Graham Hydraulics: Principles and Applications
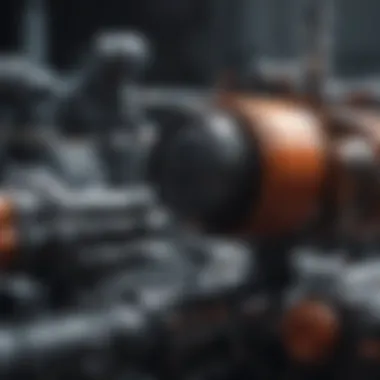
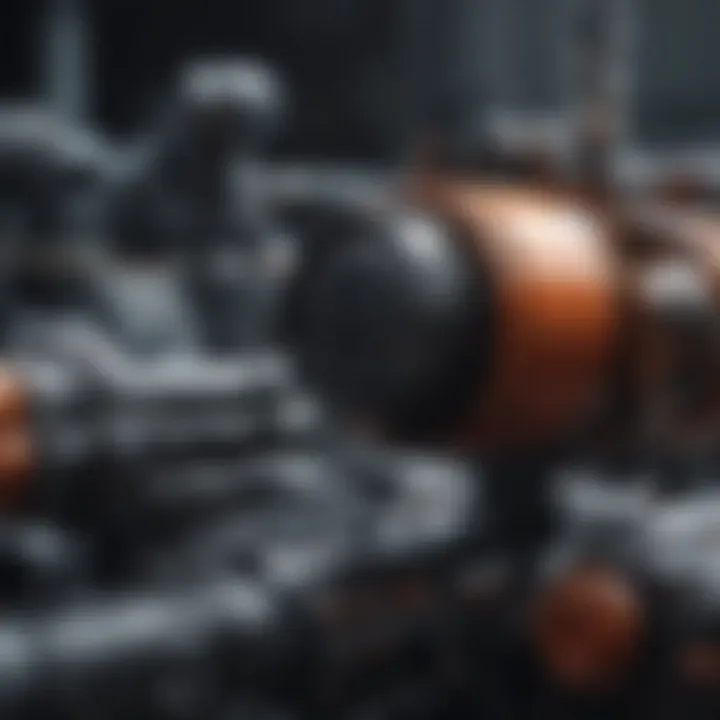
Intro
Graham Hydraulics plays a significant role in various sectors, from manufacturing to agriculture. Understanding the mechanics behind this technology can enhance efficiency and innovation. This section highlights key points that will be discussed in the article, including fundamental principles and applications.
Background and Context
Overview of the research topic
Hydraulics involves the use of fluids to create mechanical movement. When applied to Graham Hydraulics, it refers to a specific approach in hydraulic systems, which utilizes pressurized fluid to operate machinery. Understanding this helps in knowing how machines perform tasks such as lifting or moving heavy objects with ease.
Historical significance
The history of hydraulics dates back to ancient civilizations. However, Graham Hydraulics emerged notably in the 20th century. Its evolution has been tied to advancements in engineering and technology. Today, it stands as a crucial part in various industries, making tasks safer and more efficient.
Key Findings and Discussion
Major results of the study
Graham Hydraulics is integral to numerous applications. Here are some notable areas:
- Construction: Hydraulic systems are used for cranes and excavators, enabling precise movements.
- Agriculture: Equipment like tractors rely on hydraulic mechanisms for various functions, including plowing and lifting.
- Manufacturing: Hydraulic presses transform raw materials into finished products, showcasing strength and efficiency.
Detailed analysis of findings
Advancements in hydraulics technology are continuously evolving. These include:
- Smart Hydraulic Systems: Integration of sensors allows for real-time data acquisition, optimizing performance.
- Energy Efficiency: New designs minimize waste, contributing to sustainability efforts in many sectors.
"The continuous improvement in hydraulic technology signifies a shift towards sustainable practices across industries."
Understanding the implications of these advancements can provide insights into future trends in machinery and environmental responsibility.
Prologue to Graham Hydraulics
Graham Hydraulics represents a significant area of study within the field of engineering, focusing on the principles and applications of hydraulic systems. This branch of engineering deals with the mechanical properties of fluids, particularly how they can be controlled and used to transmit power. Understanding Graham Hydraulics is essential for various industries, where it underpins many of the machines and tools that we use every day.
The relevance of hydraulic systems lies in their efficiency and ability to generate high amounts of force with relatively small volumes of fluid. In this context, Graham Hydraulics serves as a critical point of research, especially when addressing modern engineering challenges. Its applications span a wide array of fields, including manufacturing, construction, and automotive engineering, highlighting the versatility of hydraulic functions.
One of the core benefits of studying Graham Hydraulics is its relationship with energy efficiency. Hydraulic systems can often perform tasks more effectively than mechanical systems, reducing energy consumption while maximizing output. As environmental concerns grow, the integration of sustainable practices within hydraulic engineering becomes more pertinent.
Moreover, the advancements in hydraulic technology present opportunities for greater automation and smarter systems. This transformation is pivotal in the context of smart manufacturing and Industry 4.0. Therefore, the significance of Graham Hydraulics extends beyond basic fluid mechanics; it impacts how industries innovate and respond to new challenges.
In summary, the exploration of Graham Hydraulics is crucial for those who seek a deeper understanding of hydraulic mechanisms and their applications. This knowledge not only benefits academic pursuits but also provides professionals and industries with the tools to enhance productivity and sustainability in an increasingly complex technological landscape.
Historical Context
Understanding the historical context of Graham Hydraulics provides a necessary framework for comprehending its significance in modern engineering and technology. The evolution of hydraulic systems has transformed industries, enabling diverse applications from manufacturing to aerospace. By studying the origins and developments in hydraulic engineering, one can grasp the innovative spirit that drove engineers to optimize fluid power and its applications.
Origins of Hydraulic Systems
The origins of hydraulic systems can be traced back to ancient civilizations. The earliest uses of hydraulic principles were seen in ancient Egypt, where water-lifting devices such as the shaduf were implemented. These devices relied on the simple mechanics of leveraging a fulcrum to lift water from lower to higher elevations. Similarly, the Greeks contributed significantly, utilizing water wheels for milling grain. The basic concepts of fluid dynamics were, albeit rudimentary, being applied in pragmatic environments.
Throughout the centuries, the understanding of hydraulics evolved. In the 17th century, mathematicians like Blaise Pascal began formally articulating principles underlying fluid behavior, essentially paving the way for modern hydraulics. This period marked a shift where empirical knowledge began to align with scientific theorization, offering deeper insights into fluid mechanics.
Key Developments in Hydraulic Engineering
The 18th and 19th centuries saw significant advancements in hydraulic engineering. Notable inventions included the hydraulic press, developed by Joseph Bramah in 1795, which demonstrated Pascal's Principle in action. This device illustrated how pressure applied to a confined fluid is transmitted undiminished in all directions. The implications were profound—allowing for transformations in manufacturing and mechanical tasks that required substantial force.
The industrial revolution catalyzed further developments. Hydraulic systems became central to lifting equipment, railways, and major construction projects. The implementation of hydraulic jacks revolutionized heavy lifting, making it more efficient and less labor-intensive.
In the 20th century, advancements in materials and technology enriched hydraulic systems' reliability and efficiency. The introduction of electronic controls and automation saw hydraulic technology being integrated into many sectors, further exemplifying its versatility and effectiveness in handling tasks that require power and precision.
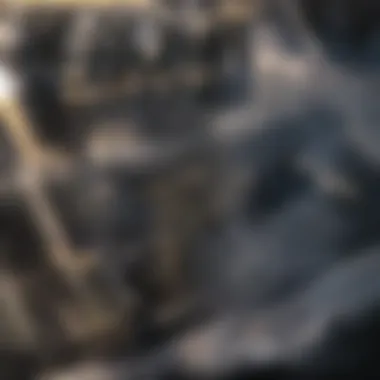
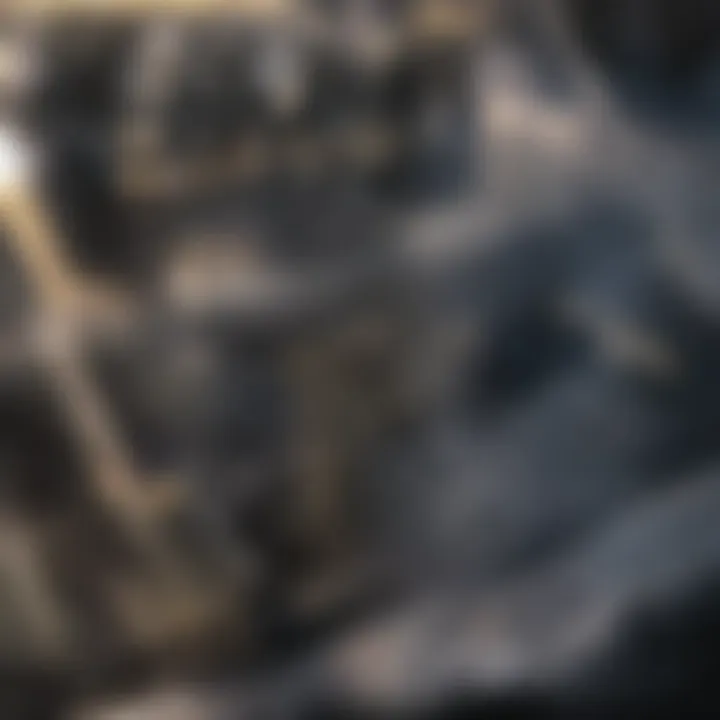
Today, understanding these historical advancements is crucial for students and professionals. It provides insight into not only how these systems function but also their impact on various industries and technologies. The path from simple water-lifting devices to complex systems illustrates human ingenuity and the ongoing pursuit of innovation in hydraulic systems.
Basic Principles of Hydraulics
Understanding the basic principles of hydraulics is essential to grasp the functionality and advantages of Graham Hydraulics. Hydraulics involves the use of incompressible fluid to transmit power. This technique is widely applicable across diverse industries, including manufacturing, automotive, and construction. The significance lies in the efficient transfer of energy and the mechanical advantages that hydraulic systems provide.
One of the most critical aspects to consider is how these systems can convert small force inputs into larger outputs. This is vital for numerous applications where heavy lifting or movement is necessary. Furthermore, hydraulics allows for precise control of machinery and tools, making it indispensable in many technical fields.
Pascal’s Law
Pascal’s Law is a cornerstone of hydraulic principles. It states that when pressure is applied to a confined fluid, the pressure change occurs uniformly throughout the fluid. This uniform transmission of pressure enables hydraulic systems to function effectively. It applies not only to the diameter of the pistons used but also to the efficiency of energy transfer.
In practical terms, if a small piston with a small area is used to apply force to a liquid, that force will cause a larger piston to move, even if it is a larger area. This amplification of force is what makes hydraulic systems beneficial for heavy machinery applications.
- Formula: Pressure (P) = Force (F) / Area (A)
- Applications: Used in hydraulic brakes, lifts, and press systems.
"Pascal’s principle is pivotal in making hydraulic machines effective and reliable."
Hydraulic Pressure and Flow
Hydraulic pressure and flow are interrelated concepts in understanding Graham Hydraulics. Pressure refers to the amount of force exerted by the fluid per unit area. It determines how much work can be done by the hydraulic system. Higher hydraulic pressure correlates with increased power output.
Flow, on the other hand, refers to the volume of fluid moving through the system per unit time. It is crucial for determining the speed at which a hydraulic actuator can operate. To manage and optimize system performance, it is necessary to balance both pressure and flow, ensuring adequate fluid movement for operational efficiency.
- Important factors to monitor include feedback mechanisms and pressure gauges.
- The use of variable displacement pumps can improve efficiency by adjusting the flow rate.
Managing these principles effectively increases the reliability and functionality of hydraulic systems. They demonstrate how vital hydraulic technology is to modern industry.
Key Components of Graham Hydraulic Systems
In the realm of Graham Hydraulics, understanding the key components is essential to appreciating how these systems function optimally. Each element contributes significantly to the overall effectiveness and efficiency of hydraulic applications. With proper comprehension, one can discern not only their operational roles but also the potential for improvements and innovations within hydraulic designs.
Cylinders and Pistons
Cylinders and pistons form the core of any hydraulic system. The cylinder, usually a robust metal tube, houses the piston, which is a movable part that translates hydraulic energy into mechanical motion. The operation depends heavily on the principles of fluid dynamics. As hydraulic fluid enters the cylinder, it creates pressure that forces the piston to move.
Importance:
- Force Generation: Pistons can create substantial forces relative to their size. This translates into powerful movements which are essential in various applications, from industrial machinery to automotive engineering.
- Precision Control: The capability to control the movement of the piston allows for precise operations in various fields, ensuring that tasks are performed accurately.
- Durability: Materials used for cylinders and pistons are chosen for their strength and resistance to wear, ensuring long-term reliability.
However, attention must be paid to maintenance. Ensuring that seals are intact and that there are no leaks is crucial for maintaining pressure and performance. Poor maintenance can lead to significant operational issues and increased costs.
Hydraulic Pumps
Hydraulic pumps are vital in transforming mechanical energy into hydraulic energy. These pumps create the flow of hydraulic fluid through the system. Without them, the entire hydraulic process would be ineffective.
Importance:
- Fluid Movement: Pumps maintain a steady flow of fluid, enabling the smooth operation of hydraulic systems. This is critical in settings where quick response times are necessary.
- Types of Pumps: There are various types of pumps, including gear pumps and piston pumps. Each has its function and suitability depending on application needs. For example, gear pumps are reliable for lower pressure environments, while piston pumps excel under higher pressures.
- Efficiency: Selecting the right pump can greatly enhance the operational efficiency of a system, thus reducing energy consumption and costs.
Like any other part, pumps require proper monitoring to ensure functionality. Overheating or cavitation can lead to failures, which underlines the importance of regular maintenance and assessments.
Valves and Controls
Valves and controls play a crucial role in directing the flow of hydraulic fluid throughout the system. Their primary function is to manage pressure and flow rate, which are essential for the system's performance and safety.
Importance:
- Flow Regulation: Valves can either allow or restrict fluid flow, making them essential for controlling the movement of machinery and ensuring that components receive the proper amount of hydraulic fluid.
- Safety Mechanisms: Many valves serve as safety devices that prevent over-pressurization of hydraulic systems. This is vital in maintaining system integrity and protecting against failures.
- Automation Benefits: Modern systems increasingly incorporate automated controls in their hydraulic mechanisms. This enhances efficiency and reduces the need for human intervention, thus streamlining operations.
Applications of Graham Hydraulics
The applications of Graham Hydraulics are vital for various industries. Hydraulic systems enable efficient movement and control in machines and processes where manual effort is inadequate. By utilizing fluid dynamics, hydraulic technologies facilitate tasks across numerous sectors. Their impact spans industrial operations, construction, and automotive engineering, making them indispensable for modern capabilities.
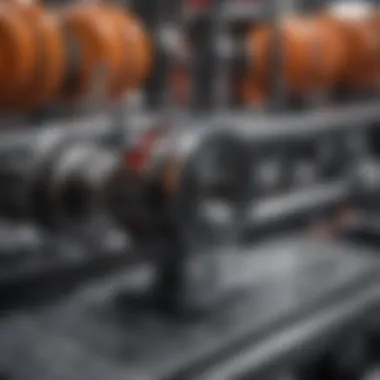
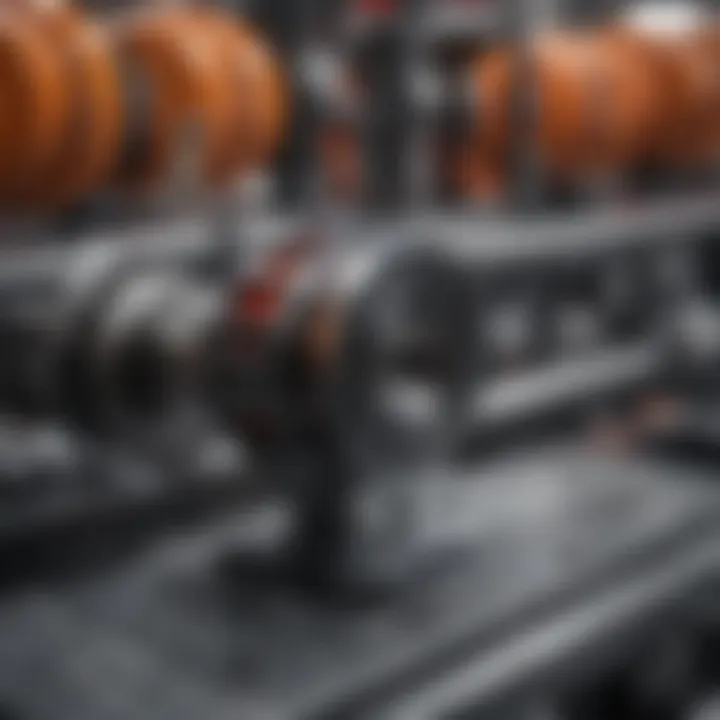
Industrial Applications
In industrial settings, Graham Hydraulics plays a key role in operational efficiency. These hydraulic systems are often found in manufacturing equipment, such as hydraulic presses and forklifts. They perform tasks like metal forming, material handling, and assembly processes.
Implementing hydraulic technology helps achieve precise control in production lines, which can significantly enhance productivity. Benefits include:
- Increased Power: Hydraulic systems can lift heavy loads that would be impossible manually.
- Versatility: These systems can be adapted for various tasks in diverse sectors, such as food processing or textiles.
- Compact Design: Compared to mechanical systems, hydraulics can provide the same power in a smaller space, saving valuable floor area.
Construction and Heavy Machinery
The construction sector relies heavily on Graham Hydraulics for creating and maintaining infrastructure. Equipment like excavators, cranes, and bulldozers utilize hydraulic systems to operate effectively. The power provided by hydraulic mechanisms allows these machines to handle heavy loads with ease.
Some specific applications in construction include:
- Excavation: Hydraulic cylinders enable digging deep into the ground accurately.
- Lifting: Heavy materials, like steel beams, can be lifted effortlessly using cranes fitted with hydraulic systems.
- Drilling: Hydraulic rigs are essential for drilling into tough materials, making it crucial for foundation work.
This technology allows for greater safety and precision, reducing risks of accidents during operation.
Automotive Engineering
In automotive engineering, Graham Hydraulics is pivotal in vehicle systems. Hydraulics are used in areas like steering, braking, and suspension. Vehicles such as cars and trucks benefit from these applications for enhanced control and safety.
Key functions include:
- Power Steering: This system allows drivers to steer vehicles with less effort, improving maneuverability.
- Braking Systems: Hydraulic brakes provide responsiveness, ensuring vehicles can come to a stop swiftly and safely.
- Suspension: Hydraulic suspension systems adjust the vehicle’s ride height in real-time, improving comfort and handling.
Environmental Considerations
The significance of environmental considerations in Graham Hydraulics cannot be overstated. As industries increasingly adopt hydraulic systems, the need to evaluate their environmental footprint becomes critical. Hydraulic technology, while efficient and effective for a variety of applications, also poses potential risks to ecosystems. Understanding these risks and addressing them through sustainable practices is essential for the long-term viability of hydraulic systems.
Sustainability in Hydraulic Systems
Sustainability in hydraulic systems involves reducing negative environmental impacts while maintaining efficiency and function. Key elements include:
- Material Selection: Using biodegradable fluids and sustainable materials can minimize the ecological impact. For instance, adopting bio-based hydraulic fluids cuts down on contamination risks.
- Energy Efficiency: Modern hydraulic systems are becoming more energy-efficient, which supports sustainability. Implementing variable speed drives in pumps can optimize energy consumption and reduce waste.
- Recycling and Reusing Components: This practice extends the lifecycle of system components. For example, remanufacturing hydraulic pumps can prevent them from ending up in landfills, reducing resource extraction.
Creating a balance between hydraulic performance and environmental responsibility is crucial. As advancements in technology continue, the implementation of smart hydraulics can lead to further efficiency improvements and reduced carbon footprints.
Impact of Hydraulic Technology on Ecosystems
Hydraulic technology can have both positive and negative impacts on ecosystems. On one side, the evolution of hydraulic systems contributes to development projects that can enhance living standards. However, it is important to recognize possible adverse environmental effects. Several considerations include:
- Water Usage: Hydraulic systems often require significant amounts of water for operation. This can lead to depletion of local water resources, especially in arid regions. Managing water usage effectively is critical.
- Contamination Risks: If hydraulic fluids leak, they can contaminate soil and water sources. Careful monitoring and maintenance are vital to mitigate these risks.
- Habitat Disruption: The installation of hydraulic systems can cause land alteration and habitat destruction. Minimizing environmental disruption during installation and usage is necessary to preserve biodiversity.
"The intersection of hydraulic technology and ecosystems requires strategic considerations to ensure current and future sustainability."
Advancements in Hydraulic Technology
Hydraulic technology is constantly evolving. These advancements play a significant role in the efficiency and functionality of hydraulic systems. Innovation in this field leads to better performance, reduced environmental impact, and enhanced safety. This section examines two critical areas: Smart Hydraulics and Automation, and Innovations in Fluid Dynamics.
Smart Hydraulics and Automation
Smart hydraulics integrate advanced technologies into traditional hydraulic systems. These systems utilize sensors, controllers, and data analytics to optimize performance. The primary benefits include improved accuracy and reliability. For example, sensors can monitor pressure and flow continuously. This real-time data allows the system to adjust automatically, ensuring optimal functionality.
Automation in hydraulic systems further enhances efficiency. By minimizing human intervention, automation reduces error rates and increases safety. Hydraulic machinery, such as excavators or cranes, can now function autonomously in various conditions. The development of programmable logic controllers (PLCs) and advanced software creates systems that can adapt to changing environments.
Important features of smart hydraulics include:
- Real-time monitoring: Continuous data collection helps identify potential issues before they escalate.
- Predictive maintenance: Data analytics can predict failures, reducing downtime and maintenance costs.
- Energy efficiency: Intelligent control systems optimize power usage, lowering operational costs.
Innovations in Fluid Dynamics
Fluid dynamics is central to hydraulic systems. Recent innovations in this area have improved the understanding and manipulation of fluid behavior. New techniques allow for better control and efficiency of hydraulic systems.
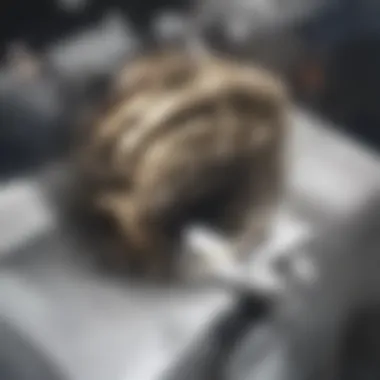
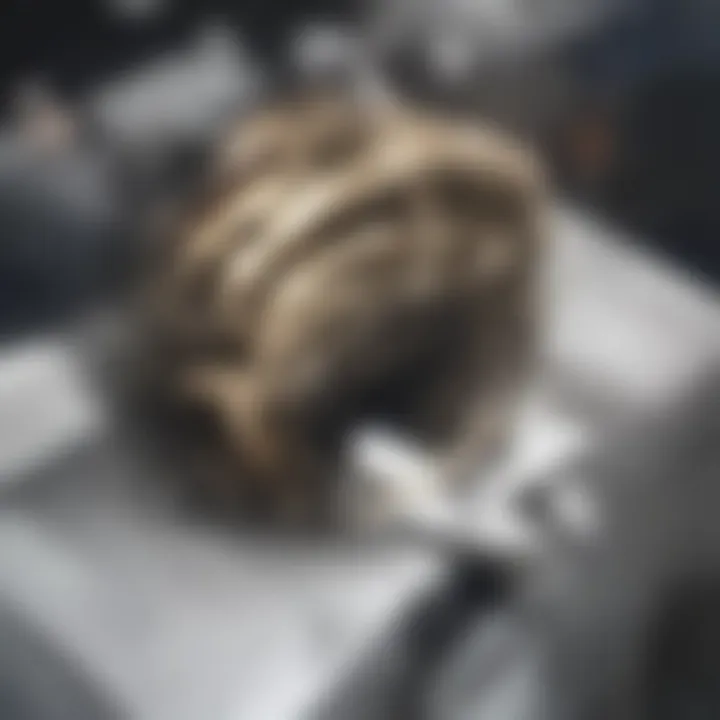
Recent developments in computational fluid dynamics (CFD) have transformed the design process. CFD provides simulations of fluid flow, allowing engineers to visualize and optimize designs before physical prototypes are built. This capability reduces development time and costs.
Key innovations in fluid dynamics include:
- Advanced Materials: New materials enhance fluid properties, allowing for less friction and better flow.
- Microfluidics: This involves studying fluids at a microscopic scale. Applications can be found in medicine and biotechnology, reflecting the shift in hydraulic applications.
- Turbulence Management: Better management of turbulence ensures smoother and more efficient operation.
"Understanding fluid dynamics is crucial for maximizing the efficiency of hydraulic systems."
These advancements help improve the overall performance and sustainability of hydraulic applications, making strides into the future. As these innovations continue, they hold the potential to revolutionize the entire hydraulic industry.
Challenges in Graham Hydraulics
The field of Graham Hydraulics is not without its challenges. Understanding these challenges is crucial for engineers and professionals involved in hydraulic systems. The importance of maintenance and reliability is highlighted, especially given that hydraulic systems are complex and subject to wear and tear. These systems support critical applications across industries, thus ensuring their optimal functionality is paramount. The maintenance demands require thoughtful strategies to avert operational failures that could lead to significant downtime and safety risks.
Moreover, energy efficiency concerns are becoming increasingly relevant as industries strive to reduce operational costs and environmental footprints. Addressing this challenge entails analyzing hydraulic systems for better performance, minimizing energy loss, and enhancing overall sustainability.
Significant attention must be given to both maintenance and energy concerns in Graham Hydraulics, given their implications for system design, operations, and environmental impact.
Maintenance and Reliability
Maintenance is a pivotal aspect of managing hydraulic systems. Regular inspections and servicing can prevent breakdowns and extend the life of equipment. Many factors contribute to the maintenance requirements of hydraulic systems, including:
- Fluid Quality: Contaminated fluid can cause wear in components, leading to failures. Keeping the hydraulic fluid clean is essential.
- Component Inspection: Regular checks on cylinders, pumps, and valves can help identify wear or damage before it results in failure.
- Preventative Maintenance Schedules: Establishing a routine maintenance plan can significantly reduce unplanned downtimes. A proactive approach is more cost-effective than reactive responses to failures.
The reliability of hydraulic systems is critical, especially in high-stakes environments such as construction and manufacturing. Failure to maintain reliability can lead to unexpected costs, safety hazards, and project delays. Hence, implementing rigorous maintenance protocols is essential.
Energy Efficiency Concerns
Energy efficiency is a growing concern in hydraulics systems. Hydraulic systems often consume considerable energy during operation, and improving this efficiency is beneficial both economically and environmentally. Key aspects to consider include:
- System Design: Engineers must design hydraulic systems to minimize energy losses. Proper sizing of components can lead to significant improvements.
- Pump Selection: Choosing the right pump type and size can reduce energy wastage. Variable displacement pumps, for instance, can adjust to the fluid demand, enhancing efficiency.
- Monitoring and Automation: Implementing sensors and automation technologies helps in monitoring system performance. This can lead to the identification of inefficiencies and optimizing operational procedures.
Maximizing energy efficiency in hydraulic systems not only reduces costs but also promotes sustainability. As the pressure grows on industries to adhere to environmental standards, addressing these concerns becomes increasingly critical.
Integrating energy-efficient practices into Graham Hydraulics is not merely a trend but a necessity for future advancements. By overcoming maintenance issues and enhancing energy efficiency, the industry can set a foundation for sustainable growth.
Future Trends in Hydraulic Systems
The realm of hydraulic systems is continuously evolving, shaped by advancements in technology and shifts in market needs. Understanding these future trends is essential for professionals in engineering and related fields, as they directly impact system design, efficiency, and environmental sustainability. This section delves into two main areas of interest: the influence of computational technologies and the emergence of new markets and applications in hydraulic systems.
Influence of Computational Technologies
Computational technologies are revolutionizing the design and implementation of hydraulic systems. Techniques such as computational fluid dynamics (CFD) allow engineers to simulate fluid movement and pressure conditions, enhancing system optimization. By employing sophisticated algorithms, these tools can predict performance under varying operational conditions without the need for extensive physical prototypes. This reduces development time and costs, leading to more efficient and reliable hydraulic systems.
- Benefits
- Design Optimization: Computational tools enable precise adjustments in hydraulic designs based on predictive modeling, improving performance.
- Cost Efficiency: Reducing the need for physical prototypes can save significant resources in research and development.
- Enhanced Precision: Simulation provides a clearer picture of how systems will behave in real-world scenarios, allowing for more accurate predictions and implementations.
Emerging Markets and Applications
As hydraulic technology advances, new markets and applications are emerging. Industries previously reliant on mechanical systems are now integrating hydraulic solutions to improve efficiency and performance. Some notable trends include:
- Agricultural Automation: With the rise in precision farming, hydraulic systems are increasingly used in machinery designed for targeted field applications, enhancing yield while minimizing resource use.
- Renewable Energy Sector: The integration of hydraulic systems in renewable energy, such as wind and hydroelectric power, is becoming more prominent, facilitating more effective energy conversion processes.
- Smart Manufacturing: The advent of Industry 4.0 has led to a focus on automation and data exchange. Hydraulic systems are being upgraded to feature IoT connectivity, allowing for real-time monitoring and predictive maintenance.
As industries continue to evolve, the demand for adaptable and innovative hydraulic solutions will only increase, pushing engineers to rethink traditional approaches.
In summary, the future of hydraulic systems is intertwined with advancements in computational technologies and the exploration of new markets. As these trends develop, they will define the direction of hydraulic engineering and its applications for years to come.
Endings
In this article, we explored various facets of Graham Hydraulics and its significance across multiple sectors. The exploration highlights several key points and insights that bear mentioning.
First and foremost, it is clear that hydraulic systems are pivotal in enhancing efficiency and effectiveness in industries such as construction, automotive engineering, and manufacturing. The mechanics behind Graham Hydraulics demonstrate the principles of fluid dynamics in action. This fluid power not only conserves energy relative to other systems but also allows for precise control in operation.
Another essential element is the impact of modern advancements in hydraulic technology. Innovations, especially in automation and smart hydraulics, have transformed traditional processes. This evolution leads to significant improvements in labor costs and overall productivity. The integration of these systems has become a standard practice, granting users the ability to monitor and control operations remotely.
Moreover, sustainability considerations cannot be overstated. As industries increasingly emphasize environmentally responsible practices, the hydraulic systems that allow for reduced waste and enhanced energy efficiency will continue gaining traction. A focus on sustainability will be increasingly important in the strategic development of hydraulic technology.
Interestingly, challenges persist even as technology advances. Maintenance remains a crucial concern. An effective maintenance strategy can prolong the life of hydraulic systems, which is essential as companies look to maximize their investments. Addressing energy efficiency is another challenge that need ongoing attention. With energy consumption becoming more scrutinized, finding ways to minimize it while maintaining functionality is vital.