results. For instance, ultrasonic devices must be calibrated to account for temperature-induced variations in sound speed.
- Material Brittleness: At lower temperatures, some materials, particularly certain polymers, become more brittle, which may affect how wall thickness can be reliably measured. Being cautious in extremely low or high temperatures is beneficial.
Surface Condition and Preparation
A material's surface condition is crucial when it comes to accurately measuring wall thickness. Unprepared surfaces may lead to inaccurate readings and skewed results.
- Surface Roughness: Rough surfaces can hinder the contact needed for precise measurements, especially with tools like micrometers or calipers. Smoothing the surface beforehand can yield significantly improved accuracy.
- Contaminants and Coatings: Oils, dust, and other contaminants can affect measurement tools and results. Ensuring that the surface is clean is vital for obtaining accurate readings. Similarly, coatings or external layers may add to the apparent thickness if not considered during assessment.
- Calibration and Setup: Properly calibrating measuring devices and using the right setup is important. The angle of measurement and contact pressure can influence results, potentially adding to errors if not properly managed.
"A comprehensive understanding of these influencing factors is not just beneficial; it is essential for ensuring the precision and reliability of wall thickness measurements."
Techniques for Measuring Wall Thickness
Measuring wall thickness is crucial in various fields like construction, manufacturing, and engineering. The selected technique can greatly influence accuracy and reliability. Knowing specific methods assists in making informed choices based on application and requirements. Choosing the right measurement approach impacts material performance, lifespan and safety. Here we will explore the main techniques, their characteristics and the benefits they offer.
Ultrasonic Testing
Principle of Operation
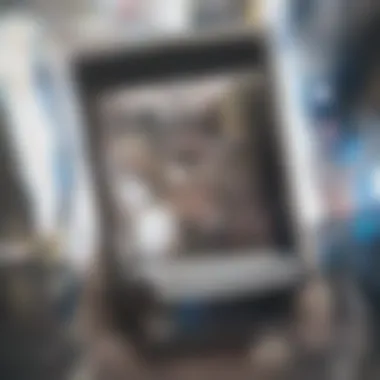
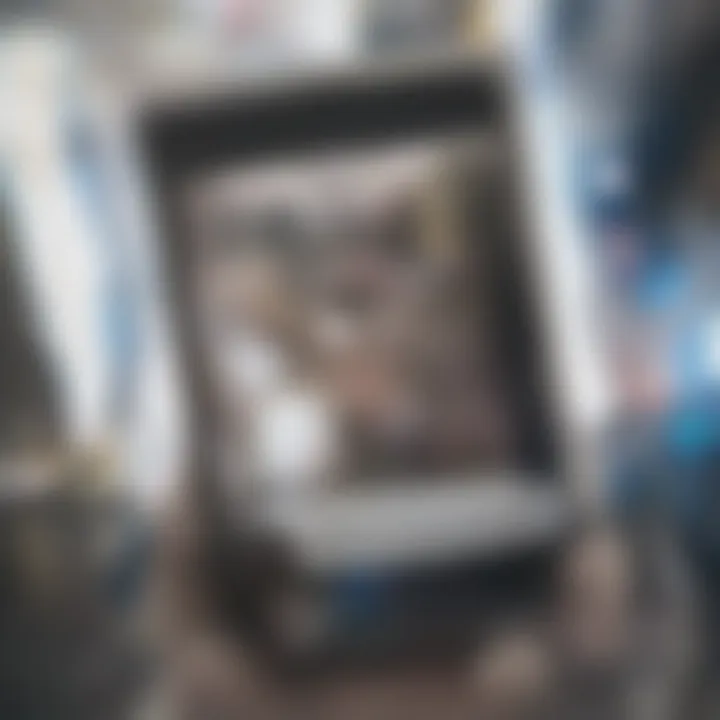
Ultrasonic testing involves using high-frequency sound waves to measure the thickness of materials. A transducer sends ultrasonic pulses into the material, and the time taken for these waves to bounce back is utilized for calculations. This non-invasive approach provides a reliable means to determine wall thickness without causing damage. One key characteristic of ultrasonic testing is its ability to gauge thickness despite surface irregularities, making it suitable for various applications.
Advantages and Disadvantages
Ultrasonic testing offers several advantages. It is precise and can be used on a wide range of materials, including metals, plastics, and composites. Additionally, it allows for measurements from one side of the material, enhancing convenience. On the downside, it may require skilled technicians for accurate interpretation of results. It can also be affected by material properties such as density and structure, which may lead to misinterpretation in certain cases.
Common Applications
Common applications of ultrasonic testing include pipeline inspections, tank wall evaluations, and evaluating weld integrity. This method is widely used in industries such as aerospace and manufacturing because of its reliability. Its non-destructive nature allows for ongoing assessments without compromising material integrity. The key feature is its versatility, with the capability to adapt to various thickness ranges and material types.
Micrometer Measurement
How to Use a Micrometer
Using a micrometer is straightforward but requires precision. A micrometer typically consists of a fixed jaw and a movable jaw. To measure thickness, the object is placed between these jaws, and the movable jaw is turned until it gently contacts the material. The measurement is read off the scale, allowing for high accuracy. The ability to gauge small dimensions accurately makes micrometers a popular choice in many settings.
Types of Micrometers
There are several types of micrometers, including outside micrometers, inside micrometers, and depth micrometers. Each type serves a distinct purpose. Outside micrometers gauge the thickness of an object, inside micrometers measure internal diameters, while depth micrometers assess bore depths. This variety allows for specialized measurements in precise applications, enhancing flexibility.
Accuracy Considerations
When using micrometers, accuracy is crucial. Regular calibration and proper handling are essential to maintain the instrument's precision. A micrometer can usually measure with an accuracy of ยฑ0.01 mm or better, making it suitable for high-precision tasks. However, environmental factors, such as temperature and humidity, can influence measurements, requiring careful consideration of conditions during use.
Laser Scanning Techniques
Working Principles
Laser scanning techniques use laser beams to capture surface profiles and measure wall thickness. The laser emits a beam, which reflects off the surface. The instrument calculates the thickness based on the time it takes for the light to return, providing accurate results. A key characteristic is its ability to gather data quickly over large areas, making it efficient for extensive applications.
Applications in Industry
Laser scanning techniques find applications in architecture, construction and manufacturing. They help create detailed 3D models for structural analysis. This technique caters to industries where dimensional accuracy is vital, such as automotive and aerospace sectors. The advantage is the rapid collection of comprehensive data without extensive manual measurement processes.
Comparison with Other Methods
Comparing laser scanning with traditional methods like ultrasonic testing or micrometer measurements, laser scanning excels in speed and data density. While ultrasonic testing is effective in gauging thickness, laser scanning offers a full surface profile, enhancing overall analysis. However, laser scanning systems can be expensive and may require specific training for effective operation.
Eddy Current Testing
Working Mechanism
Eddy current testing relies on electromagnetic principles, using alternating currents to induce magnetic fields. When a probe is placed near a conductive material, it generates eddy currents which are affected by material thickness. This technique is beneficial for non-destructive evaluation, offering quick results. The unique feature is its capability to measure thickness in conductive materials, giving it an edge in certain applications.
Applications
Eddy current testing is commonly used in applications like detecting corrosion in pipelines and assessing coatings. This method is widely adopted in industries such as aerospace, automotive and manufacturing. Its speed and accuracy make it a preferred method for real-time assessments and quality control.
Limitations
However, eddy current testing has limitations. It is primarily effective on conductive materials, which restricts its usage. Furthermore, surface conductivity and coatings can influence measurements, sometimes leading to inaccurate results. It is essential to evaluate these factors before selection to avoid potential inaccuracies.
Choosing the Right Measurement Technique
Selecting an appropriate measurement technique for wall thickness is critical in achieving accurate results. Each material presents unique properties and challenges, making it essential to tailor the measurement method accordingly. Many factors come into play, including the material type, cost constraints, and the required level of accuracy. Understanding these elements enables professionals to make informed decisions that can have lasting implications on project quality, safety, and efficiency.
Evaluating Material Properties
Material properties significantly influence the choice of measurement technique. Different materials respond distinctively to various measurement methods. For instance, softer materials like plastics may warp under pressure from tools like micrometers, leading to inaccurate readings. In contrast, metals generally withstand such pressure well but may exhibit variability due to factors like grain structure or heat treatment.
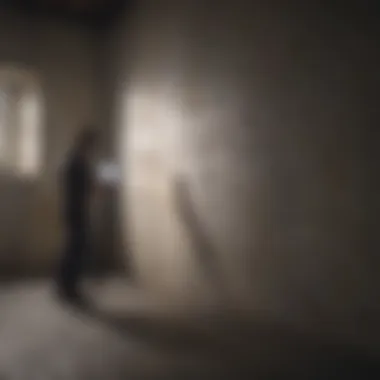
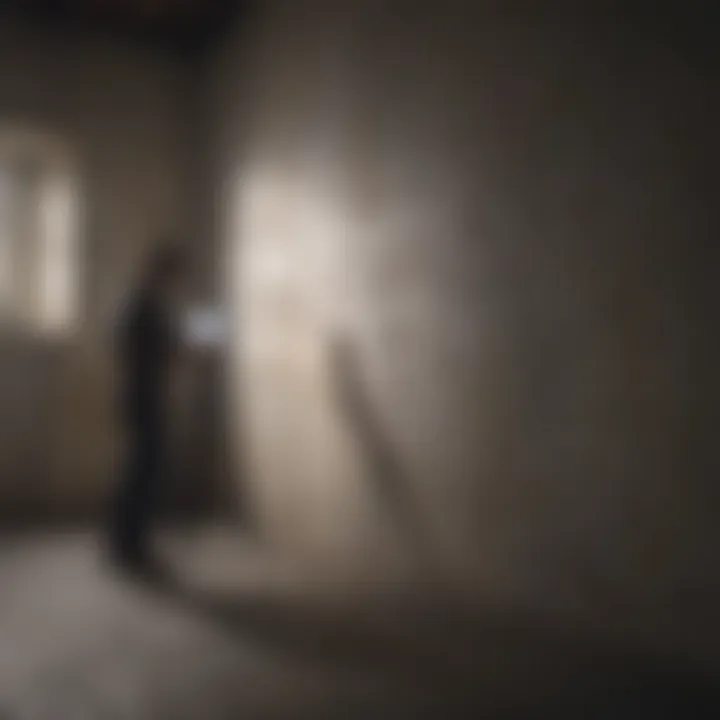
It's crucial to assess each material's physical characteristics before proceeding. Key considerations include:
- Density and Hardness: These factors will determine the required force applied during measurement.
- Thickness Range: Some techniques might not be effective for very thin or very thick materials.
- Surface Finish: A rough surface might interfere with the measurement, impacting precision.
Understanding how these attributes interact with measurement techniques allows for better decision-making in the selection process.
Cost Considerations
Cost is a vital factor in the decision-making process for wall thickness measurements. Various methods come with different price points ranging from affordable handheld tools to advanced, expensive scanning equipment. Budget constraints often dictate what is feasible for a project, but it is essential to weigh the costs against the implications of measurement inaccuracies.
For instance, investing in high-quality ultrasonic testing equipment may seem cost-prohibitive initially. However, the precision and reliability it provides can lead to significant savings in terms of reducing the risk of structural failures and subsequent reparations.
Professionals should assess:
- Initial Costs: The purchase price or rental fees of equipment.
- Operating Costs: Maintenance and operational training needed for sophisticated systems versus simpler tools.
- Potential Future Costs: Considerations related to rework, warranty claims, or material wastage due to measurement errors.
Evaluating these cost dimensions ensures the chosen technique aligns with budgetary and operational goals.
Accuracy Requirements
The accuracy of wall thickness measurements is non-negotiable in many industries. Precision influences not only the safety and functionality of structures but also compliance with regulatory standards. As such, identifying the required accuracy level is fundamental in technique selection.
Different techniques offer varying degrees of accuracy:
- Ultrasonic Testing: Known for high accuracy and suitability for a wide range of thicknesses.
- Micrometer Measurement: Offers exceptional precision for small measurements but requires careful handling and surface preparation.
- Laser Scanning Techniques: Delivers advanced accuracy but can be impacted by surface reflectivity.
Professionals must align the accuracy requirements with methods that can meet or exceed these expectations. This alignment helps minimize risks associated with measurement mistakes, safeguarding both projects and resources.
"Choosing the right measurement technique is not just about the method; it is about ensuring the safety and reliability of the outcomes."
Selecting the right wall thickness measurement technique requires a balance of understanding material properties, assessing costs, and prioritizing accuracy. Awareness of these elements is an essential step toward achieving reliable and satisfactory results.
Technical Standards and Compliance
The significance of technical standards and compliance in wall thickness measurement cannot be understated. These standards establish a framework for ensuring accuracy, consistency, and safety across various applications. In industries where wall thickness can dramatically affect the structural integrity of components, adhering to established guidelines becomes essential.
International and industry-specific standards serve multiple purposes. First, they provide benchmarks for accuracy. Adhering to these benchmarks helps professionals minimize measurement errors, which can lead to critical failures in construction or manufacturing. Second, compliance with these standards can enhance product reliability and improve market competitiveness. For organizations, demonstrating adherence to such standards is often a prerequisite for quality certification and can open doors to international markets.
When evaluating technical standards, consider the following aspects:
- Specification Requirements: Each standard outlines exact requirements for measurement tools and processes. Knowing these requirements ensures the right techniques and instruments are employed.
- Calibration Protocols: Technical standards often dictate how instruments should be calibrated to maintain precision. A well-calibrated instrument improves measurement reliability.
- Documentation and Traceability: Keeping detailed records of measurements and compliance can be vital. This practice allows for transparency and accountability, especially in regulated industries.
"Without robust standards, industries risk variability that can compromise safety and quality."
In summary, the role of technical standards and compliance is pivotal for establishing a culture of precision in wall thickness measurement. Each component of these standards helps professionals enhance the quality and safety of their products.
International Measurement Standards
International measurement standards are critical for standardizing wall thickness measurement techniques across various regions and sectors. Bodies such as the International Organization for Standardization (ISO) set these standards to ensure consistency and reliability in measurements. For example, ISO 8501-1 outlines cleanliness levels for surface preparation, which can indirectly affect wall thickness measurement by influencing the surface condition.
Some key international standards include:
- ISO 14687: This standard addresses measurement of pressurized gas, including considerations for wall thickness.
- ISO 17296: Provides guidelines on robotic measurements relevant to various materials.
- ASTM D4925: Focuses on non-destructive methods for thickness measurement of plastic films.
Following these standards can lead to increased accuracy and comparability of results, facilitating better communication in global markets.
Industry-Specific Guidelines
Industry-specific guidelines further refine the general principles outlined in international standards. Various sectors have unique requirements based on the materials involved and the applications at hand. For instance, the automotive industry may follow the Society of Automotive Engineers (SAE) guidelines, which dictate specific testing methods for evaluating wall thickness. Similarly, the oil and gas sector has standards from the American Petroleum Institute (API) to ensure safety and effectiveness in pipeline inspections.
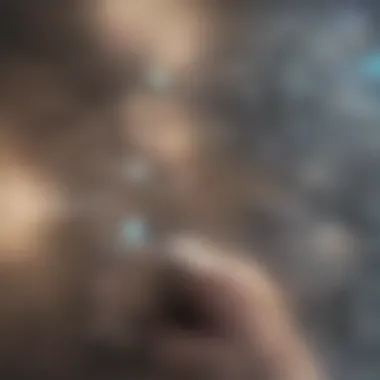
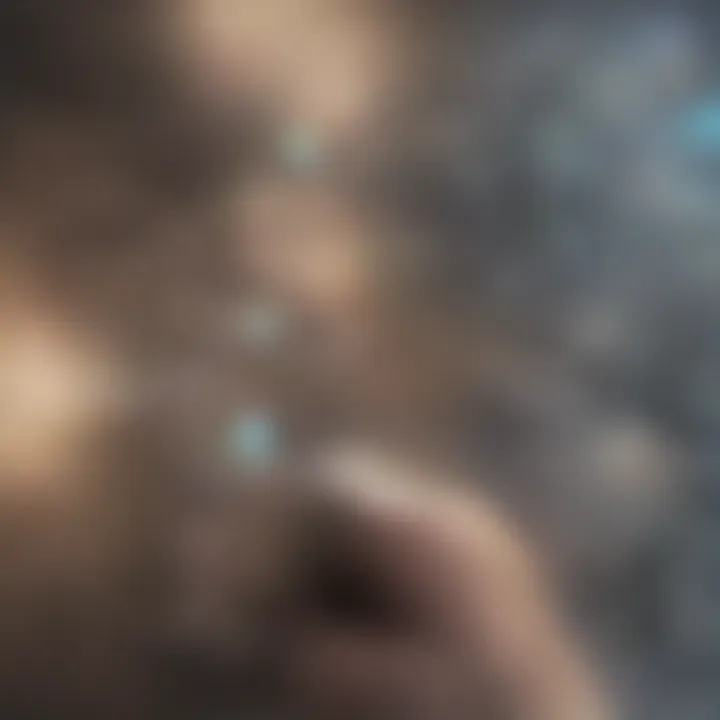
Key industry-specific guidelines include:
- API 5L: Provides specifications for line pipe used in oil and gas transportation, emphasizing wall thickness as a critical parameter.
- SAE J1231: Offers standards for ferritic castings, including thickness measurements essential for quality control.
- ISO 3834: Pertains to welding quality, where wall thickness measurement plays a role in assessing weld integrity.
By adopting and adhering to these guidelines, professionals can not only meet regulatory requirements but also improve operational efficiency and ensure high standards of safety. Therefore, understanding both international standards and industry-specific guidelines is essential for any stakeholder involved in the measurement of wall thickness.
Implications of Incorrect Measurements
Accurate wall thickness measurement is critical in various industries. Errors in measurement can have serious implications. Understanding these implications can aid professionals in making informed decisions about material assessments. Inaccurate measurements can lead to significant structural integrity risks and costly consequences in manufacturing processes.
Structural Integrity Risks
The first major implication of incorrect measurements involves the structural integrity of the materials being assessed. If wall thickness is measured inaccurately, it could lead to designs that do not meet the necessary safety standards. A thinner wall than expected, for example, may result in reduced strength and increase the likelihood of failure under stress. This is especially significant in construction and manufacturing where a component might support heavy loads or face environmental challenges.
In scenarios where pressure vessels or pipes are involved, the safety margins can be drastically affected. Failure to accurately measure wall thickness might lead to dangerous leaks or catastrophic failures. When professionals are responsible for ensuring safety, these risks are unacceptable. The costs of accidents due to inadequate structural integrity can reach far beyond monetary expenses, impacting human lives and environmental safety as well.
Costly Consequences in Manufacturing
The implications of incorrect wall thickness measurements extend into manufacturing operations as well. Miscalculations can cause a stream of inefficiencies, resulting in unnecessary production costs. For instance, if a part is improperly measured, it might need to be remade. This not only incurs additional material costs but also wastes labor time and resources.
Moreover, products that do not meet specifications might lead to production delays. Such setbacks can affect the overall supply chain and customer satisfaction. Therefore, accurate wall thickness measurements are not merely a good practice; they are essential for maintaining operational efficiency and product quality.
Future Trends in Wall Thickness Measurement
The landscape of wall thickness measurement is continually evolving, driven by technological advancements and the increasing emphasis on precision. Understanding future trends is essential to stay ahead in an industry where accuracy can mean the difference between safety and failure. As new methods emerge, professionals in engineering, manufacturing, and construction must adapt to these advancements. This section will explore significant elements and benefits associated with future trends in wall thickness measurement.
Advancements in Technology
Recent years have witnessed remarkable progress in measurement technology for wall thickness assessment. Innovative tools and instruments are being developed to enhance accuracy and efficiency. For instance, the introduction of portable ultrasonic devices allows for quick assessments without the need for extensive setup. These devices can operate with high precision, capturing wall thickness data with minimal user intervention.
Another significant advancement is the development of high-resolution laser scanning techniques. Laser scanners provide detailed three-dimensional data of surfaces, allowing for comprehensive analysis beyond mere thickness measurements. This method can also map irregular shapes and complex geometries effectively, making it suitable for modern manufacturing and construction tasks.
Moreover, digital innovations such as cloud-based data storage and processing enable easier access to measurement results. Collecting data remotely and analyzing it in real time can empower professionals to make informed decisions faster. This connectivity facilitates collaborative efforts among professionals across different locations, ensuring seamless project management.
Integration of Artificial Intelligence
Artificial Intelligence (AI) is increasingly finding its way into many fields, including wall thickness measurement. The integration of AI can significantly improve measurement accuracy and interpretation. Machine learning algorithms are capable of analyzing vast amounts of data from various measurement techniques, identifying patterns, and predicting outcomes.
One of the practical applications of AI is in predictive maintenance. By analyzing wall thickness data over time, AI systems can forecast when materials may become weak or compromised. This foresight can lead to timely interventions, preventing potential failures in structures which could be disastrous.
AI can also assist in automating the measurement process. Advanced robots equipped with AI can perform inspections with consistent accuracy, reducing human error. This automation can lead to increased productivity and allow human operators to focus on more complex tasks. In manufacturing environments, for example, AI-driven systems can ensure compliance with specifications by continuously monitoring wall thickness.
The future of wall thickness measurement lies not just in better instruments, but in leveraging technology like artificial intelligence to enhance understanding and accuracy of assessments.
Epilogue
In this article, the discussion on wall thickness measurement highlights its critical role in various industries. Understanding and correctly implementing wall thickness measurement techniques ensures both safety and functionality in construction, manufacturing, and engineering. A failure to measure accurately can lead to severe implications, including structural issues and increased costs.
Summary of Key Points
To summarize, several key aspects emerge from our exploration of wall thickness measurement:
- Techniques: Techniques such as ultrasonic testing, micrometer measurement, laser scanning, and eddy current testing are pivotal. Each has its advantages and drawbacks that cater to different material types and scenarios.
- Factors: Material type, temperature effects, and surface conditions all influence measurement outcomes. Professionals must be aware of these influencing factors to select the proper technique.
- Standards: Compliance with technical standards ensures that measurements meet international and industry-specific requirements, enhancing safety and reliability.
- Future Trends: Advancements in technology and artificial intelligence integration are set to change how wall thickness measurements are taken. These innovations will likely improve accuracy and reduce human error in measurements.
The Importance of Precision in Practice
Precision in wall thickness measurement cannot be overstated. It serves as the foundation for quality control across various sectors. In construction, an inaccurate reading can compromise the integrity of a structure. In manufacturing, the wrong wall thickness can lead to material waste and increased production costs.
To achieve a high level of precision, practitioners should be trained in the specific techniques they are using. For instance, knowing how to efficiently utilize a micrometer or an ultrasonic device is essential. Rigorous calibration procedures must also be established to ensure tools are functioning correctly.
By prioritizing precision, industries can uphold safety standards and optimize operational efficiency. In a competitive market, accuracy in measurements contributes not only to quality but also to overall profitability.
With increasing complexity in material science and engineering, the quest for precision remains a vital objective that should be embraced by all professionals in the field.
It is clear that as industries evolve, so too must the approaches to measuring wall thickness. Continuous improvements and education on cutting-edge techniques will lead to better outcomes and heightened standards of safety.