Exploring EDS Dip Powder: Composition and Applications
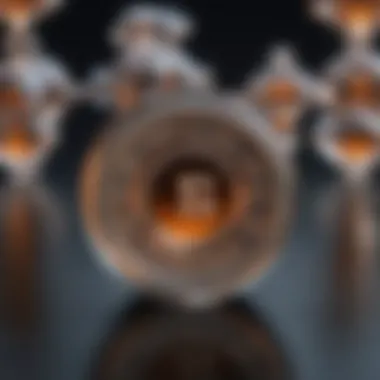
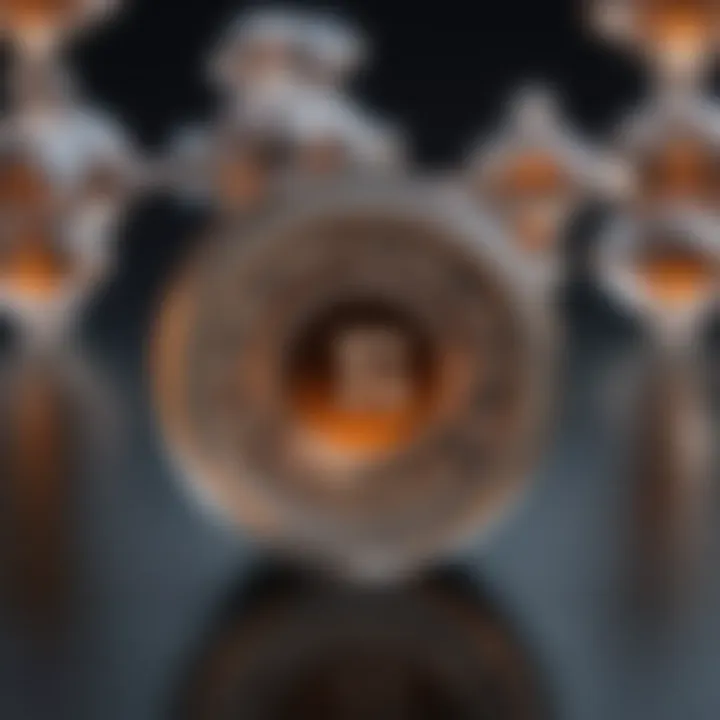
Intro
The exploration of EDS dip powder forms a vital aspect within the evolving field of materials science. While many coating techniques exist, EDS dip powder emerges as a unique approach characterized by its distinctive chemical composition and a variety of practical applications. As industries continuously pursue enhanced performance characteristics, the demand for innovative materials like EDS dip powder grows. The following sections will provide an in-depth examination, highlighting key characteristics, applications, and foreseeable directions which can guide future research initiatives.
Background and Context
Overview of the Research Topic
EDS dip powder is reasonably novel, yet its implications in several industries cannot be overlooked. It primarily consists of fine powder coatings that are applied through an electrostatic process, allowing for superior adherence to various substrates. The dip coating method provides uniform coverage, minimizing defects often associated with traditional coating processes. A precise understanding of its composition is essential to harnessing its full potential in practical applications.
Historical Significance
The development of dip powder coatings has roots tracing back several decades, with advancements in polymer technologies propelling significant growth. As the market for high-performing materials expanded, EDS dip powder gained traction due to its effectiveness in various functions, from protective coatings to decorative surfaces. The evolution of materials science has seen a shift towards sustainable practices, and the adoption of EDS dip powder represents a move towards greener alternatives to conventional coatings. Its historical development reveals both challenges and milestones that contribute to its current application landscape.
Key Findings and Discussion
Major Results of the Study
The investigation of EDS dip powder shows distinct advantages over alternative methods. Key findings indicate:
- Enhanced adhesion properties, ensuring longer-lasting results.
- A wider array of substrate compatibility, including metals, plastics, and ceramics.
- Environmental benefits due to reduced volatile organic compounds in formulations.
These results underline the efficacy of EDS dip powder in meeting rigorous industry standards. By optimizing the powder formulation, researchers have also contributed to improvements in mechanical strength and durability.
Detailed Analysis of Findings
A close inspection of the chemical composition reveals a blend of polymers, pigments, and proprietary additives which play critical roles in the performance of the coating. Each element within the formula can be tailored to suit specific requirementsโfrom hardness and flexibility to resistance to chemicals and abrasion. The functional optimization can result in a wide spectrum of applications, bridging gaps between industries.
Comparative analysis with other coating techniques, such as liquid paint, highlights significant advantages in both application efficiency and overall lifecycle impact. For example, while liquid coatings often necessitate additional layers and drying processes, EDS dip powder allows for a single-layer application that cures rapidly, reducing production time.
"The future of EDS dip powder lies in its adaptability to meet evolving industry demands and sustainable practices."
In addressing the challenges surrounding EDS dip powder, it's crucial to investigate maintenance and recycling processes. Ensuring longevity and sustainability of these coatings is essential for future market viability. Innovations in this aspect will likely shape the trajectory of EDS dip powder in multiple sectors.
In summary, EDS dip powder presents a versatile option for a variety of applications, from automotive to aerospace. Solidifying its role in materials science will require ongoing investigation and refinement, informing practices across industries. The forthcoming sections will delve deeper into specific applications and future directions, further illustrating the material's relevance in modern technology.
Intro to EDS Dip Powder
Understanding EDS dip powder is essential in materials science. This section provides a foundation for exploring its chemical composition, various applications, and future possibilities. EDS dip powder has unique properties that make it beneficial across various industries. By examining its significance, we can grasp not only its practical uses but also its potential for further innovation, addressing current market needs and environmental concerns.
What is EDS Dip Powder?
EDS dip powder refers to a specialized type of powder used primarily in coating applications. It involves the process of submerging a substrate in a powder and subsequently curing it to form a durable finish. The formulation typically consists of resins, pigments, and additives that empower the powder to adhere effectively to various surfaces. The technology behind EDS dip powder has evolved, showcasing its versatility in different sectors, such as automotive and aerospace.
Historical Context
The development of EDS dip powder can be traced back to advancements in coating technologies. Initially, liquid coatings dominated the market; however, as the demand for more durable and efficient materials arose, researchers began to explore dry powder coatings. EDS dip powder emerged as a response to the limitations of its predecessors by offering improved efficiency, reduced waste, and enhanced performance. This historical evolution reflects a trend toward innovation in material applications, emphasizing the need to adapt and improve existing technologies.
Relevance in Modern Science
In today's fast-paced industrial environment, the relevance of EDS dip powder cannot be overstated. Its properties present a valuable alternative to traditional coating methods. With increasing regulations surrounding environmental impact, EDS dip powder offers a solution, as it typically utilizes fewer volatile organic compounds (VOCs). Furthermore, ongoing research is revealing new applications in different fields including construction, electronics, and consumer goods. This adaptability underscores the material's importance in driving forward materials science, highlighting both current and future trends.
Chemical Composition of EDS Dip Powder
The chemical composition of EDS dip powder is pivotal in defining its performance and applications. Understanding the specific ingredients and their roles provides insights into how this material achieves its desirable properties. This section will analyze the main ingredients used in EDS dip powder, elucidate the various additives involved, and highlight the resultant material properties.
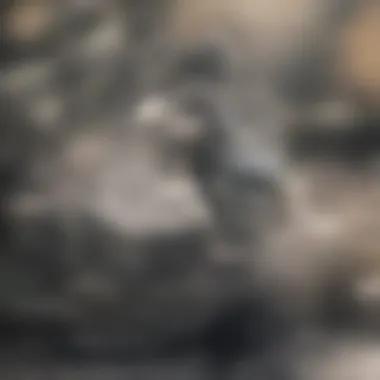
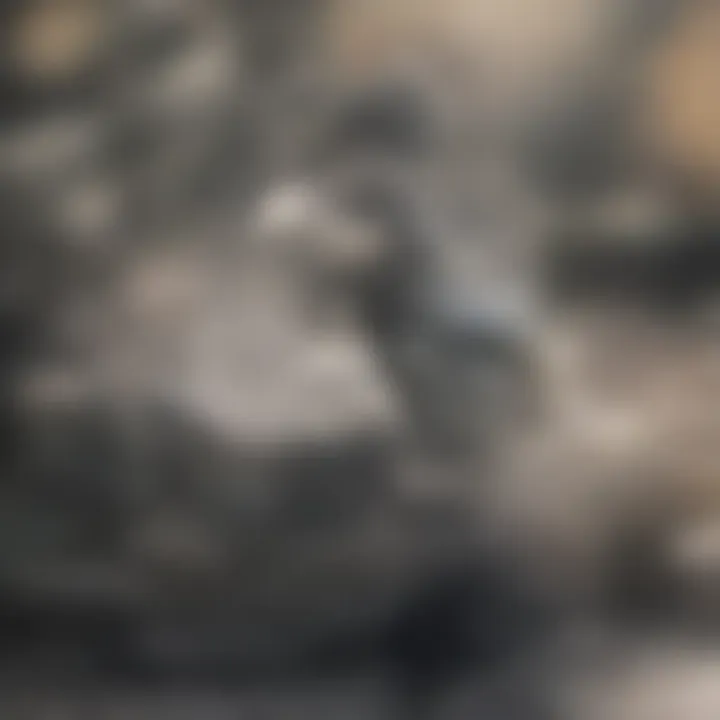
Main Ingredients
EDS dip powder consists primarily of several key components that contribute to its functionality. The main ingredients include:
- Thermosetting Resins: Often, epoxy resins are used due to their thermal stability and adhesive properties. They ensure strong bonding to the substrate.
- Fillers: Fillers such as talc or silica play a significant role in adjusting the viscosity of the powder. They enhance mechanical strength and reduce costs.
- Colorants: Various pigments are incorporated for aesthetic purposes. They allow for customization of the finished product to meet specific design needs.
- Curing Agents: These agents facilitate the hardening process of the dip powder. Common curing agents used are amines and anhydrides, which play a vital role in achieving the desired hardness and chemical resistance.
The selection of these ingredients directly influences the efficiency and effectiveness of the application. The correct combination tailored to specific applications ensures optimal performance.
Additives and Their Functions
Additives serve essential roles in enhancing the properties of EDS dip powder. These substances modify the base material for improved performance. Some common additives include:
- Modifiers: Such as plasticizers which increase flexibility and impact resistance. These help in adapting the material for different environmental conditions.
- Stabilizers: To prevent degradation during storage or application. Such additives help maintain the integrity of the product over time.
- Flame Retardants: These additives are critical in applications where fire resistance is necessary. They diminish the risk of ignition and slow the spread of flames.
Each of these additives is selected based on the requirements of the final application. They play a crucial role in extending the lifespan and enhancing the characteristics of EDS dip powder.
Material Properties
The properties of EDS dip powder are a direct result of its unique chemical composition. Some significant material properties include:
- Adhesion: The ability to bond strongly to substrates determines the overall effectiveness of the coating. Strong adhesion minimizes the risk of delamination.
- Thermal Stability: EDS dip powder maintains structural integrity under high temperatures, making it suitable for various applications in different environments.
- Chemical Resistance: The formulation of EDS dip powder often results in exceptional resistance to chemicals. This is particularly important in industrial applications where exposure to solvents and acids may occur.
- Mechanical Properties: Hardness and impact resistance are crucial for products subjected to physical stress. The appropriate composite structure ensures longevity and durability.
Overall, the chemical composition of EDS dip powder is critical to its success. Understanding and optimizing these ingredients and their interactions allows developers to enhance performance for diverse applications.
Application Processes of EDS Dip Powder
Application processes for EDS dip powder are critical as they dictate the effectiveness and quality of the coating. Understanding these processes not only assists in achieving a superior finish but also helps in optimizing performance characteristics suitable for various applications. This section will explore the specific steps involved in preparing the substrate, various dipping techniques, and the curing processes that follow.
Preparation of the Substrate
Proper substrate preparation is non-negotiable for successful EDS dip powder application. The substrate must be clean, dry and free of contaminants. This prerequisite ensures strong adhesion between the substrate and the dip powder. Often, mechanical or chemical cleaning processes are utilized to achieve the desired level of cleanliness. Additionally, surface roughening may be employed to enhance the bonding surface. Without these preparations, even the highest quality dip powders may fail to perform satisfactorily, undermining their protective and aesthetic qualities.
Dipping Techniques
Dipping techniques play a significant role in determining the final characteristics of the powder coating. Three primary methods are widely used: Conventional Dipping, Vacuum Dipping, and Automated Systems.
Conventional Dipping
Conventional dipping involves immersing the substrate directly into a powder bath. This method is straightforward, which makes it a popular choice. One major characteristic of conventional dipping is its simplicity and ease of use. It allows for a consistent layer of material, which is essential in many applications. However, the manual nature of this technique can lead to inconsistencies. For instance, operator skill can significantly influence results, leading to variable coating thickness.
Vacuum Dipping
Vacuum dipping is an advanced technique that involves drawing a vacuum while dipping the substrate. This method enhances the penetration of powder into intricate designs and cavities of the substrate. The key advantage of vacuum dipping is its capability to create a uniform coating even on complex geometries, which is often a challenge with traditional methods. Moreover, it reduces the risk of air bubbles, which can compromise the integrity of the coating. Nonetheless, this technique can be more expensive due to the required equipment.
Automated Systems
Automated systems have risen in popularity due to their efficiency and accuracy. These systems often make use of robotic arms to dip substrates with precision control over the process. The key feature is the reduced chance of human error while increasing production rates. Automated systems often deliver higher repeatability, ensuring that each item receives a consistent powder layer. However, initial investment costs and setup complexity can be barriers for smaller operations.
Curing Processes Explained
Once the dipping technique is completed, curing becomes vital. Curing allows the powder to bond and solidify, ensuring durability and performance. This process typically involves heat treatment, where the coated substrate is heated in an oven. The heat activates specific chemical compounds in the powder, leading to a hard and resilient finish. The specifics of the curing process can vary, impacting the characteristics of the final product. Knowledge of these processes is necessary to ensure that EDS dip powder applications meet the required standards in various industries.
Advantages of EDS Dip Powder
The application of EDS dip powder presents several key advantages that enhance its appeal in various industrial settings. Understanding these benefits is essential for researchers and professionals alike, as they can influence material choice for specific applications. EDS dip powder is characterized by three significant elements: durability and longevity, versatility in application, and economic considerations.
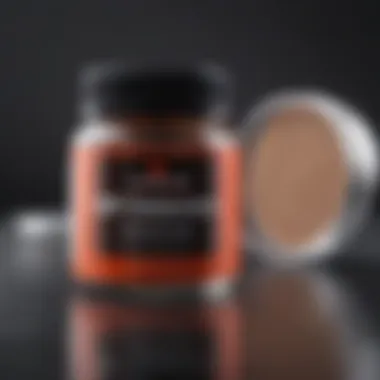
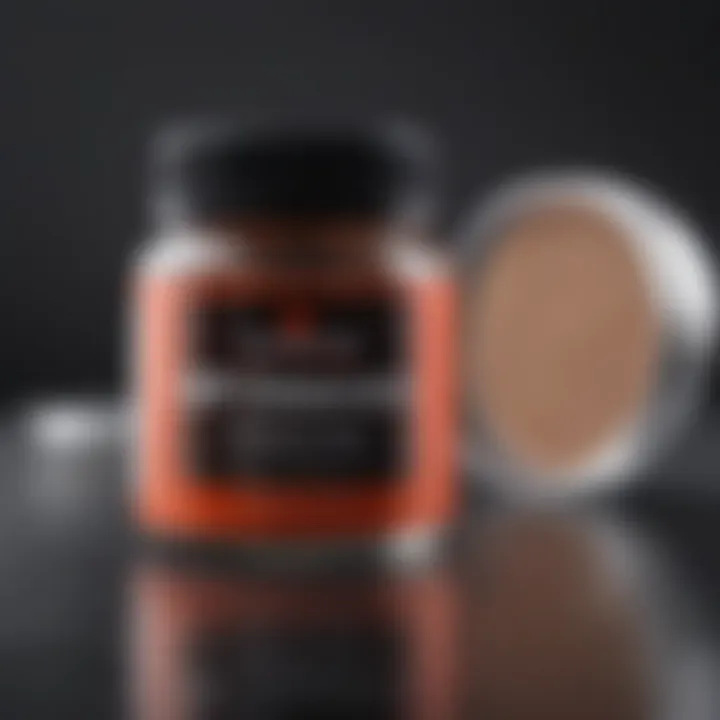
Durability and Longevity
EDS dip powder systems are known for their exceptional durability. This durability arises from the chemical makeup, which contributes to strong bond integrity once cured. The powder coating can withstand harsh environmental conditions, including extreme temperatures and exposure to corrosive substances. This resistance is particularly advantageous for industries such as automotive and aerospace, where components often face extreme stresses.
Moreover, the longevity of EDS dip powder applications reduces maintenance costs over time. As the coatings resist chipping, scratching, and fading, they keep surfaces looking new longer, thereby enhancing the product's overall lifecycle. This aspect can be crucial when considering the long-term value of materials used in manufacturing processes or protective coatings.
Versatility in Application
Another notable advantage of EDS dip powder is its versatility across diverse application scenarios. The system can be applied to various substrates, including metals, plastics, and wood, making it suitable for a wide range of industries. This adaptability makes it a favored option for manufacturers who require coatings that can easily transition between different products and use cases.
The application techniques are also diverse. From conventional dipping methods to more advanced automated systems, the flexibility allows businesses to scale production as needed. Details like thickness and finish can also be adjusted to meet specific requirements, enhancing the overall usability of EDS dip powder in different contexts.
Economic Considerations
When evaluating EDS dip powder's advantages, economic factors play a vital role. The initial investment in equipment and setup is often offset by long-term savings. Due to its durability and low maintenance requirements, businesses experience fewer reparations and replacements over the coating's lifespan. Additionally, the efficient application processes can lead to lower labor costs, making it an economically favorable choice in the long run.
Comparatively, the coatings can also enhance the aesthetic appeal of products, leading to better consumer perception and potentially higher sales. By providing protection with attractive finishes, manufacturers can differentiate their products in competitive markets.
"The blend of performance and cost-effectiveness positions EDS dip powder as a leading choice in modern coatings."
Comparative Analysis with Other Coatings
A comparative analysis with other coatings is essential to understand the unique attributes and applications of EDS dip powder. This section elucidates how EDS dip powder performs in relation to other modalities like liquid and spray coatings. Such comparisons are not just academic; they have practical implications for industries seeking optimal solutions for various applications. By dissecting the differences in performance, cost-efficiency, and environmental impact, one can gauge the effectiveness of EDS dip powder in real-world scenarios.
EDS Dip Powder vs. Liquid Coatings
When comparing EDS dip powder to liquid coatings, several key differentiators emerge. Liquid coatings often rely on solvents that can evaporate during application, which raises environmental and health concerns. In contrast, EDS dip powder is generally solvent-free and presents a safer alternative in terms of emissions. Moreover, EDS dip powder facilitates a thicker application layer in a single pass, which can enhance durability.
Another point of consideration is the curing process. Liquid coatings may necessitate intricate drying times and conditions, while EDS dip powder simplifies this through heat curing methods that can provide rapid results. This means that production lines can operate more efficiently with EDS dip powder.
Additionally, EDS dip powder demonstrates superior resistance to corrosion and adverse weather conditions when evaluated under similar usage scenarios. As a result, for industries operating in harsher environments, dip powder might offer better longevity and reduced maintenance costs.
EDS Dip Powder vs. Spray Coatings
The comparison between EDS dip powder and spray coatings reveals different strengths and weaknesses. Spray coatings offer flexibility and can cover complex geometries more easily than EDS dip powder. However, they often produce more overspray, leading to material waste and potential environmental issues. EDS dip powder, being an application with a controlled process, minimizes material waste.
In terms of thickness, dip powder results in a more uniform layer across surfaces, reducing the risk of imperfections that are sometimes associated with spray applications. This uniformity is essential for maintaining the aesthetic and functional qualities of the finished product.
Moreover, the solid composition of EDS dip powder can enhance the mechanical properties of the coating. It is often more resilient against impacts and scratches compared to spray coatings, which can lose their integrity over time.
Performance Metrics Comparison
A direct performance metrics comparison enhances the understanding of EDS dip powder's capabilities. Key metrics to consider include:
- Adhesion Strength: EDS dip powder generally exhibits superior adhesion to substrates compared to both liquid and spray coatings.
- Thickness Uniformity: Achieved with greater consistency using dip powder, which can reduce defects.
- Chemical Resistance: EDS dip powder often performs better when exposed to corrosive chemicals and environmental elements.
- Durability: Performance testing usually shows that EDS dip powder-coated parts maintain their properties longer than those treated with liquid or spray coatings.
In summary, evaluating EDS dip powder against other coating types brings to light its advantages and shortcomings. This knowledge is vital for selecting the appropriate coating for specific applications, ensuring that industries can make informed decisions that align with their operational needs.
Challenges and Limitations of EDS Dip Powder
The assessment of EDS dip powder inevitably brings forward its challenges and limitations. Understanding these aspects is crucial for researchers and professionals in materials science. Every innovation, including EDS dip powder, has constraints that can impact its practicality and effectiveness. By examining these challenges, we can identify areas for improvement and innovation.
Application Limitations
EDS dip powder applications come with specific limitations that are vital to acknowledge. One significant limitation is the need for consistent substrate quality. If the surface of the material being coated is not prepped properly, the adhesion of the dip powder may suffer, leading to coating failures. The surface should be free from contaminants such as oil, dust, or rust, requiring additional pre-treatment steps, which can increase operational costs.
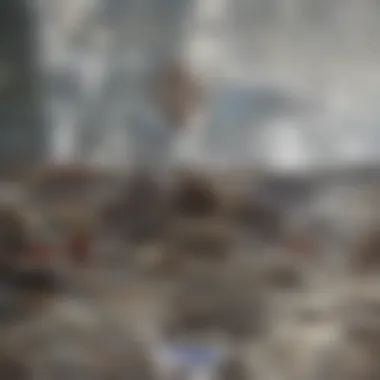
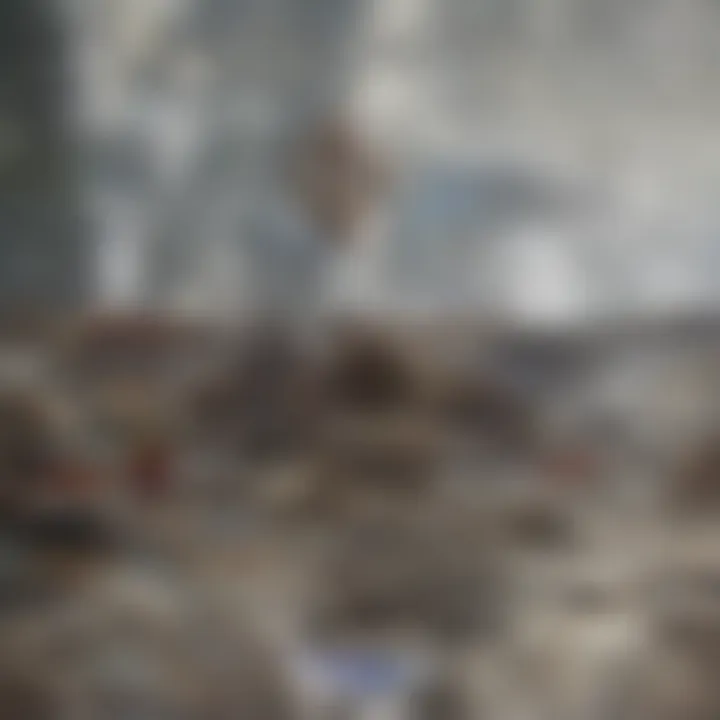
Moreover, EDS dip powder is not suitable for all materials. Its efficacy diminishes when applied to surfaces that have complex geometries or intricate designs. These factors can hinder access during the dipping process, which could create uneven coatings. In addition, it has limitations regarding thickness; EDS coatings can be difficult to achieve in very thin layers, which can be a requirement for specific applications.
Environmental Concerns
The environmental impact of EDS dip powder is a topic of growing concern. The production and disposal of chemical components used in the dip powder can lead to negative environmental effects. Some additives or solvents might be harmful if released into the ecosystem. Specific compounds, such as those found in traditional coatings, have generated regulatory scrutiny, impacting the manufacturing processes.
Additionally, the energy consumption involved in curing processes can contribute to a carbon footprint that industries are increasingly being pressured to minimize. Thus, developing more sustainable practices is essential. Research in biodegradable additives or environmentally-friendly curing agents could address these concerns in the future.
Quality Control Issues
Quality control is an ongoing challenge within the context of EDS dip powder usage. Variability during the production of dip powder batches can lead to inconsistencies in performance. Every batch may display differences in chemical composition or physical properties, making standardization difficult. This inconsistency can affect the reliability of the coating process.
Furthermore, the implementation of strict quality control measures requires additional resources and investment. Regular testing for adhesion, hardness, and other mechanical properties becomes necessary to ensure performance expectations are met. Insufficient testing could result in failures in field applications, leading to increased costs due to reapplication or repairs.
Addressing the challenges associated with EDS dip powder is essential for maximizing its potential in advanced materials applications.
Future Directions and Research Areas
Research on EDS dip powder is rapidly evolving, reflecting its significance and versatility in multiple fields. A thorough understanding of the future directions pertaining to this material is vital. It facilitates advancement not just in applications but also in addressing some of the existing limitations. This section discusses essential aspects such as innovation in material science, emerging technologies, and sustainability initiatives that will shape the landscape of EDS dip powder.
Innovation in Material Science
Innovation in material science is crucial for the development of new EDS dip powder formulations. As industries demand higher performance standards, researchers must address challenges through innovative approaches. One promising avenue is the integration of nanomaterials into the dip powder matrix. These materials can enhance properties like adhesion, durability, and resistance to environmental factors.
Additionally, modifying the chemical formulation of the dip powder can lead to significant improvements. For instance, the inclusion of reactive additives can enhance cross-linking during curing processes, resulting in stronger coatings. The exploration of bio-based and biodegradable materials is also gaining traction. These approaches can lead to eco-friendlier products, aligning with growing environmental consciousness across industries.
Emerging Technologies
Emerging technologies hold the potential to revolutionize the application and effectiveness of EDS dip powder. For instance, advancements in automated dipping systems can streamline the application process. By utilizing robotics and sophisticated control systems, manufacturers can achieve more consistent coating quality while reducing waste.
Furthermore, the adoption of advanced curing techniques, such as ultraviolet (UV) curing, is another area of ongoing research. UV curing offers rapid processing times and enhanced material properties, making it a compelling alternative to traditional thermal curing methods. Engaging with technologies like augmented reality (AR) for training and application optimization could also enhance user understanding and operational efficiency.
Sustainability Initiatives
In recent years, sustainability has become a pivotal driver for research and development in materials science. EDS dip powder's future must align with these initiatives to minimize environmental impact. Efforts to incorporate recyclable and renewable materials into the dip powder formulation are essential steps forward.
A focus on reducing volatile organic compounds (VOCs) in the dip powder can significantly mitigate environmental risks associated with its use. Researchers are already investigating alternative solvents and binders that maintain performance while being less harmful to the environment.
"Sustainability is not just an option but a necessity for the future of materials, including EDS dip powder."
Moreover, promoting closed-loop systems in the manufacturing and application processes can reduce waste significantly. Initiatives focusing on recycling used dip powder or repurposing waste material can contribute to a more sustainable production cycle.
The End
The conclusion of the article serves several pivotal functions. It synthesizes the various elements discussed in detail throughout the piece, reinforcing the significance of EDS dip powder in the realm of materials science. By summarizing key insights, this section not only wraps up the findings but also signifies the impact these findings have on current practices and future explorations in the field.
In terms of benefits, the conclusion highlights how EDS dip powder stands as a valuable asset in industries that demand high-performance materials. It integrates an understanding of its chemical composition, application techniques, and advantages over alternative coatings. For practitioners, the conclusion emphasizes practical applications which can lead to strategic enhancements in production and efficiency. Moreover, the challenges presented in the earlier sections offer a nuanced view that is essential for comprehending the limitations and potential areas for research.
This article aims to inform and guide future researchers and engineers, encouraging innovative exploration into EDS dip powder. The complexity of its application and the multilayered nature of its advantages make it a topic worth deeper investigation in upcoming studies, particularly in enhancing sustainability initiatives and integrating emerging technologies.
Summary of Key Insights
The article delves into several essential observations regarding EDS dip powder:
- Chemical Formula: The unique blend within EDS dip powder distinguishes it from traditional coatings, aiding in superior adhesion and durability.
- Application Techniques: Employing various methodologies such as vacuum dipping, this material can cater to diverse industrial needs, enhancing its versatility.
- Comparative Metrics: EDS dip powder exhibits commendable performance against liquid and spray coatings, making it a robust choice for many applications.
- Challenges: Understanding the limitations regarding environmental impacts and application efficacy provides a well-rounded perspective for potential users.
These insights lay the foundation for further discussions on innovation and sustainability, positioning EDS dip powder as a significant figure in the future landscape of material science.
Final Thoughts on EDS Dip Powder
As we contemplate EDS dip powder's trajectory, it is important to recognize its position at the intersection of performance and sustainability. The applications of this innovative material extend beyond mere surface coating; it represents a broader scope in the advancement of material formulations.
In closing, the evolving landscape of materials science would benefit greatly from continued exploration of EDS dip powder. The integration of new technologies combined with a commitment toward sustainable practices could yield products that not only perform effectively but also reduce environmental impact. Thus, for students, researchers, and professionals, EDS dip powder remains a fertile ground for exploration and innovation. The discussion presented in this article serves to ignite curiosity and inspire further inquiry into a material that is both promising and impactful.