Understanding Large Ball Mills in Chemical Processing
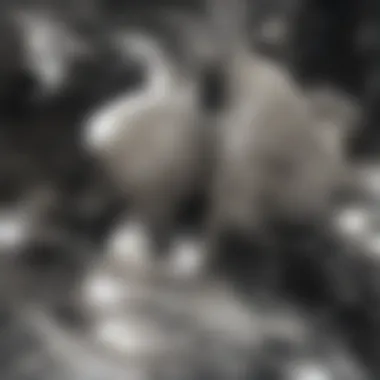
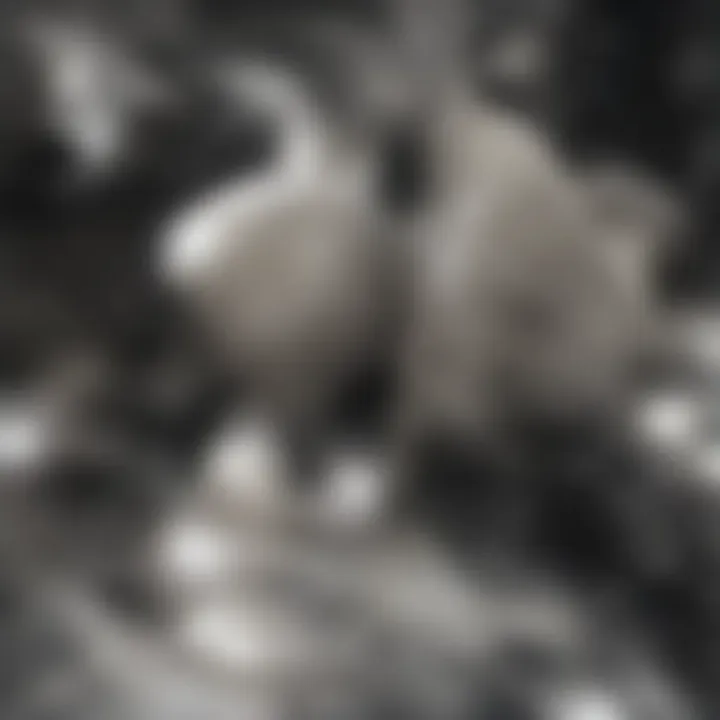
Intro
Large ball mills play a pivotal role in chemical processing. They are vital equipment used for grinding materials, influencing the efficiency of various processes in industries such as mining, metallurgy, and pharmaceuticals. Understanding how these massive machines operate can provide insights into their significance in the chemical sector.
Background and Context
Overview of the research topic
Large ball mills are cylindrical devices that rotate around a horizontal axis, filled with grinding media and materials. Their primary purpose is to reduce particle size through mechanical forces. This reduction process is critical in numerous applications, from ore processing to the creation of fine powders in chemical synthesis. As materials move through the mill, they experience tumbling and cascading actions, effectively breaking down larger particles during the process.
Historical significance
The development of ball mills dates back to the late 19th century. Initially, hand-operated models evolved into large-scale industrial equipment, leading to innovations in material processing. With time, their design has adapted to meet the evolving requirements of modern chemical processing, contributing to improved efficiency and operational safety.
Key Findings and Discussion
Major results of the study
Recent research emphasizes several critical aspects of large ball mills. Operational efficiency can often be enhanced by optimizing the mill's design and operational parameters. Factors such as the size of the grinding media, the rotational speed, and the filling ratio may significantly affect performance.
Detailed analysis of findings
For example, a study found that increasing the diameter of grinding balls could improve energy transfer and size reduction efficiency. Additionally, variations in speed can lead to changes in the impact forces acting on the materials, recalibrating the effectiveness of the milling process. Ongoing technological advancements have introduced automated systems and real-time monitoring, allowing for more precise control of milling conditions.
Prologue to Large Ball Mills
Large ball mills are crucial machines in the fields of chemical processing and material engineering. Their design and function significantly impact a variety of industrial applications, making the understanding of these machines vital for professionals in the sector. This section delves into the definition and purpose of large ball mills, followed by a historical overview that highlights their evolution and significance.
Definition and Purpose
Large ball mills are industrial equipment used for grinding and milling materials. They consist of a cylindrical shell filled with balls, usually made of steel or other hard materials, that rotate to crush and homogenize substances. The purpose of these mills is not just limited to grinding; they play a significant role in the mixing of materials, enhancing the physical properties of the final products. Essentially, their function embodies the transformation of raw materials into more usable forms or compounds.
Operationally, these mills exhibit a balance between energy efficiency and production capacity. They are widely employed in various sectors, including mining, metallurgy, and chemical manufacturing. Understanding their operational mechanics is crucial, as it provides insights into how to optimize their use for improved productivity and cost-effectiveness.
Historical Overview
The concept of ball milling dates back to the late 19th century, when manufacturers recognized the necessity for efficient methods to pulverize materials. Initially, small-scale operations utilized manual grinding, which was time-consuming and labor-intensive. The introduction of large ball mills marked a pivotal change in milling technology, enabling mass production which was previously unattainable. By the early 20th century, with advancements in engineering and material science, large ball mills became more widely utilized, particularly in the mining industry.
Significant milestones include the integration of automated controls in the 1960s, which enhanced operational efficiency. Over the decades, large ball mills have evolved to include features that allow for greater precision and control during the grinding process. This transformation continues today, as modern industries demand more efficient and environmentally friendly milling solutions.
Understanding the historical context of large ball mills helps frame their current applications and innovations. As industries evolve, so too do the technologies surrounding ball mills, ensuring their relevance in modern processing environments.
Mechanics of Large Ball Mills
The mechanics of large ball mills plays a crucial role in understanding their operations within chemical processing. This section delves into how these mills function, highlighting vital concepts that dictate their efficiency and effectiveness. Knowledge of the mechanical principles allows industries to optimize productivity, achieve desired material properties, and reduce operational costs. Thus, grasping these mechanics is essential for anyone involved in chemical engineering, material processing, and related fields.
Operational Principles
Large ball mills function primarily through the interaction of the grinding media, which are typically steel or ceramic balls, and the material to be processed. The principle is straightforward: these mills use gravitational and rotational forces to achieve size reduction through impact and attrition. As the mill rotates, the balls ascend along the mill's wall before descending to apply force on the material at the bottom. This motion creates sharp compressive forces that fracture the material.
Key elements of their operation include:
- Rotation Speed: The speed at which the mill rotates is critical. If the speed is too low, the balls fail to generate enough force; too high, and they won't impact the material effectively.
- Filling Ratio: The amount of grinding media in relation to the total volume of the mill will influence the grinding effectiveness. An optimal filling ratio is essential to ensure sufficient contact between media and materials.
Understanding these dynamics allows for better control over the milling process, leading to improved product quality and reduced waste.
Energy Consumption Dynamics
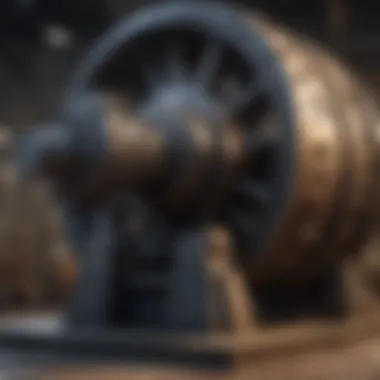
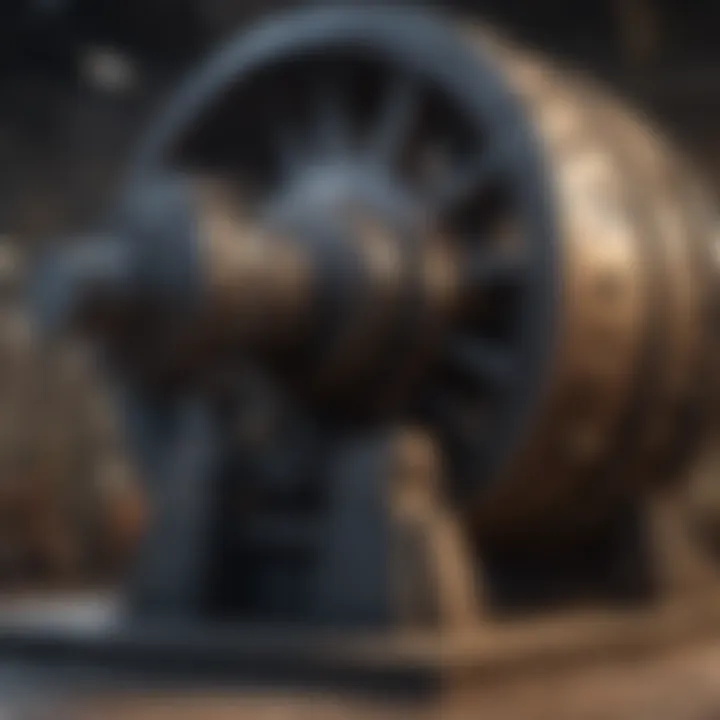
The energy consumed during the operation of large ball mills is a key factor influencing both their efficiency and overall costs. The amount of power required to run these mills is primarily determined by the quantity of material being processed and the intended product fineness.
Several aspects affect energy consumption:
- Material Characteristics: The hardness, moisture content, and feed size of the material being processed have direct implications on energy use. Harder materials require more energy to achieve the same degree of size reduction.
- Mill Design: The design features, such as the type of drive mechanism and liner design, can impact energy efficiency. For instance, mills with variable speed drives can optimize energy consumption during different phases of operation.
- Operational Parameters: Factors such as the operational load and isolation of the mill can significantly influence energy dynamics. By monitoring and adjusting these parameters, operators can minimize energy wastage.
"Understanding energy consumption dynamics in large ball mills is crucial for developing sustainable practices in chemical processing."
In summary, comprehending the mechanics behind large ball mills—their operational principles and energy consumption dynamics—provides invaluable insights into optimizing their use in chemical processing. This knowledge enables professionals to better manage their resources while ensuring high levels of efficiency and productivity.
Design Features of Large Ball Mills
The design features of large ball mills play a crucial role in their overall efficiency and effectiveness in chemical processing. Understanding these features helps to optimize the operation, enhance performance, and extend the lifespan of these machines. When considering large ball mills, factors such as the materials used in construction, dimensional specifications, and proper load configurations come into focus. Each of these elements significantly contributes to how well these mills function in various industrial applications.
Construction Materials
The choice of materials in the construction of large ball mills is pivotal. Typically, mills are made from materials such as steel, iron, and various alloys. These materials are selected based on their durability, resistance to wear, and ability to withstand high temperatures and corrosive environments.
- Steel: This material is favored for its strength and ability to endure the immense pressures and impacts during milling processes.
- Cast Iron: Often used for certain parts of the mill, cast iron provides good wear resistance and is cost-efficient in manufacturing.
- Alloyed Materials: High chromium or nickel alloys are used for specific components to increase hardness and resistance against abrasive materials.
The combination of these materials enhances the structural integrity of the mills and minimizes wear and tear over time. Additionally, selecting proper materials can lead to improved energy efficiency, reducing the overall operating costs.
Dimensional Specifications
Dimensional specifications are imperative for ensuring that large ball mills operate at their optimal capacity. The design includes various dimensions such as diameter, length, and thickness of the shell. These specifications determine the mill’s capacity to hold and process materials effectively.
- Diameter: The diameter of a ball mill typically ranges from a few meters to over ten meters. A larger diameter allows for more significant amounts of material to be processed at once.
- Length: The length of the mill can also vary; longer mills generally lead to finer grinding, as they provide more time for the particles to be ground down.
- Shell Thickness: Thicker shells are often used in high-capacity mills to withstand increased internal pressure and grinding forces.
A well-designed ball mill adheres to optimal dimensional specifications, allowing it to maximize performance and efficiency while minimizing maintenance needs.
Load Configurations
Load configurations in a large ball mill refer to how the materials being ground are loaded into the mill and how they interact during operation. This aspect is essential for optimizing the milling process.
Different load configurations can lead to variations in grinding efficiency and product quality. Some typical considerations include:
- Ball Charge: The size and distribution of balls within the mill affect the grinding effectiveness. A well-balanced charge maximizes contact with the material and promotes better grinding.
- Material Load: The amount and type of materials loaded into the mill determine grinding efficiency. Overloading can lead to reduced performance and increased wear on the mill.
- Orientation and Speed: The orientation of the mill and the rotational speed also dictate how the materials are processed. Ensure that the mill operates at optimal speed to maintain energy efficiency.
By paying attention to these load configurations, operators can significantly enhance the functioning of large ball mills and improve the quality of the end product.
Key Point: The design features of large ball mills are not merely for show; they serve practical purposes that directly impact efficiency, maintenance, and output quality.
Applications in Various Industries
Large ball mills find their significance in multiple industrial sectors due to their versatility and efficiency in grinding materials. These machines play a crucial role in several processes, whether in extracting valuable minerals or producing fine chemicals. Understanding their applications helps manufacturers optimize operations, ensuring better output quality and reduced costs.
Mineral Processing
In mineral processing, large ball mills are pivotal for crushing and grinding raw materials. These mills significantly impact the three stages of mineral processing: comminution, which involves the reduction of particle size; concentration, which enhances the ore's economic value; and the subsequent extraction processes.
The power of large ball mills lies in their ability to handle vast quantities of feed material, achieving finer particle sizes without extensive energy costs. For instance, miners often rely on these mills for more efficient separation of gold or copper from low-grade ores. Additionally, the resilience of these mills contributes to lower maintenance costs, making them a favorable choice for mining operations.
Metallurgy
In metallurgy, the use of large ball mills is vital for preparing materials for smelting or refining. Grinding materials into finer particles allows for better reaction rates during the metallurgical process. The homogeneous particle size achieved through milling enhances prospected attributes such as strength or ductility in metals.
Furthermore, the operation's kinetics can significantly affect the outcomes. Large ball mills can be tailored to optimize the milling environment, altering factors like rotational speed and charge volume to achieve desired results in alloy production. Metallurgists increasingly depend on these mills to balance quality with productivity, making large ball mills indispensable in advanced material design.
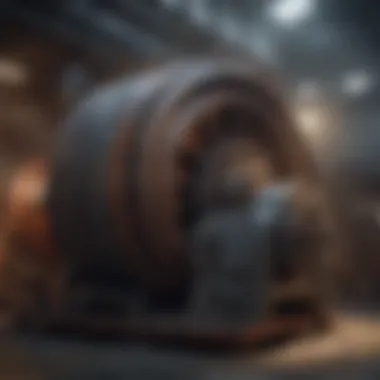
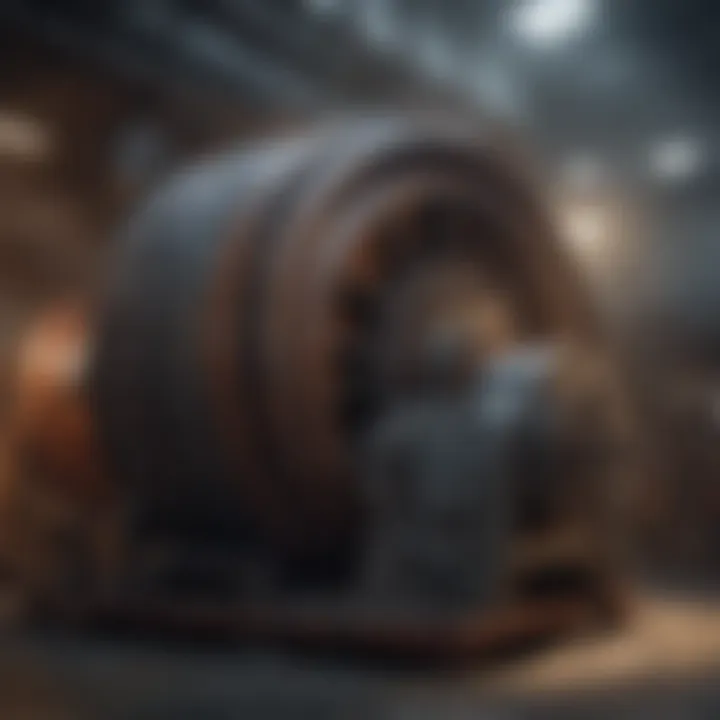
Chemical Manufacturing
In chemical manufacturing, large ball mills offer a unique advantage by efficiently blending raw materials with minimal energy consumption. These mills serve various purposes, from grinding pigments in paint to encapsulating nanoparticles for pharmaceuticals. Their ability to maintain uniform mixing and particle size distribution ensures product consistency across batches.
Moreover, large ball mills contribute to process intensification. For example, when producing specific chemicals, the milling process can enhance reaction speeds, enabling reduced processing times. Many chemical manufacturers notice enhanced output while simultaneously lowering operational costs and resource consumption.
Overall, large ball mills hold a substantial role across industries, with each application presenting opportunities for efficiency and innovation. Their design and operational principles align directly with the needs of mineral processing, metallurgy, and chemical manufacturing, making them critical components in diverse industrial settings.
Operational Efficiency of Large Ball Mills
Operational efficiency in large ball mills is a crucial aspect of chemical processing. These mills play a significant role in achieving desired product quality while ensuring cost-effectiveness. Efficiency encompasses a range of factors including energy consumption, material utilization, and overall operational output. Improving efficiency can lead to substantial savings and enhanced production capacity, making it a focus for many operators and engineers in the field.
A well-optimized ball mill ensures minimal energy wastage, which is particularly important in industries that rely heavily on energy for production. Also, it affects the lifespan of the equipment. Significant downtime due to inefficiency can lead to increased maintenance costs and lost revenue. Hence, understanding operational efficiency is key to maximizing the benefits of large ball mills in production environments.
Factors Influencing Performance
Several elements play a role in the performance of large ball mills. These include:
- Material Characteristics: The type and properties of the materials processed can significantly impact efficiency. Harder materials often require more energy, thus affecting overall operational costs.
- Mill Speed: The rotational speed of the mill influences the motion of the grinding media. An optimal speed helps achieve the best grinding efficiency. This can vary based on the specific mill design and material properties.
- Ball Size and Load: The size and quantity of balls used in the mill affect the quality of the grind. A balanced load ensures effective breaking of particles and enhances the surface area for reactions in chemical processing.
- Temperature Control: In many chemical processes, temperature can influence both the reaction rates and the efficiency of the milling process. Properly managing temperature can lead to better performance.
- Feed Size and Distribution: The size of the material entering the mill impacts the grinding efficiency. Smaller feed sizes can often lead to better throughput and enhanced operational performance.
Comparison with Alternative Technologies
When evaluating operational efficiency, it is important to compare large ball mills with alternative milling technologies.
- Vertical Mills: These mills may consume less energy for certain applications and provide better efficiency. They often handle finer materials better compared to large mills.
- Hammer Mills: While they can be effective for specific materials, they generally do not achieve the same size reduction as ball mills. However, they can offer lower operational costs for specific tasks.
- Stirred Mills: These are known for their high efficiency and ability to grind finer particles, which could be beneficial depending on the application.
Maintenance of Large Ball Mills
Importance of Maintenance of Large Ball Mills
Maintenance of large ball mills is critical for ensuring their longevity and operational efficiency. These mills, which are central to many chemical processing applications, undergo significant wear and tear during operation. Proper maintenance practices help to avoid unexpected failures, which can lead to costly downtime and repair. An emphasis on routine maintenance can enhance performance, optimize energy consumption, and ensure the safety of operations.
Regularly maintained equipment yields consistent results, benefiting production quality and efficiency. Understanding the maintenance of these large machines is essential for operators and facility managers alike. It involves a proactive approach to identifying and addressing potential issues before they escalate. This understanding can also function as a foundation for establishing best practices that align with industry standards.
Regular Maintenance Practices
Implementing a structured regular maintenance program can significantly enhance the operational life of large ball mills. Here are key aspects of regular maintenance practices:
- Lubrication: Proper lubrication of moving parts is crucial. Inadequate lubrication can lead to friction, causing wear and heat generation.
- Inspection: Regular inspection should be performed on components such as gears, bearings, and liners. Detecting signs of wear early enables timely replacement or repair.
- Cleaning: Build-up of material can hinder machine efficiency. Regular cleaning of the mill's interior and external surfaces helps maintain optimal function.
- Alignment Checks: Misalignment can cause excessive vibrations and material damage. Regular checks ensure that the machine operates smoothly.
- Calibration: Equipment should be calibrated regularly to meet operational standards and specifications. This helps maintain product quality and process efficiency.
These practices, when consistently applied, contribute to sustained high performance and reduced likelihood of breakdowns.
Troubleshooting Common Issues
Troubleshooting is an integral part of the maintenance routine. Being aware of common issues that may arise during operation can lead to quicker resolutions. Some typical problems include:
- Vibration: Excessive vibrations can indicate misalignment or worn bearings. Monitoring vibration levels can help detect issues early.
- Noise: Unusual sounds, such as grinding or screeching, can signify component failure. Identifying the source of noise is critical for timely intervention.
- Temperature Fluctuations: Abnormal temperature changes in bearings or motors can indicate lubrication failure or overheating. Regular monitoring of temperature is essential.
- Wear on Lining: Insufficient lining can lead to material loss. Regular inspections help ensure linings are in good condition.
When encountering these issues, a systematic approach to troubleshooting is beneficial. Operators should refer to maintenance logs, usage data, and manufacturer recommendations when diagnosing problems.
Effective maintenance practices not only optimize the operational capacity of large ball mills but also extend their service life, safeguarding investments in machinery.
Technological Advancements in Large Ball Mills
Technological advancements in large ball mills are critical for enhancing their performance and efficiency. This section delves into various innovations that have emerged in recent years, focusing on automation systems and design improvements. Understanding these advancements helps stakeholders in chemical processing not only to implement them effectively but also to recognize their importance in achieving operational goals.
Automation and Control Systems
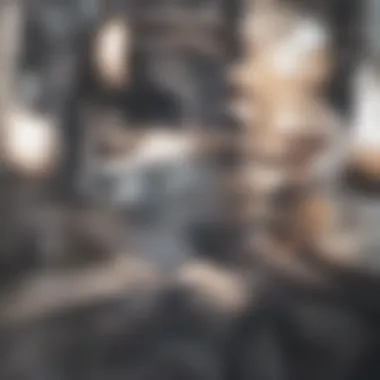
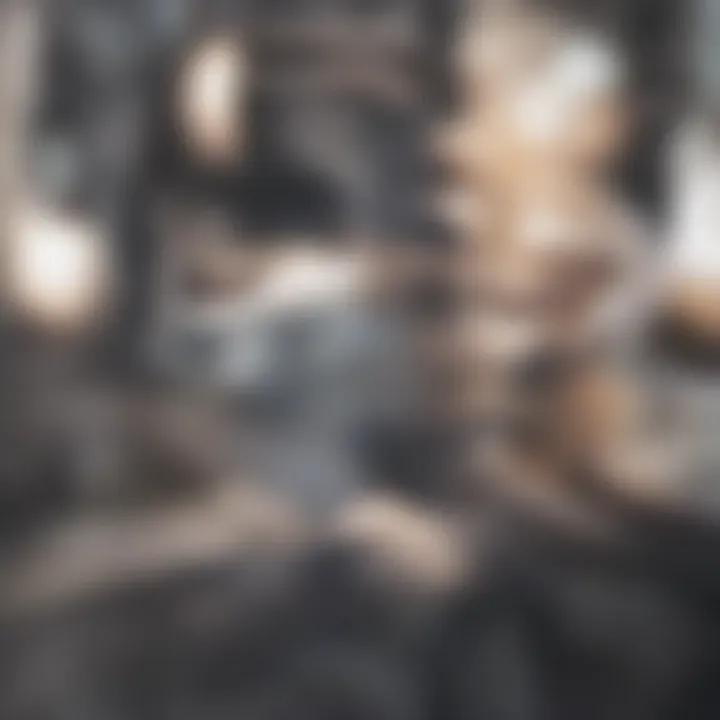
Automation in large ball mills significantly enhances operational control. Modern systems incorporate sensors and software that monitor various parameters like temperature, pressure, and load conditions in real-time. This ability for dynamic monitoring enables operators to adjust settings promptly, ensuring optimal performance.
Some key advantages of automation include:
- Enhanced Precision: Automated systems maintain consistent parameters across operations, reducing variability that can impact final product quality.
- Reduced Labor Costs: With automated control, human oversight in routine tasks decreases. This not only lowers labor costs but also minimizes human error.
- Improved Safety: Sensors can detect problems such as overheating or overload, allowing for immediate corrective actions. This proactive approach can prevent accidents and extend the lifespan of the equipment.
Leading control systems, such as Siemens and Allen-Bradley, offer tailored solutions for integration into existing mill frameworks. By employing advanced algorithms, they ensure that large ball mills operate at peak efficiency.
Innovations in Design and Efficiency
As technology progresses, the design of large ball mills also evolves. Innovations focus on enhancing efficiency and minimizing energy usage, critical factors in today’s resource-conscious environment.
For instance, the introduction of more efficient grinding media contributes significantly to performance. New materials, like ceramic beads or high-carbon steel balls, provide better grinding effectiveness and longevity. Moreover, the design of the mills themselves has seen improvements:
- Optimized Geometry: Advanced computational design tools allow engineers to create mill geometries that maximize material exposure and reduce energy consumption.
- Liner Materials: Modern liners, made from wear-resistant materials, enhance the lifespan of mills. Brands like Metso and FLSmidth are pioneers in this area, offering solutions that increase productivity while reducing maintenance costs.
- Energy Recovery Systems: These systems capture and reuse energy during operations, leading to lower operational costs and an eco-friendlier process.
In summary, the technological advancements in large ball mills, especially in automation and design, play a vital role in enhancing efficiency and operational performance. These innovations not only contribute to better output but also promote sustainability in industrial practices.
"It is essential for the industry to embrace new technologies, like automation and advanced material designs, to stay competitive and efficient in a rapidly changing market."
Equipped with this understanding, professionals in the field are better positioned to leverage technological advancements to their advantage.
Environmental Considerations
In the context of large ball mills used in chemical processing, environmental considerations are paramount. These mills, while effective for various industrial applications, present specific challenges and opportunities in terms of their impact on the environment. An understanding of these considerations enhances not only regulatory compliance but also operational efficiency, making this an important focus for professionals in the field.
Waste Management and Recycling
Effective waste management practices are critical for minimizing the environmental footprint of large ball mills. Waste generated in the ball milling process can include used grinding media, contaminated materials, and residual chemicals. Proper disposal and management of these wastes are essential.
- Collection Systems: Implementing robust collection systems can prevent waste from contaminating the surrounding environment. This can involve dedicated containers for different types of waste, such as metal, ceramic, or polymer grinding media.
- Recycling: Recycling plays a significant role in sustainability. Ball mills can utilize recycled materials as feedstock, supporting circular economy principles. For instance, used grinding media can often be repurposed after appropriate processing.
- Regulatory Compliance: Following local and international regulations regarding waste management is vital. Non-compliance not only leads to environmental damage but can also result in hefty fines and negative public relations for companies involved.
Sustainability Practices in Operation
The operational life of large ball mills can be optimized through sustainable practices. Sustainability in this context refers to balancing efficient production with environmental responsibility.
- Energy Efficiency: Using energy-efficient motors and variable frequency drives can significantly reduce the energy consumption of large ball mills. This leads not only to financial savings but also to a decrease in greenhouse gas emissions.
- Water Usage: Large ball mills may require substantial amounts of water for cooling and dust suppression. Implementing closed-loop water systems can save water and reduce waste.
- Emission Control: It is crucial to install systems to control emissions from the milling process. This can include filters, scrubbers, and other air quality management technologies that minimize harmful pollutants.
"By adopting sustainable practices, large ball mills can greatly contribute to both industrial efficiency and environmental protection."
Focusing on these environmental considerations is not merely a matter of complying with regulations. It also offers long-term benefits in terms of brand reputation and operational efficiency. In the evolving landscape of industrial practices, businesses that prioritize environmental considerations in their processes will increasingly stand out in the market.
Future Trends in Large Ball Mill Technology
The landscape of large ball mills is undergoing rapid transformation, influenced by advancements in technology and changing industry needs. The importance of exploring future trends in large ball mill technology cannot be overstated, as these trends dictate operational efficiency, cost-effectiveness, and environmental impact.
Innovation is essential for companies aiming to maintain a competitive edge. As industries increasingly adopt sustainability measures, the role of large ball mills must evolve to meet these demands. Emerging technologies can enhance not just performance but also the sustainability profiles of these critical processing units. Therefore, understanding these future developments is vital for organizations looking to maximize productivity while minimizing their ecological footprint.
Industry Predictions
Outlook for the large ball mill industry is bright, with several key trends emerging. First, there is a growing emphasis on automation. Integration of smart technologies allows for optimal control and monitoring. Automated systems can significantly reduce human error and enhance operational efficiency. For example, predictive maintenance technologies can forewarn operators about potential failures, thereby reducing downtime and maintenance costs.
Another important trend is the shift toward energy efficiency. Ball mills consume substantial energy. Innovations that focus on energy-efficient operations are needed. Some manufacturers are developing mills that utilize advanced drive systems, which can cut energy consumption by up to 20%. Also, alternative materials are being explored to make mill linings that can withstand wear while being more environmentally friendly.
Moreover, there is an increasing interest in data analytics. Using big data to track mill performance offers insights that can refine operations. Techniques like Machine Learning can analyze trends and suggest improvements, enhancing both throughput and product quality.
Research Opportunities and Challenges
Research in large ball mill technology faces various challenges and opportunities. One significant opportunity lies in the investigation of new materials for construction. Developing composites that are lightweight yet durable presents a potential breakthrough in efficiency. Moreover, understanding the interaction of different materials in grinding processes can improve performance significantly.
Conversely, challenges exist in the integration of new technologies. Companies may face resistance to change from established practices. Furthermore, there is a need for extensive testing to evaluate how new methods will perform in real-world settings.
Additionally, experts must address the environmental regulations that continue to evolve. Balancing operational efficiency with compliance will be critical. Researchers must design mills that not only perform well but also adhere to strict environmental standards.