Electrolytic Polishing: Process and Industrial Uses
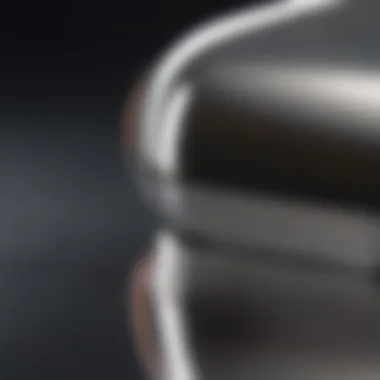
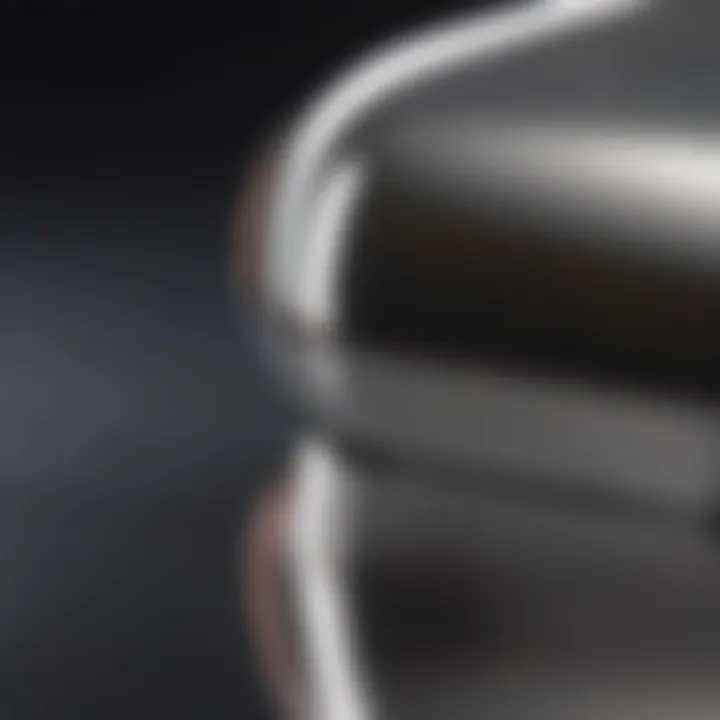
Intro
Electrolytic polishing is a method that improves the surface finish of metal parts through an electrochemical process. This technique is beneficial in various sectors, including aerospace, medical devices, and food processing. With increasing demands for high-quality surfaces, understanding electrolytic polishing becomes vital for those involved in manufacturing and research.
This article aims to provide a detailed exploration of the electrolytic polishing process, its historical context, and its practical applications. It will also discuss the benefits and limits of this method and compare it with other polishing techniques, offering a broad perspective on its significance today.
Background and Context
Overview of the Research Topic
Electrolytic polishing, also known as electrochemical polishing, enhances the surface finish of metals by using a direct current to remove a thin layer of material from the workpiece. During this process, the workpiece is submerged in an electrolyte solution. The metal surface reacts, allowing for the dissolution of microscopic high points on the surface. This results in a smoother finish.
This technique is particularly useful for materials like stainless steel, aluminum, and titanium, which are often used in critical applications. The need for a refined surface is often driven by requirements for cleanliness, corrosion resistance, and aesthetic appeal.
Historical Significance
Historically, polishing methods primarily relied on mechanical means. However, as manufacturing processes evolved, the need for advanced techniques became apparent. Electrolytic polishing has its roots in the early 20th century. It gained popularity during the post-World War II period, especially in industries such as aerospace and medical devices, where precision and surface integrity are paramount. The advancement of materials science and the development of sophisticated equipment have played crucial roles in popularizing this method.
Key Findings and Discussion
Major Results of the Study
Research highlights that electrolytic polishing significantly enhances surface characteristics. Test results show improvements in surface roughness parameters and reductions in contamination on polished items. Additionally, materials that undergo electrolytic polishing demonstrate higher resistance to corrosion and stress corrosion cracking.
Detailed Analysis of Findings
Further analysis reveals that the success of electrolytic polishing is largely contingent on factors such as current density, temperature, and the composition of the electrolyte solution. For instance, using phosphoric acid and sulfuric acid in the electrolyte allows for efficient removal of material while minimizing excessive etching.
- Key Parameters in Electrolytic Polishing:
- Current Density: Influences the rate of polishing.
- Temperature: Affects viscosity and reaction kinetics.
- Electrolyte Composition: Determines the speed and quality of polishing.
In summary, electrolytic polishing represents a prominent method for achieving high-quality surface finishes, delivering control over surface properties critical in today’s advanced manufacturing environments.
"Understanding the variables influencing the electrolytic process is essential for optimizing outcomes in various applications."
This process stands as an effective alternative to traditional polishing techniques, showcasing both precision and cleanliness. As emphasis on quality and efficiency grows, so too will the interest in methodologies like electrolytic polishing.
Intro to Electrolytic Polishing
Electrolytic polishing has gained prominence in various sectors where metal finishing is crucial. It is not just about aesthetics; the process enhances component longevity and functionality. The relevance of electrolytic polishing is evident in its ability to yield superior surface quality. This aspect is particularly important in industries such as medical, aerospace, and food processing, where cleanliness and precision are paramount.
Definition of Electrolytic Polishing
Electrolytic polishing, often referred to as electrochemical polishing, is a process that removes material from the surface of a workpiece through anodic dissolution in an electrolyte solution. This technique usually involves the immersion of the metal item into an electrolytic cell. When an electric current is applied, metal ions detach from the surface, resulting in a smooth and shiny finish. The process is fundamentally different from mechanical polishing, which relies on abrasion. Instead, it achieves a level of smoothness that can be challenging to reach with traditional methods.
Importance in Metal Finishing
The importance of electrolytic polishing in metal finishing can be summarized in a few key points:
- Surface Quality: The process minimizes scratches, pits, and other surface imperfections, leading to a consistently smooth finish.
- Corrosion Resistance: By removing surface contaminants and creating a uniform microstructure, electrolytic polishing significantly enhances the corrosion resistance of metals. This is vital in environments that expose metals to aggressive chemicals or moisture.
- Ease of Cleaning: Smooth surfaces are easier to clean and maintain, which is especially beneficial in sanitary applications, such as food processing equipment and surgical instruments.
- Reduced Friction: The smooth finish achieved through this method decreases friction when parts interact, promoting longer lifespan and better performance in applications like automotive and aerospace components.
In summary, electrolytic polishing is not merely about achieving visual appeal; it's an essential technique that improves functionality and durability in various industrial applications.
The Chemistry Behind Electrolytic Polishing
The chemistry behind electrolytic polishing is crucial for understanding how this process achieves superior surface finishes on metal components. Grasping the underlying electrochemical principles can inform the optimization of the procedure, leading to enhanced quality and efficiency. By recognizing the behaviors of materials and reactions involved, industries can better tailor techniques to their specific needs, ensuring reliability and performance of products.
Electrochemical Reactions
At the core of electrolytic polishing are electrochemical reactions occurring at the anode and cathode. During polishing, the workpiece acts as the anode and undergoes oxidation. As electric current passes through the electrolyte solution, the metal surface is selectively dissolved. This results in a smoother finish as the higher points on the surface are removed preferentially. The reactions not only improve the surface quality but also play a crucial role in controlling the material removal rates. Understanding these reactions allows for precise adjustments in polishing parameters, making it essential for effective application across different metals and alloys.
Role of Electrolytes
Electrolytes serve as the medium that permits conductivity in electrolytic polishing. Commonly, solutions may include acids like sulfuric acid or phosphoric acid, which enhance the dissolution of metal ions from the surface. The choice of electrolyte affects current efficiency and, subsequently, the quality of the polished surface. For example, acidic solutions might yield brighter finishes compared to neutral or basic electrolytes. Additionally, the concentration and temperature of these solutions can influence the overall efficiency of the process, stressing their importance in achieving the desired results.
Current Density and Voltage Effects
Current density and voltage are key parameters in electrolytic polishing that directly impact the overall process. Current density refers to the current per unit area on the workpiece. High current densities can lead to quicker material removal but may also cause overheating or uneven polishing. Conversely, lower densities tend to produce finer finishes but at slower rates. Voltage, on the other hand, contributes to the speed of the electrochemical reactions. A balance must be struck between achieving an efficient process and maintaining quality. Hence, empirical studies often guide the optimization of these parameters to reflect specific objectives in polishing and desired surface characteristics.
In summary, the chemistry surrounding electrolytic polishing encompasses electrochemical reactions, the role of electrolytes, and the influence of current density and voltage. These elements intertwine to exemplify the sophistication and precision required in this refining process. Understanding these components not only improves practical applications but also contributes to ongoing advancements within the field.
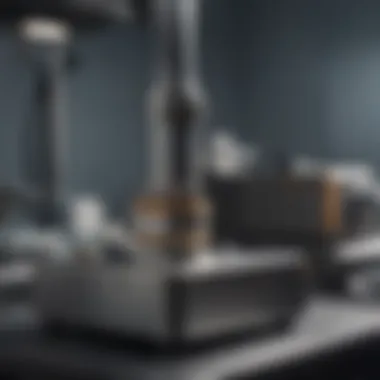
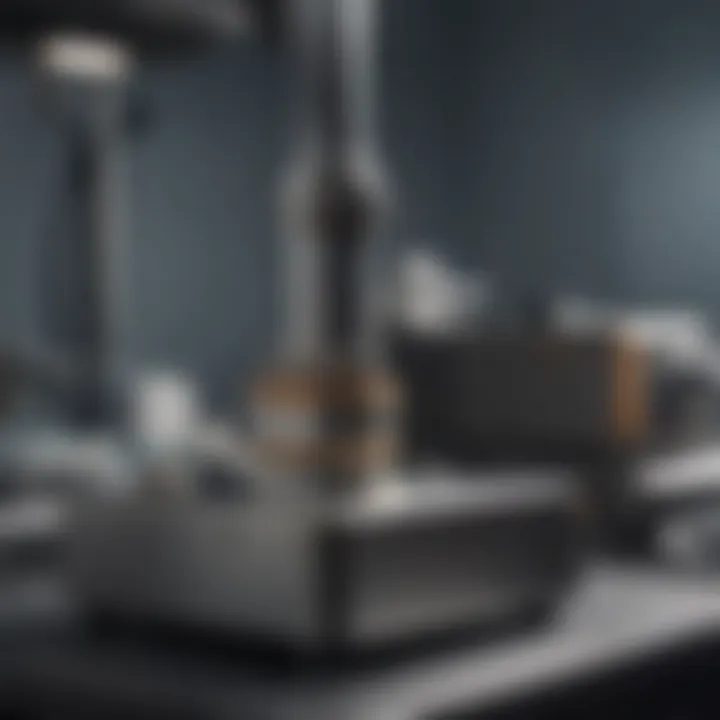
Equipment Used in Electrolytic Polishing
Electrolytic polishing requires specialized equipment to achieve optimal results. This section will cover the different components involved, emphasizing their roles and significance in the polishing process. Proper understanding of this equipment is crucial for efficient operation and superior surface quality.
Electrolytic Cells
Electrolytic cells are the heart of the electrolytic polishing process. They provide the medium in which metal ions are removed from the surface of the workpiece. The design of these cells can vary, but they generally consist of an electrolyte solution, an anode, and the workpiece as a cathode.
These cells facilitate electrochemical reactions. Here, the workpiece is immersed in a conductive electrolyte solution. An electrical current passes through the solution, leading to the dissolution of material from the surface of the workpiece. The choice of electrolyte is important, as it must be compatible with the metal being polished. Certain electrolytes, like sulfuric acid or phosphoric acid, are commonly used due to their effective ion transport properties.
The efficiency of the electrolytic cell directly affects the polishing quality. A well-designed cell ensures uniform current distribution, which leads to consistent polishing results across the surface of the workpiece.
Power Supplies
Power supplies are another vital component in the electrolytic polishing setup. They provide the necessary electrical current to the electrolytic cells. Factors such as voltage and current density are critical in determining the polishing effectiveness.
An ideal power supply will allow for precise control over these parameters, which can significantly influence the polishing outcome. For instance, higher voltage may lead to faster polishing, but if too high, it can cause damage to the workpiece. Conversely, lower voltage leads to slower polishing but can ensure a more controlled process.
These supplies can be adjustable to cater to the specific needs of different metals and surface finishes. Therefore, investing in a high-quality power supply is crucial for consistent results in electrolytic polishing.
Protective Gear
Safety is a key consideration when engaging in electrolytic polishing due to the use of hazardous chemicals and electrical equipment. Protective gear is essential to mitigate health risks during the process.
Important protective gear includes:
- Gloves: Protect hands from harmful electrolytes.
- Goggles: Shield eyes from splashes.
- Face Shields: Provide additional face protection.
- Aprons or Lab Coats: Keep personal clothing free from chemicals.
In addition to personal protective equipment, utilizing proper ventilation in the work area is important. This can help prevent the accumulation of gases that may be released during the polishing process.
Ensuring the use of protective gear not only safeguards the operators but also fosters a better environment for carrying out the polishing tasks without fear of mishaps.
Effective safety measures during electrolytic polishing cannot be underestimated as they play a crucial role in sustainable practices in industrial settings.
The Electrolytic Polishing Process
The electrolytic polishing process is a crucial component in enhancing the surface finish of metallic workpieces. This method utilizes electrochemical reactions to remove material from the workpiece surface, creating a smooth and reflective finish. It is especially significant in industries where precision and cleanliness are paramount, as seen in medical and aerospace applications. This section explores the preparation involved, the steps taken during polishing, and the subsequent treatments that can enhance the final product's quality.
Preparation of Workpieces
Before initiating electrolytic polishing, preparing the workpiece is essential. This preparation phase determines the efficiency of the polishing process and the quality of the final surface finish. The workpieces must be thoroughly cleaned to remove any contaminants, including oils, dust, or oxidation. Common cleaning methods include ultrasonic cleaning, rinsing with suitable solvents, and using alkaline or acidic solutions for more stubborn residue.
It is also necessary to inspect workpieces for defects or irregularities before polishing. Uneven surfaces can affect the polishing effectiveness and may lead to insufficient finish quality. In some cases, initial machining processes may need to be performed to achieve a more uniform base surface before electrolytic polishing. This preparation ensures that the subsequent steps yield the best possible results in terms of surface smoothness and finish quality.
Polishing Steps
The actual polishing process consists of several meticulously timed steps that involve immersion of the workpieces into an electrolytic solution within the electrolytic cell. The setup generally includes a cathode and an anode, where the workpiece acts as the anode.
- Electrolytic Solution Selection: The choice of electrolyte is paramount. Commonly used solutions are made from phosphoric acid, sulfuric acid, or mixtures suited for specific metals.
- Current Control: Current density needs to be precisely managed to ensure an even removal of the surface material. A higher current density means faster polishing but risks distortion.
- Temperature Management: Maintaining optimal temperature within the electrolytic cell enhances the rate of material removal and helps in achieving a better finish.
- Polishing Duration: The duration of exposure can vary based on the desired finish and the material being polished. Continuous monitoring is essential to prevent over-polishing.
The electrochemical action in this process leads to the dissolution of surface imperfections and irregularities, allowing for a smooth outcome that can be very desirable in applications where aesthetics and function are critical.
Post-Polishing Treatments
After the polishing process, post-polishing treatments are often required to enhance and protect the workpiece's surface. These steps can include:
- Rinsing: A thorough rinse is essential to remove remaining electrolytic solution and any reaction byproducts from the surface of the workpiece.
- Passivation: For materials like stainless steel, passivation can improve corrosion resistance by enhancing the protective oxide layer on the surface.
- Ultrasonic Cleaning: Following polishing, ultrasonic cleaning can be beneficial in dislodging any residual particles that the rinsing may not have cleared.
- Protective Coatings: In some applications, it may be advantageous to apply protective coatings to further enhance corrosion resistance or to achieve specific aesthetic properties.
These subsequent treatments are critical in ensuring the longevity and effectiveness of the polished workpieces, maximizing the benefits achieved through the electrolytic polishing process.
"The careful execution of the polishing process and the associated preparations and post-treatments ultimately dictate the effectiveness of electrolytic polishing."
Applications of Electrolytic Polishing
Electrolytic polishing finds extensive use across various industries due to its ability to enhance the surface properties of metal components. This section elaborates on its importance, focusing on several key applications. The benefits of electrolytic polishing include a smoother surface finish, improved corrosion resistance, and better biocompatibility, which make it especially valuable in specific sectors. Here, we will explore four significant applications: medical instruments, aerospace components, food processing equipment, and automotive parts.
Medical Instruments
In the medical field, instruments require high levels of precision and sterility. Electrolytic polishing significantly improves the surface finish of surgical tools such as scalpels, forceps, and scissors, providing a smoother, cleaner surface. This reduces the areas where bacteria can harbor, thus enhancing the instruments' hygiene. Moreover, the improved corrosion resistance extends the lifespan of medical instruments, making them a cost-effective choice for hospitals and clinics.
"A polished surgical tool not only enhances performance but also ensures higher patient safety."
Aerospace Components
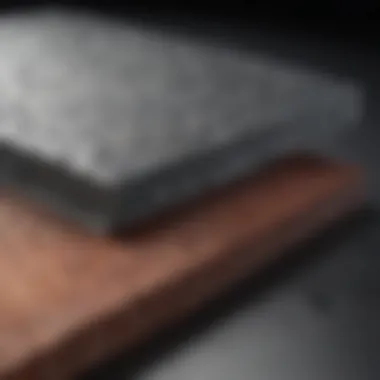
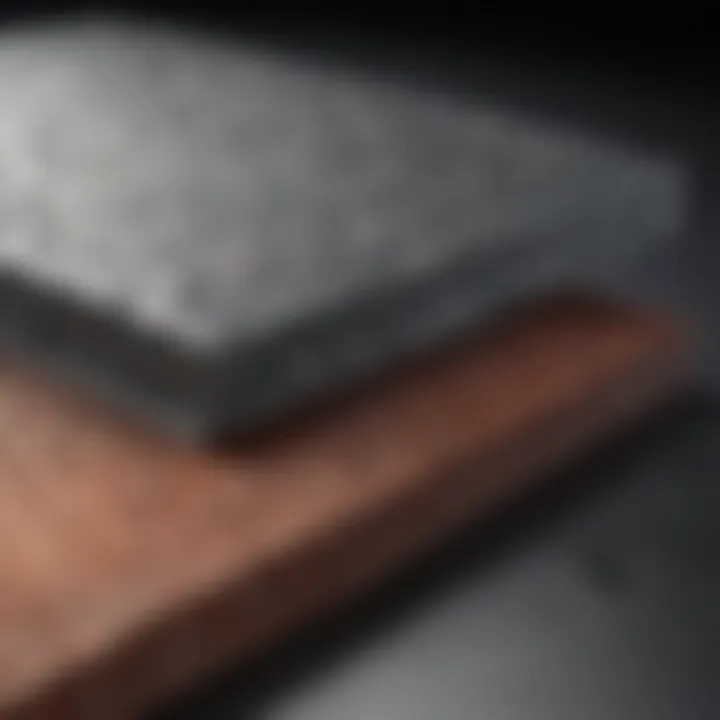
The aerospace industry demands components that are not only lightweight but also highly durable. Electrolytic polishing helps to enhance the surface quality of metals like titanium and aluminum, which are commonly used in aircraft manufacturing. A well-polished component exhibits lower friction and reduced drag, contributing to improved fuel efficiency. Furthermore, the enhanced corrosion resistance of these polished parts safeguards against the harsh environments encountered during flight.
Food Processing Equipment
In food processing, maintaining sanitary conditions is crucial. Equipment used in this industry, such as mixers, conveyors, and storage tanks, must be easy to clean and resistant to corrosion. Electrolytic polishing aids in creating a smooth surface, preventing food particle buildup and facilitating easier cleaning routines. Additionally, the enhanced resistance to corrosion and staining ensures compliance with health and safety regulations, making it an essential process for food industry applications.
Automotive Parts
The automotive sector benefits from electrolytic polishing in several ways. Components like exhaust systems, fuel injectors, and wheels can see significant improvements in their resistance to corrosion when polished electrolytically. This results in longer-lasting parts and better performance. Furthermore, a polished surface can also improve the aesthetic appeal of automotive components, which is a valuable aspect for manufacturers aiming to enhance the consumer experience.
In summary, the applications of electrolytic polishing highlight its critical role in improving the quality, durability, and hygiene of metal components across diverse industries. Its relevance cannot be understated, making it a favored technique in contemporary manufacturing.
Advantages of Electrolytic Polishing
Electrolytic polishing brings significant enhancements to metal finishing, offering a multitude of advantages that can be essential in various applications. This process does not simply improve the appearance of metal surfaces; it also has practical implications for performance and longevity. Understanding these benefits helps professionals and researchers to make informed decisions in their respective fields.
Surface Finish Improvement
The foremost advantage of electrolytic polishing is the impressive enhancement of surface finish. This method produces a smooth and shiny surface with minimal roughness. Unlike traditional mechanical polishing, which often leaves small scratches or marks, electrolytic polishing effectively removes material from the peaks or high points of the metal surface. The end result is a much more refined finish that is not only aesthetic but also functional.
- Precision. Electrolytic polishing can achieve higher levels of precision. It is ideal for applications requiring strict tolerances and uniformity.
- Reflection. The polished surface features improved light reflection, a factor that is vital in applications like optics or surgical instruments.
Enhancement of Corrosion Resistance
Another notable benefit of electrolytic polishing is its capacity to enhance corrosion resistance. The process effectively removes oxides and contaminants from the metal surface, leading to a cleaner and more resistant finish. This is particularly important in environments where metals are exposed to humidity, chemicals, or other corrosive elements.
- Surface Passivation. The polishing process often results in a passivation layer, which acts as a protective barrier against oxidation.
- Longevity. Components that undergo electrolytic polishing typically exhibit longer service life, thus reducing maintenance costs and downtime.
Control Over Polishing Parameters
Electrolytic polishing provides remarkable control over the polishing parameters, which allows for customization based on specific needs. By adjusting variables such as current density, temperature, and time, operators can effectively tailor the process to achieve desired outcomes. This level of control can optimize not only the quality of the finish but also the efficiency of the overall operation.
- Adaptability. Different materials and applications may require different settings. Personalized parameters can result in ideal surface traits without compromising the integrity of the material.
- Consistency. A controlled process minimizes variability, which is crucial for mass production in industrial settings.
Limitations of Electrolytic Polishing
Understanding the limitations of electrolytic polishing is crucial for both practitioners and researchers in the field of metal finishing. There are specific material and cost factors that can impact the effectiveness and applicability of this process. By recognizing these limitations, one can make informed decisions when choosing electrolytic polishing as a metal finishing method.
Material Limitations
Electrolytic polishing is not suitable for every material. This method primarily works best with metals that are conductive and offer good corrosion resistance. Stainless steels, aluminum, and copper alloys are among the most common materials used. However, materials like titanium and certain ceramics can pose challenges. They may not achieve the desired smooth finish due to their unique properties.
For instance, titanium’s high affinity for oxygen can lead to oxidation during the polishing process, resulting in a poor surface finish. Additionally, some materials may corrode or degrade when exposed to the harsh chemicals used in the electrolytic solution. The specific composition of the metal plays a crucial role. A comprehensive understanding of the materials involved is essential to determine if the electrolytic polishing process is feasible.
Cost Factors
Cost considerations are also significant when evaluating electrolytic polishing. The initial investment in equipment, which includes electrolytic cells and power supplies, is substantial. Furthermore, the ongoing costs related to chemicals, maintenance, and energy consumption can accumulate. Companies must weigh these costs against the benefits gained from improved surface finishes and corrosion resistance.
While electrolytic polishing can offer enhanced quality over mechanical or chemical polishing methods, it may not always present a favorable cost-to-benefit ratio for every application. Thus, assessing the financial implications before committing to this process is necessary.
Note: A comprehensive cost analysis specific to the type of operation and volume of work should be undertaken.
In summary, while electrolytic polishing is a valuable method for achieving high-quality finishes, its limitations—particularly regarding suitable materials and cost—should be thoroughly evaluated to ensure effective and efficient application in metal finishing.
Safety Considerations in Electrolytic Polishing
In the field of electrolytic polishing, safety is a paramount concern. The process involves chemicals and equipment that, if not managed properly, can pose significant risks. Understanding the potential hazards and following safety protocols is essential for anyone involved in this work. This section provides a comprehensive overview of the hazards associated with chemical use and the operational safety protocols necessary for safe practice in electrolytic polishing.
Hazards of Chemical Use
Electrolytic polishing utilizes various chemicals that can be hazardous. Common substances include sulfuric acid, phosphoric acid, and chromic acid. These chemicals can cause skin burns, respiratory issues, and eye damage. It is important to be aware of their properties and effects.
The following hazards are often associated with these substances:
- Corrosiveness: Many polishing solutions can cause serious skin burns. Always wear protective gear when handling these materials.
- Toxicity: Inhalation or ingestion of fumes can lead to severe health effects. Proper ventilation is crucial.
- Environmental Concerns: Disposal of chemical waste must adhere to local regulations to prevent environmental contamination.
To mitigate these hazards, proper training on chemical handling and an understanding of Material Safety Data Sheets (MSDS) are crucial.
Operational Safety Protocols
Operational safety protocols are designed to ensure a safe working environment in electrolytic polishing. Here are key protocols to follow:
- Personal Protective Equipment (PPE): Always use gloves, goggles, and aprons. This helps protect against chemical splashes and exposure.
- Ventilation: Work in a well-ventilated area or use fume hoods. This prevents the accumulation of toxic fumes.
- Emergency Procedures: Familiarize yourself with emergency protocols. This includes knowing the location of eyewash stations and emergency showers.
- Chemical Storage: Store chemicals according to recommendations. Keep them in labeled containers and away from incompatible substances.
- Training and Awareness: Regular training on chemical hazards and safety practices can greatly reduce accidents.
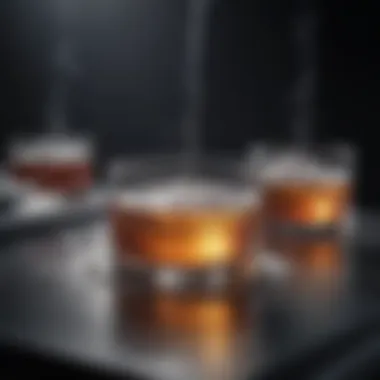
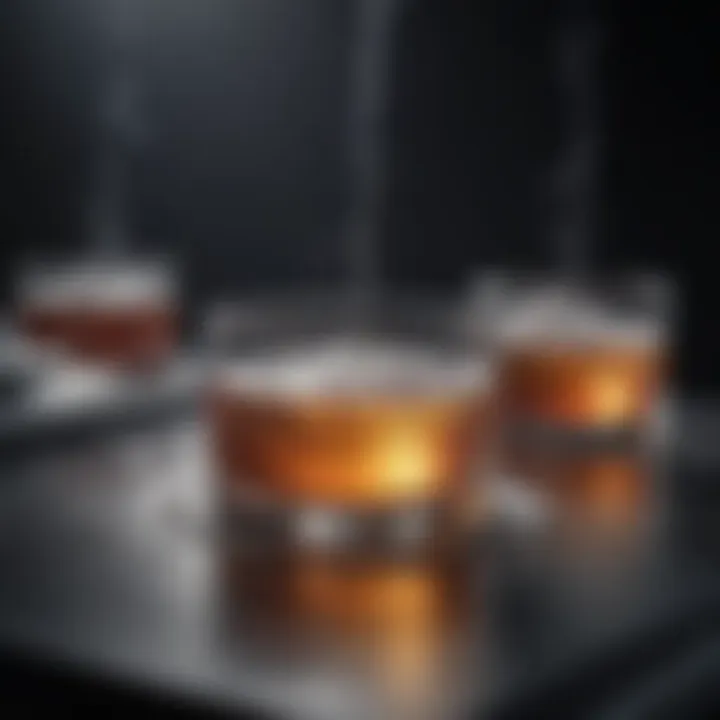
"Safety is not just a priority; it is a part of our responsibility in the workplace."
By adhering to these safety considerations and protocols, individuals can significantly reduce the risks associated with electrolytic polishing, creating a safer working environment for all.
Comparative Analysis: Electrolytic Polishing vs Other Methods
The area of metal finishing incorporates several techniques. Among these, electrolytic polishing is notable due to its precision and efficiency. Comparing electrolytic polishing with other methods is critical for understanding not only its unique advantages but also its limitations. This section evaluates three specific metal finishing techniques: mechanical polishing, chemical polishing, and abrasive blasting. Each method has distinct characteristics, offering different benefits and considerations depending on application requirements.
Mechanical Polishing
Mechanical polishing involves the use of abrasive materials or tools to enhance the surface finish of metal items. This method utilizes different forms of abrasives, including wheels, belts, and pads. The main advantage of mechanical polishing is its ability to achieve significant surface smoothing through direct contact with the workpiece. However, it can be labor-intensive and may lead to uneven surfaces, especially on complex geometries.
Advantages of Mechanical Polishing:
- Cost-effective: Mechanical polishing often requires less initial investment compared to etrolytic processes.
- Accessibility: Equipment for mechanical polishing is widely available and user-friendly.
- Versatility: It is applicable to various materials.
Disadvantages of Mechanical Polishing:
- Surface Integrity: Substantial pressure can induce stress or deformation on the material.
- Finish Quality: Achieving mirror-like finishes may require additional steps.
Chemical Polishing
Chemical polishing employs a chemical solution to remove a thin layer of material from the surface without abrasive action. It tends to provide a high-quality finish and is particularly effective for intricate shapes. This method is beneficial for metals such as stainless steel and aluminum. The interaction between the chemical solution and the workpiece leads to a very polished surface, often minimizing roughness significantly.
Advantages of Chemical Polishing:
- Uniformity: It offers a more consistent surface finish across complex geometries.
- No Surface Damage: There is no risk of micro-scratches or surface defects caused by contact abrasives.
Disadvantages of Chemical Polishing:
- Environmental Concerns: The disposal of chemical waste may pose environmental risks.
- Limited Material Compatibility: Not all metals react favorably to chemical polishing agents.
Abrasive Blasting
Abrasive blasting, also known as sandblasting, involves propelling abrasive particles at high velocity onto the workpiece surface. This method is effective for cleaning, stripping, and preparing materials for coating. It can quickly remove surface contaminants and grants the flexibility to achieve various finish roughness levels. However, the process can be harsh, which may lead to pitting or unnecessary material loss if not controlled properly.
Advantages of Abrasive Blasting:
- Speed: This method can cover large surface areas quickly.
- Surface Preparation: It is helpful for preparing surfaces for additional treatments or coatings.
Disadvantages of Abrasive Blasting:
- Potential Damage: Excessive blasting can lead to substrate damage.
- Dust and Cleanup: This method generates dust and requires appropriate ventilation and cleanup efforts.
Future Trends in Electrolytic Polishing
Electrolytic polishing is an area witnessing constant evolution. The marshaling of new technologies and heightened awareness towards sustainable practices shape its future considerably. Understanding these trends is crucial for stakeholders in various industries. Innovations promise not just efficiency but also responsibility towards the environment.
Technological Innovations
Emerging technologies stand as a cornerstone in the evolution of electrolytic polishing. Key players in the industry are integrating automation and advanced monitoring systems to optimize processes. The use of smart sensors and real-time data analytics enhances precision, leading to improved surface finishes. Automation reduces human error, ensuring consistency in results. Innovations in electrolyte formulations also present significant advancements. These new formulations can allow for faster initial polishing without compromising quality. Machine learning is starting to influence how parameters are adjusted in real-time during the polishing process. This adaptability makes electrolytic polishing more versatile, allowing it to meet various production demands efficiently.
Sustainability Considerations
With increasing focus on environmental stewardship, sustainability in electrolytic polishing is gaining attention. The electroplating process traditionally consumes significant energy and generates waste. The future focuses on reducing these impacts. More manufacturers are opting for biodegradable electrolytes which lower environmental hazards. Recycling processes for waste generated during electrolytic polishing are also being developed, promoting a circular economy approach. Implementing closed-loop systems can drastically minimize water usage while still maintaining effective polishing results.
Additionally, the quest for energy-efficient equipment cannot be overstated. Innovations aimed at reducing energy consumption are key. The shift towards renewable energy sources in powering electrolytic polishing processes aligns closely with global sustainability goals. These considerations not only appeal to eco-conscious consumers but also attract businesses aiming for greener practices.
"The future of electrolytic polishing will rely heavily on technological integrative approaches that harmonize efficiency and sustainability."
In summary, the future trends in electrolytic polishing suggest a realm of opportunities. Technological advancements promise enhanced efficiency, while sustainability initiatives align processes with environmental goals. Stakeholders should stay informed about these trends to foster adaptability and do well in demanding markets.
End
The concluding section of this article emphasizes the multifaceted impact of electrolytic polishing on modern manufacturing practices and its relevance across various industries. Electrolytic polishing is not merely a step in metal finishing; it is a crucial process that influences both the performance and durability of metal components. Its benefits extend beyond aesthetic improvements, providing significant enhancements in functional attributes.
Summation of Key Points
To encapsulate the main insights:
- Electrolytic Polishing Process: This method employs electrochemical reactions to achieve a smooth surface finish. It involves specific steps like preparation, polishing, and post-polishing treatments.
- Applications Across Industries: Industries ranging from healthcare, aerospace, food processing to automotive, leverage this technique for its ability to enhance safety and functionality.
- Advantanges and Limitations: While offering superior surface quality and corrosion resistance, considerations about material limitations and costs remain pertinent.
- Safety Considerations: Adhering to proper safety protocols during the polishing process is essential to mitigate risks associated with chemical use.
- Comparative Analysis: The juxtaposition with alternative polishing methods illustrates its unique advantages in certain applications.
- Future Directions: Technological innovations and sustainability efforts will shape the future landscape of electrolytic polishing.
These points underscore the importance of familiarity with electrolytic polishing methodologies, not just as a practical technique, but as a strategic advantage in various sectors.
Implications for Future Research
The landscape of electrolytic polishing invites continued exploration. Future research should focus on:
- Advancement in Techniques: Innovations aimed at improving efficiency and reducing costs in the electrolytic polishing process could significantly enhance its application. Exploring alternative electrolytes and polishing parameters presents a pathway for breakthroughs.
- Environmental Considerations: Investigating more sustainable practices that align with global environmental efforts can make electrolytic polishing more appealing. Reduction of hazardous waste generated during the process will be a key area of focus.
- Customization: Tailoring electrolytic polishing techniques for specific materials or industries can yield improved outcomes, warranting detailed studies.