Exploring Structural Simulation in Engineering Design
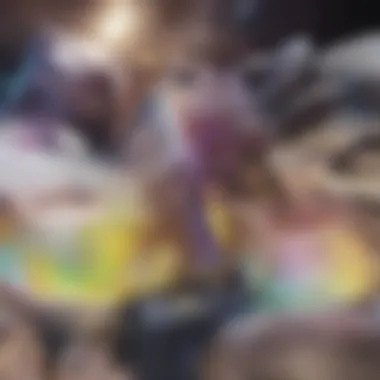
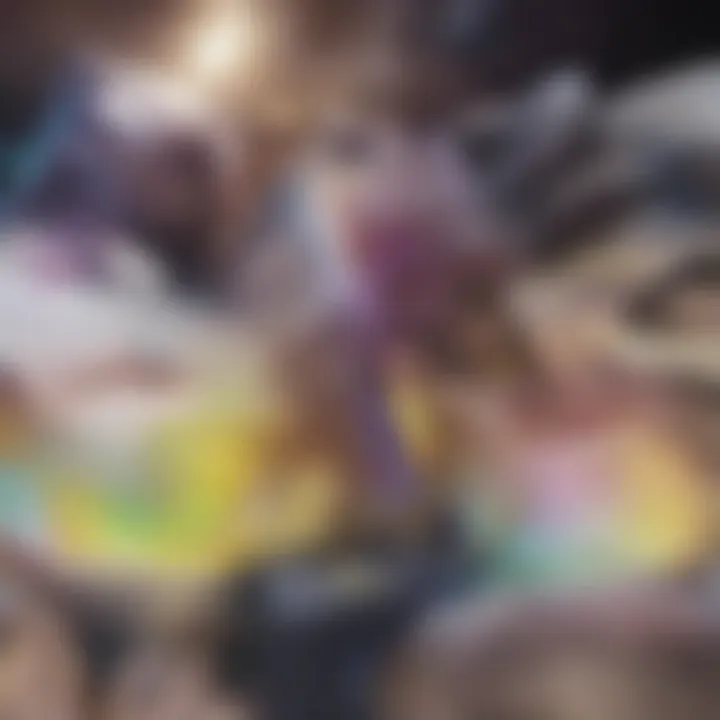
Intro
Structural simulation is a vital part of modern engineering and design, where understanding how structures will behave under various conditions becomes crucial. This involves more than just theoretical analysis; it encompasses a range of practical applications that inform decisions in real-world scenarios. As we venture deeper into this topic, we will dissect the essential concepts, methodologies, and future potential of structural simulation.
Background and Context
Overview of the Research Topic
At its core, structural simulation focuses on the predictive analysis of structures. Engineers employ various analytical techniques to ascertain how elements like buildings, bridges, and other infrastructures will respond to forces and environmental factors. This field harnesses advances in technology, computational power, and material science to create sophisticated models, offering insights that were previously unachievable.
Historical Significance
The roots of structural simulation trace back to early engineering practices, where the need to predict structural performance was recognized. Historically, methods such as static analysis and rudimentary models laid the groundwork for this discipline. Over time, with the advent of computer technology in the late 20th century, the practice transformed. Finite Element Analysis (FEA) emerged as a game-changer, enabling more complex simulations that incorporate multiple variables affecting structural integrity.
Key Findings and Discussion
Major Results of the Study
Recent advancements in structural simulation yield significant benefits. These innovations streamline the design process, reduce material wastage, and enhance safety protocols. By creating accurate models, engineers can anticipate and mitigate potential failures before structures are even built. This proactivity has widespread implications for urban planning and disaster management.
Detailed Analysis of Findings
In practice, the methodologies employed in structural simulation can be categorized into several key approaches:
- Computational Mechanics: This area applies the principles of mechanics to simulate physical processes. It often utilizes FEA and Computational Fluid Dynamics (CFD) to analyze how different forces interact within a structure.
- Material Modeling: Understanding how different materials behave under stress is essential. Simulation helps predict failure points, fatigue life, and long-term performance under various conditions.
- Dynamic Analysis: This aspect focuses on how structures react to dynamic loads, such as earthquakes or wind. By employing advanced simulation tools, engineers can optimize the design for resilience.
Effective structural simulation not only saves time and costs but also significantly improves structural safety.
The implications of these methodologies go beyond engineering. The integration of structural simulation into design processes influences regulatory standards, construction practices, and maintenance strategies. As technology advances, we can expect to see greater precision in simulations, ushering in an era where predictive modeling will play an even more critical role in infrastructure development.
Foreword to Structural Simulation
Structural simulation serves as a cornerstone in the fields of engineering and design, providing critical insights into how structures behave under various conditions. This area of study not only encompasses a plethora of methodologies but also highlights the intricate relationship between theoretical concepts and real-world applications. Understanding structural simulation is paramount for students, researchers, educators, and professionals alike, as it influences the decision-making process in design, safety assessments, and maintenance strategies.
Definition and Importance
Structural simulation refers to the computational representation of a structure's behavior under different loads and conditions. This technique allows engineers to predict how structures will respond to forces such as gravity, wind, and seismic events.
The significance of this field cannot be overstated. By employing simulation techniques, engineers can identify potential problems early in the design phase, reducing the likelihood of costly failures and ensuring safety. Moreover, the ability to visualize stress distribution and deformation patterns enables a more informed approach to material selection and design optimization. This not only enhances the efficiency of the project but also contributes to sustainable practices within the industry.
Historical Context
Historically, the practice of structural simulation has evolved significantly. In the early days, engineers relied on empirical methods and physical models to predict the behavior of structures. The introduction of computer-aided design (CAD) and finite element analysis (FEA) marked a turning point in this field. The 1960s saw the emergence of these technologies, allowing for more precise calculations and simulations.
As computational power increased, the models became more complex and detailed. This evolution paved the way for advanced techniques, such as computational fluid dynamics (CFD) and multibody dynamics (MBD), which are now commonplace in the industry. The richness of data and understanding that structural simulations provide continues to transform engineering practices, allowing for innovations that were once thought impossible.
Fundamental Principles of Structural Simulation
The realm of structural simulation is multifaceted, encapsulating key principles that are fundamental to understanding how structures behave under various conditions. Emphasizing these principles is crucial for professionals engaged in engineering and design, as they underpin effective methodologies for analysis and prediction. These principles offer insight into the essential elements and considerations necessary for achieving accurate simulation results and fostering informed decision-making.
Basic Concepts
At the core of structural simulation lie several basic concepts that shape how simulations are conducted. These include the notion of a model, which serves as an approximation of the real-world structure. A model’s reliability hinges on its ability to accurately represent the physical characteristics and loading conditions of the structure in question. Additionally, concepts such as boundary conditions and loads are crucial, as they define how external forces interact with the structure. Understanding the role of these elements is vital, as they directly influence the outcome of any simulation.
Some basic concepts also involve:
- Discretization: This process involves breaking down a continuous structure into smaller, manageable elements, which can be analyzed separately.
- Mesh Generation: Refers to the creation of a mesh, which determines how the elements are connected and influences the accuracy of results.
- Loading Scenarios: Different loading scenarios must be modeled to see how the structure performs under various conditions, such as weight, wind, or seismic activity.
Mathematical Framework
The mathematical framework in structural simulation is central for understanding and predicting structural behavior. Various mathematical techniques, including differential equations and linear algebra, are utilized to describe the physical behavior of materials and structures. A critical aspect is the use of finite element methods, which transform continuous structural equations into a system that can be solved numerically. This mathematical approach allows engineers to simulate real-world conditions efficiently.
Key components of this framework include:
- Equilibrium Equations: These balance forces and moments within a structure, ensuring stability.
- Constitutive Models: This aspect defines how materials will deform under stress, providing essential insight into material behavior.
- Boundary Conditions: They are necessary for solving mathematical equations and ensuring that simulations reflect realistic physical constraints.
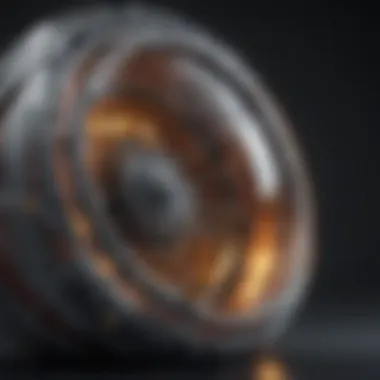
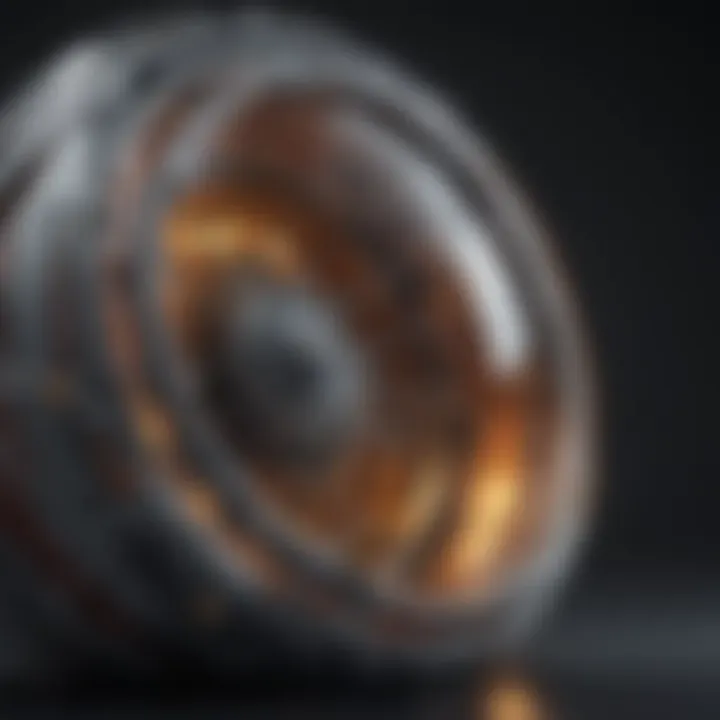
Material Properties and Behavior
Understanding material properties and their behavior under various conditions is paramount in structural simulation. Materials respond differently to stress and strain, so accurate characterization is essential for the reliability of simulations. Factors such as elasticity, plasticity, and viscosity determine how materials react under load. Engineers must select appropriate models for material behavior to ensure accurate predictions of how structures will perform over time.
Important considerations include:
- Elastic Modulus: This property indicates the material's stiffness and affects how it deforms under stress.
- Yield Strength: Understanding the yield strength can help predict when a material will deform permanently.
- Fatigue Limit: This property is critical in assessing how repeated loading affects material longevity.
In structural simulation, an in-depth understanding of these factors is crucial for enhancing the accuracy and reliability of results, ultimately guiding effective design and engineering practices.
"The integration of fundamental principles into structural simulation is essential for robust design and analysis. The accuracy of simulation relies heavily on understanding basic concepts, mathematical frameworks, and material behaviors."
By grasping these essential principles, engineers and designers can significantly improve the outcomes of their simulations, leading to better-informed decisions in the design process.
Types of Structural Simulation
Understanding the various types of structural simulation is crucial. Each type offers distinct benefits and considerations, which can significantly influence both the analysis process and the overall outcomes of engineering projects. This section will explore three prominent categories of structural simulation: static versus dynamic simulation, linear versus nonlinear models, and deterministic versus probabilistic approaches.
Static vs. Dynamic Simulation
Static simulation deals with structures that are assumed to be unchanging over time. In this analysis, loads are applied slowly and remain constant through the period of examination. The primary goal is to determine how a structure responds under these static loads, focusing on displacements, stresses, and potential failure points. One of the main advantages of static analysis is its simplicity. It usually requires less computational power, making it accessible for simpler structures.
Dynamic simulation, on the other hand, encompasses structures subject to changing forces or motions. This type of analysis is critical for applications involving impacts, vibrations, or seismic loads. It requires more complex algorithms and a deeper understanding of material behavior under time-varying conditions. Dynamic analysis enables engineers to assess not just the final state of a structure but how it behaves over time, providing insights into safety and performance under realistic conditions.
Linear vs. Nonlinear Models
Linear models operate under the assumption that material behavior is directly proportional to the applied loads. This means that the stress-strain relationship remains consistent. Linear analysis is generally favored due to its straightforwardness and computational efficiency. However, it can be insufficient for materials or structures that experience large deformations, where behavior deviates from proportionality.
In contrast, nonlinear models account for behaviors such as material yielding, buckling, or large displacements. These models are essential for accurately representing real-world scenarios. Despite requiring greater computational resources, they provide a more comprehensive understanding of structural behavior, particularly in complex applications. Nonlinear analysis is pivotal in assessing structures under extreme conditions or failures, ensuring higher reliability in designs.
Deterministic vs. Probabilistic Approaches
Deterministic approaches assume that the parameters used in the analysis are fixed and known. This method simplifies models and is frequently used when materials and loads are predictable. However, this methodology can overlook real-world uncertainties that may affect structural performance.
Probabilistic approaches, conversely, factor in uncertainties by treating variables such as material properties and loads as random variables. This method provides more comprehensive risk assessments and can help engineers understand the likelihood of various outcomes. Ultimately, probabilistic models can lead to more resilient designs and improved safety measures.
"Understanding the types of structural simulation is essential in achieving optimal design and analysis outcomes. Each type contributes to a rounded comprehension of how structures behave under different conditions."
Using the appropriate type of structural simulation enhances decision-making processes. It leads to better design and maintenance of structures while ensuring safety and efficiency.
Simulation Techniques and Tools
Simulation techniques and tools are foundational elements within the broader scope of structural simulation. They are integral to various engineering disciplines, providing the methods and technologies required for accurate modeling and analysis. Understanding these tools is essential for students, researchers, and professionals, as they enhance the efficiency and effectiveness of design and analysis processes.
Finite Element Analysis (FEA)
Finite Element Analysis is a powerful computational technique that breaks down complex structures into smaller, simpler parts known as finite elements. Each element is examined under various conditions, allowing engineers to predict how materials will react to external forces, changes in temperature, and other environmental factors.
The importance of FEA lies in its ability to provide detailed insights into stress distribution, deformation, and dynamic behavior of structures. It is widely used in fields such as automotive and aerospace engineering to optimize design, improve safety, and reduce material costs. Moreover, the flexibility of FEA allows it to be applied to both linear and nonlinear analysis, making it versatile for a range of applications.
Computational Fluid Dynamics (CFD)
Computational Fluid Dynamics focuses on analyzing fluid flow, heat transfer, and associated phenomena. This technique uses numerical methods to solve the equations governing fluid motion. CFD is crucial in scenarios where fluid interacts with solid structures, such as in the design of aircraft wings, automotive bodies, and even in biomedical applications like prosthetics.
By simulating fluid flow, engineers can identify potential issues such as turbulence and pressure drops. This helps in optimizing designs for performance and efficiency. CFD enables engineers to visualize flow patterns, which is paramount when evaluating aerodynamic properties or cooling performance in complex systems.
Multibody Dynamics (MBD)
Multibody Dynamics is the study of mechanical systems that involve interconnected bodies in motion. This technique allows for the simulation of complex interactions between moving parts, which is especially important in fields such as robotics and automotive engineering. With MBD, engineers can predict how assemblies will behave under different conditions, which aids in design and safety assessments.
Implementing MBD provides insights into the dynamic behavior of mechanisms, allowing for adjustments early in the design process. This can significantly reduce the risk of errors and enhance overall product reliability.
Software Solutions
The advancement of technology has led to the development of sophisticated software solutions that facilitate structural simulation. Tools such as ANSYS, Abaqus, and SolidWorks Simulation are prominent in the industry. These platforms provide comprehensive environments where users can perform FEA, CFD, and MBD—all within the same ecosystem.
Choosing the right software solution is critical as it directly affects the accuracy and efficiency of simulations. Considerations include the type of analysis required, user interface, computational power, and support for various materials and geometrical configurations. Ultimately, leveraging the right tools can lead to better design decisions and streamline the simulation process.
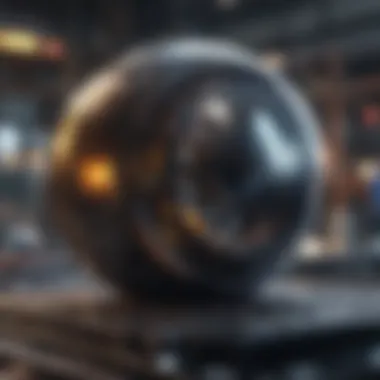
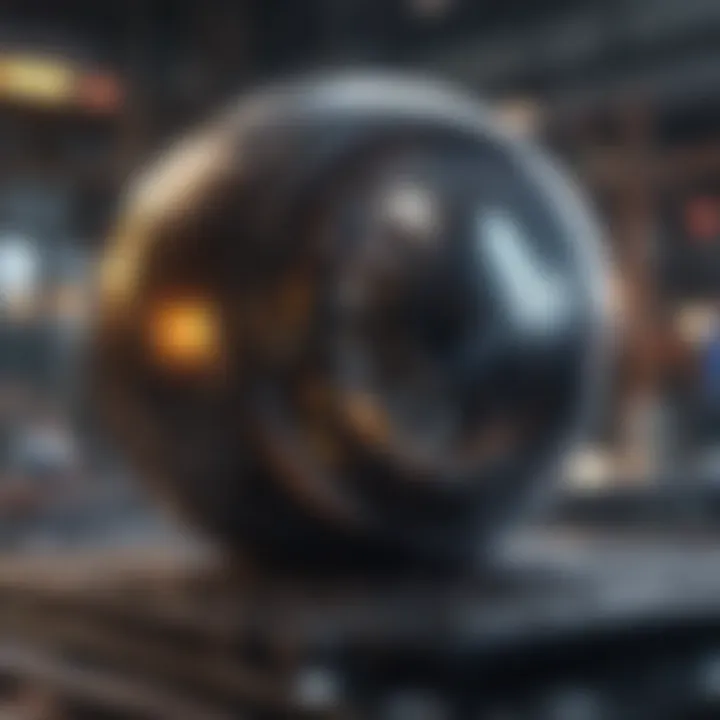
"Effective simulation techniques can significantly shorten the design cycle while improving the quality and safety of engineering outcomes."
In summary, understanding simulation techniques and tools is pivotal for anyone involved in structural simulation. These methods not only facilitate deeper insights into material behavior and structural integrity but also promote innovation and optimization across various engineering disciplines.
Applications of Structural Simulation
Structural simulation is a pivotal framework in various engineering fields. It facilitates the analysis and prediction of structural responses to different forces and conditions. The importance of this topic cannot be overstated, as it influences the design, safety, and efficiency of structures and systems across multiple industries. By employing structural simulation, engineers can avoid costly errors, optimize material usage, and enhance performance under expected loads.
Civil Engineering
In civil engineering, structural simulation plays a crucial role in the design and assessment of infrastructure projects. The ability to simulate how buildings, bridges, and other structures behave under various conditions is vital. Engineers use these simulations to evaluate factors like load distribution, stability, and potential failure points.
For example, during an earthquake, simulations help predict how a building will respond to seismic forces. This information is key to designing structures that adhere to safety standards and withstand such events. Additionally, simulations can also assist in retrofitting existing structures to improve their resilience against future disasters.
Mechanical Engineering
Mechanical engineering heavily relies on structural simulation for the analysis of mechanical components and systems. Here, simulations are used to predict how parts behave under stress, temperature variations, and operational loads. For example, when designing a new engine, engineers can simulate the thermal and mechanical stresses the engine components will endure during operation.
This approach not only shortens the design cycle but also leads to more reliable products. By understanding how components interact under various conditions, manufacturers can optimize designs, reduce weight, and improve fuel efficiency. This is increasingly important in sectors such as automotive and aerospace, where performance and reliability are paramount.
Aerospace Engineering
In aerospace engineering, the stakes are exceptionally high. Structural simulation is essential for analyzing the integrity of aircraft and spacecraft. Engineers simulate different flight conditions to ensure that the structure can withstand forces like turbulence, vibration, and atmospheric pressure changes.
Moreover, advanced simulations enable testing of composite materials often used in aerospace applications. By simulating these materials’ performance, engineers can enhance the safety and efficiency of modern aircraft and space vehicles while minimizing weight, leading to better fuel efficiency.
Biomedical Applications
The application of structural simulation in biomedical fields is increasingly relevant. In this domain, it is used to model biological systems and medical devices, such as prosthetics and implants. For instance, simulations can predict how a prosthetic limb will function in real life, considering factors like movement, weight, and user interaction.
By assessing these factors through simulation, engineers can improve design and functionality, leading to better patient outcomes. Furthermore, simulations in biomedical engineering also extend to studying tissue behavior under load, which is vital for surgical planning and implant development.
"Simulation is not just a tool; it's a means to innovate and ensure safety in engineering."
This exploration of applications demonstrates how integral effective simulation is for developing safer, more efficient systems across industries.
Challenges in Structural Simulation
Structural simulation plays a crucial role in various engineering fields. However, it does not come without its set of challenges. Understanding these challenges is vital for improving methodologies and results in structural simulations. This section will delve into complexities, data limitations, and computational resource demands encountered in the field.
Modeling Complexity
Modeling complexity is one of the foremost challenges in structural simulation. Real-world structures exhibit intricate behaviors that are difficult to replicate in simulations. The interactions between various components, environmental factors, and material properties add layers of complexity. For example, in civil engineering, modeling how wind affects a skyscraper is not just about the building alone; it includes assessing material vibrancy, weight distribution, and external loads.
Moreover, there are different methods for creating models, such as finite element methods and boundary element methods. Each method has its own limitations and requires different assumptions and computational effort. The challenge often lies in choosing the right modeling technique that accurately reflects the actual conditions while balancing computational resources and time constraints.
Inaccuracies in the model can lead to significant errors in predictive outcomes. This makes it essential to validate models through comparison with experimental data or realized behaviors of structures. Therefore, a careful balance must be maintained between complexity, computational feasibility, and accuracy.
Data Limitations
Data limitations present another significant hurdle in structural simulation. Accurate simulations rely on high-quality data, including material properties, environmental conditions, and geographical information. Often, engineers may not have access to detailed or up-to-date data, leading to less reliable simulations.
For instance, material properties such as yield strength may vary due to manufacturing defects or irregularities in material composition. If these variations are not known or captured in simulations, the results may be misleading. Furthermore, external factors such as seismic activity or temperature fluctuations need robust data for precise modeling. In cases where data is scarce, engineers must use approximations, which may compromise the integrity of the simulation.
Data governance also plays a role. As structures become more complex, the amount of data generated and required increases. Without a strong data strategy or management framework, interpreting and using this data becomes cumbersome, leading to inefficiencies.
Computational Resources
The demands for computational resources in structural simulation are continuously increasing with advancements in simulation technologies. As models become more complex, they require more computational power for processing. This can lead to significant challenges in both cost and time.
High-performance computing (HPC) systems can provide the necessary processing capabilities. However, this comes at a significant cost. Many smaller companies or academic institutions may struggle with access to these advanced computational resources, limiting their ability to conduct high-quality structural simulations.
Additionally, as the need for real-time simulations grows, the performance demands on computing resources intensify even further. Engineers are finding it increasingly important to optimize simulations through parallel processing and improved algorithms to manage resources effectively.
Future Directions in Structural Simulation
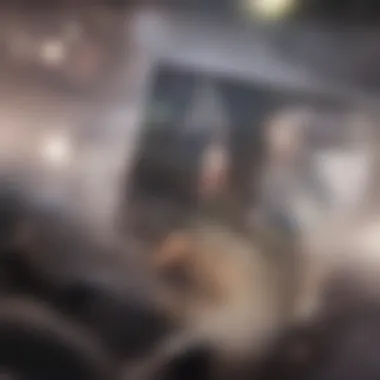
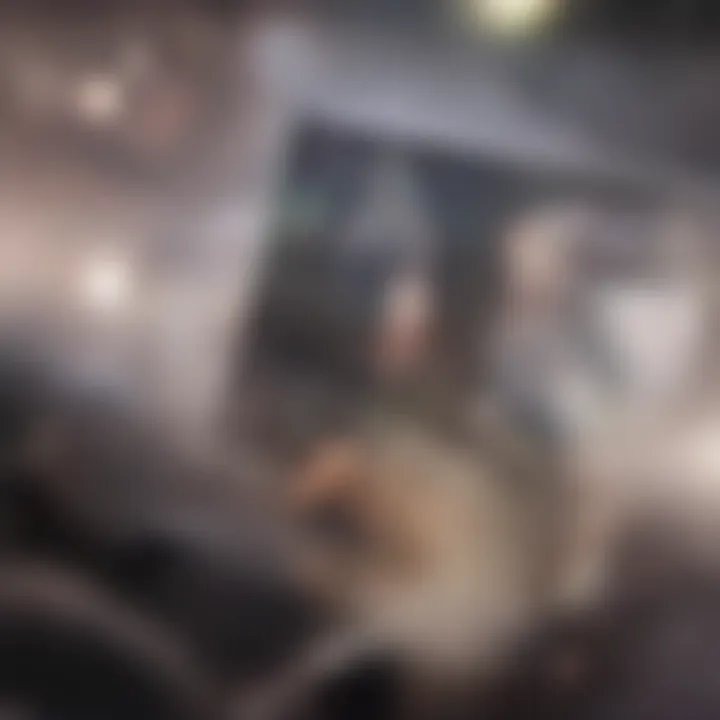
Future directions in structural simulation are crucial for understanding how engineering and design will evolve. This section highlights several specific aspects of this topic. As technology advances, the integration of new methods will reshape how structural systems are analyzed, designed, and maintained.
Emerging Technologies
Emerging technologies play a pivotal role in advancing structural simulation methodologies. Innovations such as additive manufacturing, smart materials, and internet of things (IoT) devices are changing conventional practices. These technologies allow for more precise modeling and can improve real-world applications, like load-bearing capabilities and material efficiency.
For instance, 3D printing enables the creation of complex structures that were previously difficult or impossible to produce. This aspect can lead to customized designs tailored to specific load conditions, making structural elements stronger and more efficient. On the IoT side, sensors embedded within structures can provide real-time feedback on stress, strain, and environmental conditions. This information is invaluable for predicting failures before they occur.
Integration with Machine Learning
Integrating machine learning into structural simulation is an essential capability for future advancements. Machine learning algorithms can analyze vast datasets that traditional methods may not effectively handle. They excel at identifying patterns in material behavior under various conditions.
By using predictive modeling, engineers can enhance accuracy in simulations. This approach can potentially reduce the time and cost in both design and maintenance stages. For example, machine learning can facilitate failure prediction, allowing engineers to take preventive measures based on data rather than reliance on past experiences alone. This shift enhances the decision-making process and provides a quantitative basis for crucial project aspects.
Advancements in Real-Time Simulation
Real-time simulation represents a significant advancement in structural analysis. This capability allows for simulations to be performed continuously as conditions change. For example, in construction, real-time simulations can help monitor stress responses of buildings under dynamic influences such as earthquakes or heavy loads.
This approach can dramatically enhance a project’s safety and reliability. Real-time data integration leads to improved responsiveness to unforeseen issues. Employing technologies such as AR (augmented reality) can also help visualize structural performance in real environments, enhancing practical applications for engineers and architects alike.
"The future of structural simulation lies in the blending of innovative technology with traditional principles, leading to increased accuracy, efficiency, and safety in design and analysis."
Case Studies Highlighting Structural Simulation
The subsection on case studies provides a concrete context for understanding the theoretical aspects of structural simulation. Through specific examples, it becomes easier to appreciate the value of simulation in real-world applications. These case studies reveal not just the methodologies used but also their outcomes, allowing professionals to evaluate effectiveness. Studying these scenarios can offer insight into best practices and potential pitfalls that can arise in various fields of engineering. Here, we will explore three significant case studies that highlight the utility of structural simulation across multiple domains.
Infrastructure Projects
Infrastructure projects are a quintessential domain where structural simulation plays a vital role. The design and maintenance of bridges, roads, and buildings require robust predictive analyses to anticipate structural failures and ensure safety. For instance, consider the simulation conducted for the Golden Gate Bridge, which utilized finite element analysis to predict how it would perform under various loading conditions, including extreme weather events.
By simulating real-world stresses, engineers were able to make informed decisions regarding maintenance schedules and material reinforcements. This proactive approach not only extended the lifespan of the structure but also minimized potential risks, showcasing the benefits of simulation.
"Simulating real-world stresses allows engineers to make informed decisions regarding maintenance and fabric choice."
The integration of simulation into infrastructure design fosters an environment where potential issues can be addressed before they become problems, thereby ensuring public safety and optimizing resource allocation.
Automotive Safety Analysis
Structural simulation is crucial in the automotive industry, especially concerning safety analysis. The example of crash testing through simulation demonstrates how virtual environments can replace expensive and time-consuming physical tests. Companies like Toyota utilize advanced simulation software to model vehicle responses in crash scenarios. This allows them to evaluate the effectiveness of safety features like airbags and crumple zones.
Using simulations enables quicker iterations in design and testing, leading to safer vehicles without the same financial burden as traditional crash tests. Moreover, crash simulations can be conducted under multiple variables, providing a comprehensive overview of safety performance across different conditions.
This strategic application of structural simulation maximizes safety while minimizing overall costs in vehicle development, showing its importance in the automotive field.
Aerospace Component Testing
In aerospace engineering, structural simulation is indispensable due to the high stakes involved. The development of aircraft components involves rigorous testing to ensure structural integrity under extreme conditions. For example, Boeing employs computational fluid dynamics to model the effects of aerodynamic forces on aircraft wings.
These simulations enable engineers to assess how various design choices affect performance and durability. The ability to test remotely through simulations reduces time and resource expenditure, while also enhancing the reliability of critical components in flight.
By utilizing structural simulation, aerospace engineers can introduce innovations faster, enhancing overall safety and performance in increasingly complex designs.
Epilogue
The conclusion serves as a vital synthesis of the insights gathered throughout the exploration of structural simulation. This section encapsulates the overarching themes, emphasizing how integral structural simulation is in today's engineering landscape. It reinforces the notion that effective simulation leads to a deeper understanding of structural behavior, ultimately influencing engineering design and ensuring safety across various applications.
In reflecting on the summary of findings, one recognizes the multifaceted nature of structural simulation. This article highlights the significance of balancing theoretical models with practical applications. It demonstrates how diverse methodologies, such as Finite Element Analysis and Computational Fluid Dynamics, coexist within the collective framework, aiding engineers from civil to aerospace disciplines. The adaptability of structural simulation to different scenarios reinforces its essential role in predictive modeling.
Summary of Findings
Throughout this article, several key points emerged regarding the utility and effectiveness of structural simulation:
- Structural simulation can predict how structures respond under various conditions, which informs design choices.
- Different types of simulation techniques provide varied insights. For example, static simulations focus on stability, while dynamic simulations assess real-time responses under loads.
- The integration of new technologies, especially machine learning, enhances predictive capabilities and optimizes results, pushing the boundaries of traditional methods.
- Case studies showcased practical applications, such as automotive safety analysis, reinforcing how simulation data translates to real-world solutions.
These elements not only underscore the importance of structural simulation but also serve as a testament to its evolving nature.
Implications for Future Research
Future research in structural simulation reveals several avenues for exploration and enhancement:
- Emerging technologies such as AI and automation are poised to disrupt traditional methodologies. Investigating their roles could yield more efficient frameworks.
- There is a need for improved computational models that reflect increasingly complex material properties and behaviors. Studies could focus on creating more resilient structures by understanding their interaction with varying environmental conditions.
- Integration with big data analytics presents an opportunity to refine simulation accuracy. Future research may explore how vast datasets from historical simulations can inform predictive modeling.
- Collaborations across disciplines can lead to innovative uses of simulation in unexpected fields, expanding its reach beyond engineering.
The pathway forward in structural simulation is not only about refining existing techniques but also about embracing innovation and adaptability. As research progresses, the goal remains clear: to enhance understanding and manipulation of structural dynamics, shaping the future landscape of engineering.