3D Printed Dental Implants: Revolutionizing Oral Restoration
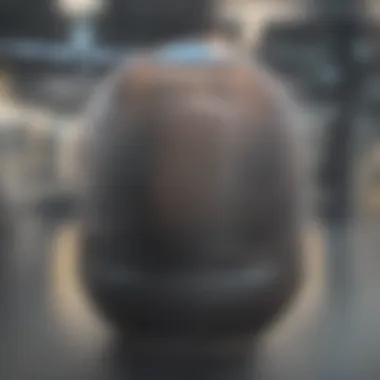
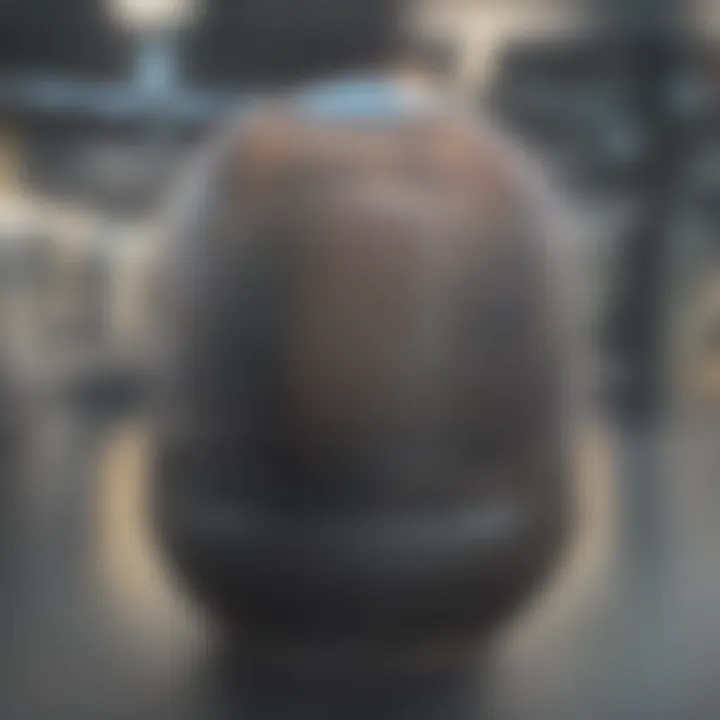
Intro
The realm of dentistry has begun to witness a significant transformation with the advent of 3D printing technology. The ability to create precise, custom dental implants has opened new horizons for oral restoration. This section outlines the growing relevance of this technology in dental practices and its implications for both patients and practitioners alike.
Background and Context
Overview of the Research Topic
3D printing, or additive manufacturing, refers to various processes where material is joined or solidified under computer control to create a three-dimensional object. In the field of dentistry, this technology has emerged as crucial for the development of dental implants, enabling the production of tailored solutions for individual patients.
Historical Significance
Historically, dental implants have relied on traditional manufacturing methods which often led to a one-size-fits-all solution. These procedures were not only time-consuming but also limited in terms of customization. The introduction of 3D printing in this field can be traced back to the early 2010s, with significant advancements made in materials and design techniques since then. Today, the ability to print implants using biocompatible materials significantly enhances surgical success and patient satisfaction.
Key Findings and Discussion
Major Results of the Study
The recent studies demonstrate that 3D printed dental implants can improve healing time and integration with the surrounding bone. Moreover, surveys reveal that patients experience enhanced comfort due to the personalized fit of these implants.
Detailed Analysis of Findings
The materials used in 3D printing are a key factor in the success of these implants. Common materials include titanium and polymer composites, which are known for their biocompatibility and strength. Furthermore, the design process typically begins with a digital scan of the patient’s mouth, allowing for the generation of highly detailed models. These models are then used to create implants that match the exact specifications needed.
"The future of dental implants lies in the hands of advanced technology, fundamentally changing how we approach oral health."
This transformative approach does not come without challenges, however. There are ethical considerations regarding the accessibility of this technology, as well as potential regulatory hurdles that could impede widespread adoption. Nevertheless, the implications for dental practices are profound, offering opportunities for growth and enhanced patient care.
Culmination
As we continue to explore the developments in 3D printed dental implants, it is clear that this technology represents a turning point in oral restoration. With ongoing advancements, the future of dental practices can be expected to become increasingly refined and patient-centered.
Intro to 3D Printing in Dentistry
The integration of 3D printing technology into dentistry signifies a paradigm shift in oral restoration. This section explores the important role of 3D printing in dental applications, focusing on its evolution, advantages, and the considerations surrounding its implementation. The convergence of technology with healthcare has the potential to enhance patient outcomes significantly.
The Historical Context
The inception of dental 3D printing can be traced back to the advent of rapid prototyping technology in the late 20th century. Initially, it was employed for creating models for dental education and planning surgical interventions. However, it did not take long for the dental industry to recognize the benefits of producing actual dental components such as crowns, bridges, and now, implants, using this innovative method.
Historically, dental implants relied heavily on traditional manufacturing techniques that often produced many inconsistencies in fit and quality. The introduction of 3D printing allowed for precise replication of anatomical features, paving the way for better-fitting and aesthetically pleasing implants. As these techniques developed over the years, they became more accessible and affordable for dental practices, thus broadening their application across various clinical scenarios.
Emergence of 3D Printing in Dental Applications
As technology progressed, so too did its applications in dentistry. The emergence of 3D printing has introduced a new era for creating dental implants. Practitioners began to adopt this method not just for its efficiency, but for the customization it offers. Personalized care is vital in dentistry, where the fit and comfort of dental implants can significantly impact patient satisfaction.
The production of 3D printed dental implants involves a digital workflow that commences with imaging techniques like Cone Beam Computed Tomography (CBCT). This imaging creates a comprehensive representation of an individual’s dental structure, which is crucial for developing tailored solutions.
Once the digital model is prepared, it serves as a blueprint for creating the implant using various 3D printing technologies, which allows for rapid prototyping and immediate feedback.
Tackle regulatory standards and biocompatibility to ensure that these innovations are not only effective but also safe for patients. In summary, the emerging use of 3D printing in dentistry marks a significant leap forward, emphasizing the importance of accuracy and personalization in treatment.
Understanding Dental Implants
Understanding dental implants is fundamental to grasping the transformation that 3D printing brings to oral restoration. Dental implants serve as effective solutions for replacing teeth lost due to injury, decay, or other issues. They provide a strong foundation for fixed or removable replacement teeth designed to blend seamlessly with natural teeth. When looking at the integration of 3D printed dental implants, the importance of knowing the types and traditional manufacturing techniques cannot be overstated. This understanding lays the groundwork for discussing precision, customization, and the potential for improved patient outcomes.
Types of Dental Implants
There are several types of dental implants, each designed for specific situations and patient needs. The two primary categories are endosteal and subperiosteal implants.
- Endosteal Implants: These are the most common type. They are surgically placed directly into the jawbone. They come in various shapes, including screws, cylinders, or blades. After healing, a post is attached to the implant, which supports the artificial tooth.
- Subperiosteal Implants: Unlike endosteal implants, these are placed under the gum but above the jawbone. They are less common and typically used for patients who lack adequate bone height for endosteal implants.
Each type has advantages and is considered based on both the health of the patient and their specific dental condition. This understanding helps practitioners make informed decisions for the best restorative procedures.
Traditional Manufacturing Techniques
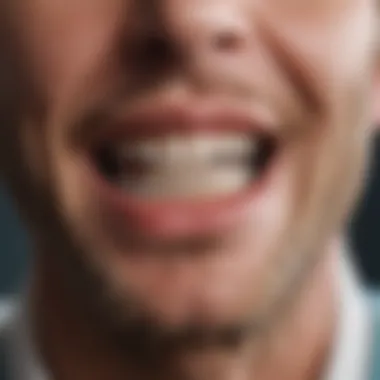
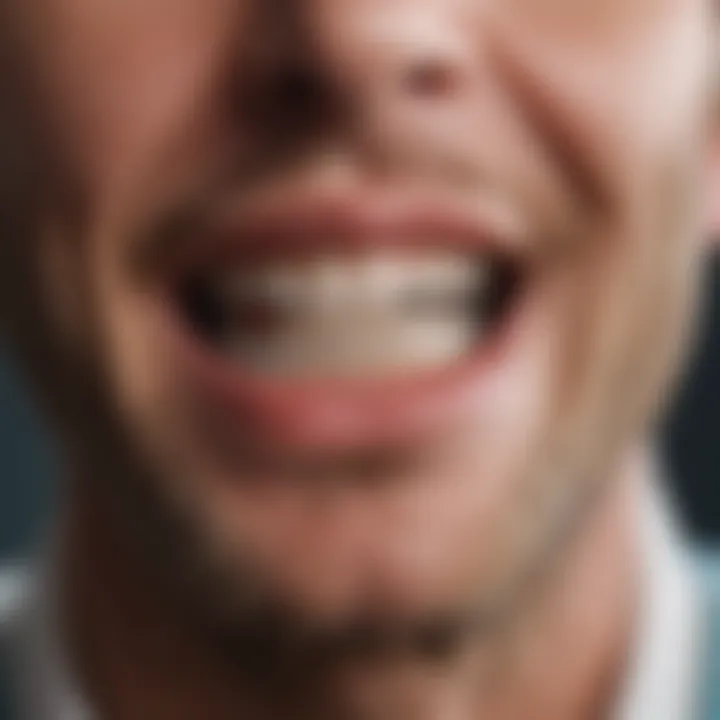
Before 3D printing emerged, traditional methods of creating dental implants involved more labor-intensive processes. Typically, this included casting or machining metal from rods to produce the necessary shapes. Here are some notable methods:
- CNC Milling: This involves using computer-controlled machines to cut and shape materials. It is precise but can result in wasted material and often requires multiple steps before reaching the final product.
- Lost-Wax Casting: In this technique, a wax mold is created and surrounded by a heat-resistant material. Once the mold hardens, the wax is melted away, leaving a cavity that can be filled with metal. This method can be time-consuming and less adaptable to complex shapes.
- Injection Molding: This method allows for creating multiple identical parts quickly, which is beneficial for large-scale production. However, it limits creativity regarding design variations.
Understanding these traditional manufacturing techniques highlights their limitations, such as producing bulk designs without the customization that patients may need. As we transition to discuss 3D printing, it becomes clear that this technology offers substantial improvements in creating customized, precise dental implants tailored to individual patient needs.
3D Printing Technology Explained
The realm of 3D printing technology in dentistry is rapidly evolving. It is crucial for understanding how this innovation shapes dental implants and oral restoration. The technology provides unprecedented levels of customization and efficiency in the fabrication of dental devices. By enabling precision and personalization, 3D printing changes the landscape of restorative dentistry.
This section delves deep into the specific technologies used in crafting 3D printed dental implants, emphasizing their relevance and advantages.
Types of 3D Printing Technologies
Fused Deposition Modeling
Fused Deposition Modeling, or FDM, is a widely-used 3D printing method. Its core operation involves the extrusion of melted thermoplastic filament. This filament is laid down layer by layer to create three-dimensional objects. One key characteristic of FDM is its accessibility; it is often one of the most affordable 3D printing methods available. This aspect makes it a popular choice among dental practitioners who are exploring 3D printing options.
A unique feature of FDM is its versatility in material choice. Various polymers can be utilized to form dental implants, allowing for tailored applications. The advantages include ease of use and relatively low costs. However, the disadvantage lies in the lower mechanical properties compared to other methods.
Selective Laser Sintering
Selective Laser Sintering, SLS, stands out due to its use of a high-powered laser to fuse powdered materials into solid structures. This method allows for the production of complex geometries that may be impossible with other technologies. A significant characteristic of SLS is its ability to work with a variety of materials, including metals and polymers.
SLS presents many advantages, particularly regarding the structural integrity of the created implants. The unique feature of this method is its capacity to produce durable and functional parts, often used in load-bearing dental applications. However, the disadvantages include higher costs and more complex machinery requirements.
Stereolithography
Stereolithography, known as SLA, employs a different approach. It uses ultraviolet light to cure resin into solid forms, layer by layer. The main characteristic of SLA is its ability to create extremely high-resolution parts. This method is notable for fine details and smoother surface finishes, making it suitable for aesthetic applications in dentistry.
The unique feature of Stereolithography is its precision. The advantages of SLA include high accuracy and meticulous details, crucial for dental restorations. One downside is the limited material options available in comparison to other technologies, potentially restricting its applications in certain scenarios.
Materials Used in 3D Printed Dental Implants
Polymers
Polymers are pivotal in the production of 3D printed dental implants. They are lightweight and flexible, making them beneficial for various dental applications. A notable characteristic of polymers is their ability to mimic the elasticity of natural tissues, promoting patient comfort. Their main advantage is the ease of processing and customization. However, there are concerns about durability and wear resistance compared to metals.
Metals
Metals, particularly titanium and alloys, are used primarily for their exceptional strength and biocompatibility. A key aspect of metals is their load-bearing capabilities, which is essential in dental implants. The unique feature of metals in this context is their resistance to corrosion and strength under stress. This makes them a popular choice for long-term solutions. Nonetheless, the disadvantages include higher costs and the complexity of processing.
Ceramics
Ceramics play a significant role in the realm of dental implants as they closely resemble human tooth structure. They are primarily selected for their aesthetic properties and biocompatibility. One of the key characteristics of ceramics is their ability to bond well with bone, promoting better integration. The unique feature of ceramics is their sheer stability and resistance to wear. However, they can also be brittle, posing a risk of fracture under certain conditions.
The Design Process for 3D Printed Dental Implants
The design process for 3D printed dental implants is a crucial component that plays a significant role in ensuring successful outcomes in oral restoration. This process combines advanced technology with clinical insights, allowing dental professionals to create implants that are both functional and tailored to individual patient needs. Implementing effective design strategies in 3D printing can lead to improved patient outcomes, reduced surgery times, and higher degrees of patient satisfaction. Thus, understanding this process is vital for both practitioners and their patients.
Computer-Aided Design (CAD) in Dentistry
Computer-Aided Design, or CAD, has transformed the landscape of dentistry. It allows for the precise modeling of dental implants based on specific anatomical features of a patient's mouth. This technology enables dental professionals to create highly detailed and accurate representations of implants before they are manufactured.
Some critical advantages of using CAD in designing dental implants include:
- Precision: CAD provides a level of accuracy that is hard to achieve with traditional methods. The designs can be easily adjusted and refined based on the patient's unique situation.
- Time Efficiency: CAD software can streamline the design process, allowing for faster turnaround times. This is particularly beneficial in urgent cases where immediate restoration is needed.
- Impressive Visualization: Practitioners can visualize the final product through 3D models, enabling better communication with patients regarding their treatment options.
Given these advantages, CAD plays a pivotal role in the overall process of designing effective 3D printed dental implants.
From Digital Models to Physical Implants
The transition from digital models to physical implants is a fascinating aspect of the 3D printing process. Once the digital design is complete, the next step is to use 3D printing technology to bring these models to life. This stage requires precise coordination between digital plans and the actual manufacturing process.
The process generally follows these steps:
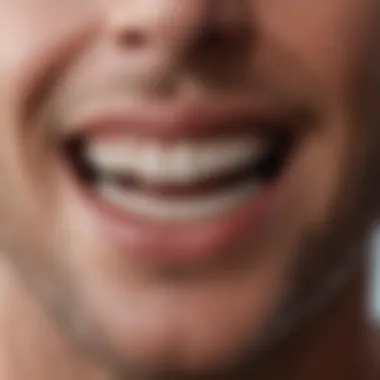
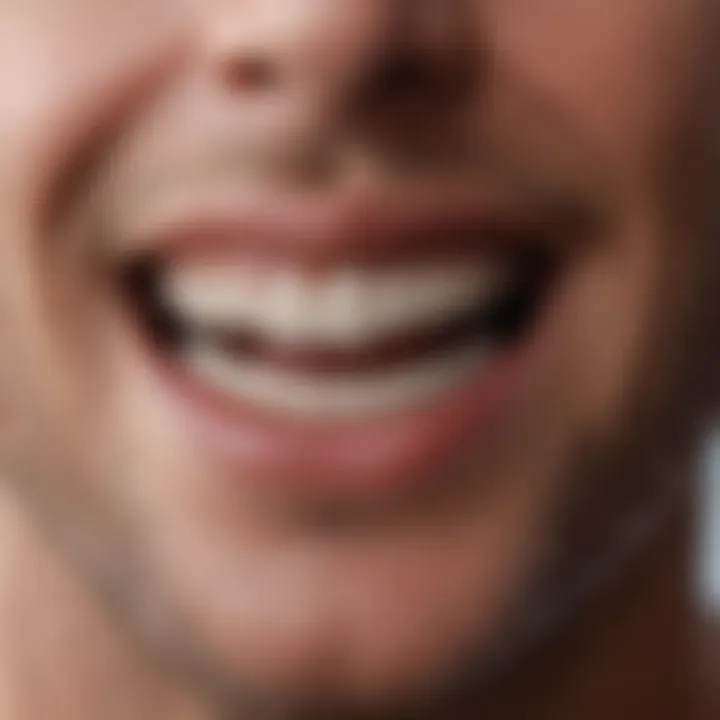
- Selection of 3D Printing Technology: Depending on the materials and specifications, the appropriate printing technology is chosen, such as Stereolithography or Selective Laser Sintering.
- Material Preparation: The chosen material, be it polymer, metal, or ceramic, is prepared for use in the printer.
- Printing: The printer creates the implant layer by layer, translating the digital design into a tangible form.
- Post-Processing: After printing, the implants often undergo various post-processing steps, such as cleaning and sterilization, ensuring they are ready for implantation.
Overall, this transformation from digital to physical is significant. It allows for the creation of implants that are specifically suited to a patient’s unique anatomical requirements, enhancing the effectiveness and compatibility of the implants.
The design process for 3D printed dental implants stands at the intersection of technology and patient care, highlighting the advancements in personalized medicine.
Clinical Advantages of 3D Printed Dental Implants
The introduction of 3D printing technology to the field of dentistry has fundamentally changed how dental implants are designed, produced, and utilized. This section highlights the clinical advantages that these cutting-edge implants provide. By focusing on patient-specific customization and improving precision in implant placement, we can appreciate the significant benefits they offer. These advancements lead to better patient outcomes, greater satisfaction, and potentially lower costs for treatment.
Customization for Patient-Specific Needs
One of the most significant advantages of 3D printed dental implants is their customization. Traditional implants often require a one-size-fits-all approach, which may not cater adequately to individual anatomical variations.
With 3D printing, dentists can create implants tailored to the precise dimensions of a patient's mouth. This process begins with sophisticated imaging techniques, such as cone beam computed tomography. These scans create a detailed digital model of a patient’s dental architecture.
The CAD software used can then be programmed to adjust the implant's size, shape, and features. This results in an implant that better fits the patient's unique anatomy.
Benefits of customization include:
- Improved fit and comfort
- Reduced risk of complications
- Shorter recovery times
- Enhanced aesthetic outcomes
Essentially, telorated implants minimize the likelihood of rejection and improve integration with existing bone. Personalized solutions ensure that dental professionals can address specific issues that may arise from conventional implants, ultimately leading to better oral health outcomes.
Enhanced Precision in Implant Placement
Precision in the placement of dental implants cannot be understated. Success largely depends on accurate placement, as poorly positioned implants can lead to complications, including infection or implant failure. 3D printing technology enhances this precision significantly.
By using computer-aided design and modeling, surgeons can plan the implant placement down to the millimeter. This careful planning facilitates the creation of surgical guides that provide real-time orientation during procedures. The guides help ensure that dental implants are placed at the correct angle and depth.
From 3D printed surgical templates, oral surgeons can:
- Achieve optimal positioning of implants
- Reduce surgery times due to pre-planning
- Ensure reproducibility for future procedures
Precision also translates to improved long-term outcomes. When implants are placed correctly, patients experience fewer complications and greater success rates. The efficiency gained through these techniques means that follow-up procedures may be less frequent, leading to reduced healthcare costs in the long run.
"The shift toward 3D printed dental implants showcases not just technological advancement, but a revolution in patient-centered care."
The combination of customization and precision highlights the clinical advantages of 3D printed dental implants, underscoring their role as transformative tools in modern dentistry.
Challenges and Limitations
The adoption of 3D printed dental implants presents several challenges and limitations that need careful consideration. Understanding these aspects is crucial for stakeholders involved in dental practices, including clinicians, manufacturers, and patients. The regulatory landscape, material selection, and biocompatibility are some of the significant barriers that can affect the effective implementation of this technology.
Regulatory Hurdles and Standards
One of the most pressing issues with 3D printed dental implants is the regulatory framework. Regulatory bodies, such as the U.S. Food and Drug Administration (FDA), have strict guidelines to ensure that medical devices are safe and effective. The unique nature of 3D printing complicates this regulatory landscape.
Each printed implant can be slightly different, depending on the specific patient needs and digital design files used. This variability puts a strain on standardized testing and approval processes.
Furthermore, the classification of these implants under existing regulations is an ongoing debate. Manufacturers must navigate this complex environment to attain necessary certifications. This process is often time-consuming and costly, potentially delaying access to innovative products.
Meeting stringent regulatory requirements is essential. It ensures patient safety and builds trust in new technologies. Successful navigation through these hurdles may foster a clearer path for future innovations in 3D printing within dentistry.
Material Limitations and Biocompatibility Issues
Material selection plays a pivotal role in the success of 3D printed dental implants. While there are several advanced materials available, not all meet the requirements for strength, durability, and biocompatibility.
Polymers, metals, and ceramics—each has its pros and cons. For instance, polymers might offer versatility but can lack the structural integrity needed for certain applications. On the other hand, metals, such as titanium, provide remarkable strength but may not always integrate well with surrounding biological tissues.
Biocompatibility is particularly critical as it affects how the body reacts to the implant. Poorly chosen materials can lead to adverse reactions, such as inflammation or rejection, which compromises patient outcomes. Ongoing research attempts to discover and develop new materials that not only possess the necessary physical characteristics but also ensure compatibility with human tissues.
Better materials could pave the way for more effective and reliable implants, addressing both functionality and patient safety.
By addressing these material limitations, the dental industry can leverage more promising options that enhance both effectiveness and durability of 3D printed dental implants.
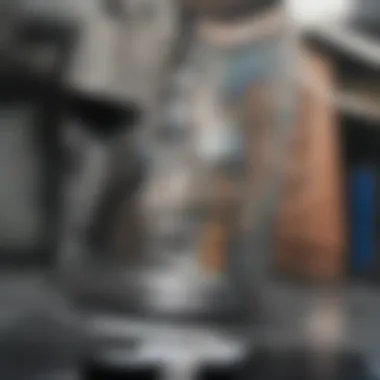
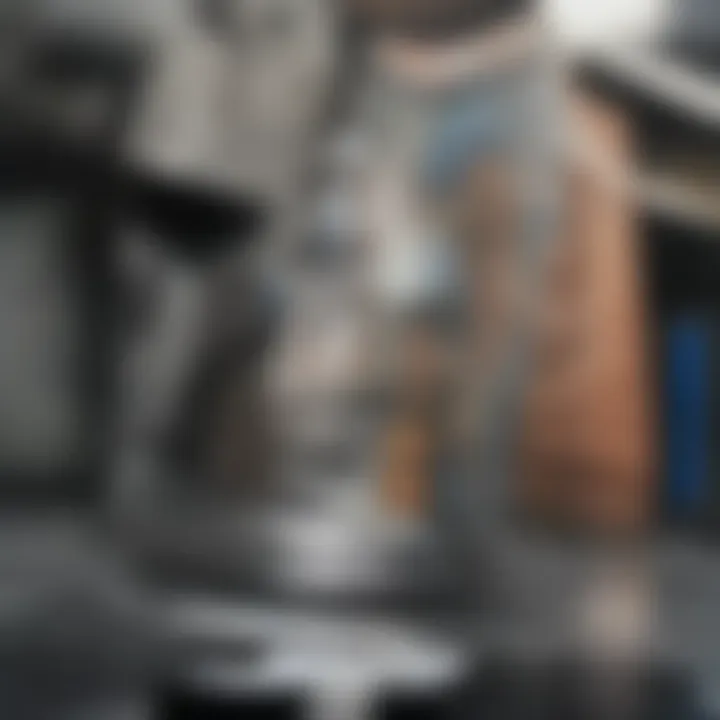
Future Trends in 3D Printed Dental Implants
The evolution of 3D printed dental implants is not just a trend but a significant shift in how oral restoration is approached. This section sheds light on the future directions that this technology may take, emphasizing integration with digital health technologies and the potential for mass customization of dental solutions. By understanding these trends, professionals in dentistry can better prepare for the changes on the horizon and embrace the opportunities they present.
Integration with Digital Health Technologies
Integration of 3D printed dental implants with digital health technologies can enhance patient outcomes significantly. Digital health encompasses a wide range of devices, applications, and platforms that leverage data to improve health care delivery. By combining 3D printing with tools like telehealth and wearable devices, practitioners can offer a more personalized, efficient, and data-driven approach to dental care.
For instance, real-time data from wearable technology can inform the design of dental implants tailored specifically to individual biomechanical needs.
Key benefits of this integration include:
- Enhanced Patient Monitoring: Continuous data collection enables adjustments to treatment plans based on real-time feedback.
- Streamlined Communication: Enhanced interfaces between dental professionals and patients facilitate quick decision-making.
- Predictive Analytics: Leveraging AI and data analytics to predict patient needs and outcomes leads to more proactive care.
This combination forms a rich ecosystem where dental health is monitored consistently, allowing for timely interventions and superior patient experience.
Potential for Mass Customization
The concept of mass customization in 3D printing represents a profound shift in how dental implants are designed and manufactured. Unlike traditional methods, where implants are produced in bulk without personal specifications, 3D printing allows for the direct adaptation of implants to each patient's unique anatomy and requirements. This not only addresses aesthetic concerns but also improves functional outcomes.
In practical terms, mass customization offers several advantages:
- Individual Fit: Each implant can be crafted precisely to fit a patient's dental structure, minimizing complications during placement.
- Speed of Production: Automation and digital design can reduce production time for implants, enabling quicker turnaround for patients in need.
- Cost-effictiveness: While initial setup costs for advanced equipment may be high, long-term savings stem from reduced material waste and less need for adjustments.
Mass customization is reshaping expectations in dental care. With patients becoming increasingly involved in their treatment decisions, dentists can provide solutions that resonate more with individual preferences.
Future advancements in this area will likely refine the process even further. It is crucial for dental professionals to stay informed about emerging technologies and practices that promise to enhance the quality and efficiency of patient care.
"The future of dental implants is not just about creating; it's about creating with precision tailored to the individual."
Ethical Considerations in 3D Printing for Dentistry
The integration of 3D printing technology within dentistry has brought numerous advancements, but it also raises critical ethical issues. As dental professionals employ 3D printing for fabricating implants and other devices, it is essential to consider the implications surrounding patient care, data security, and overall treatment consent. These elements are vital for ensuring that the benefits of this technology are realized without compromising ethical standards in the dental field.
Patient Privacy and Data Security
With the adoption of 3D printing, dental practices increasingly rely on patient data to produce customized solutions. This data often includes sensitive health information, making its security paramount. There are several components involved in maintaining data security:
- Data Storage Solutions: Practices must invest in secure data storage systems that are resistant to breaches. This often involves using encrypted databases and secure server environments.
- Access Control: Only authorized personnel should have access to personal data. Implementing strict access protocols minimizes the risk of unauthorized access and ensures patient confidentiality.
- Compliance with Regulations: Adhering to regulations, such as the Health Insurance Portability and Accountability Act (HIPAA), is crucial in safeguarding patient information. Awareness and training on these regulations are necessary for all staff members.
In the absence of rigorous data protection, patients may hesitate to provide personal information, jeopardizing both the practice's operations and the quality of care given to patients. Therefore, ensuring patient privacy and data security forms the backbone of ethical practice in 3D dental printing.
Informed Consent in Customized Treatments
Informed consent is fundamental when patients undergo any medical or dental treatment, and it takes on new dimensions within the context of 3D printed dental implants. As customization becomes a standard feature of dental care, ensuring patients fully understand their options is vital. Key elements of informed consent include:
- Clear Communication: Dentists must clearly explain the 3D printing process, the materials used, and the benefits of customized implants as compared to traditional options. This clarity helps build trust and ensures patients make informed choices.
- Comprehensive Information on Risks and Benefits: Patients should receive complete information regarding potential risks associated with the materials, potential complications, and long-term outcomes. This way, they can weigh these factors against the anticipated benefits of personalized implants.
- Autonomy and Choice: It is crucial to respect patient autonomy. They should feel encouraged to ask questions and express concerns regarding their treatment. This engagement fosters a collaborative relationship between professionals and patients.
Combining these considerations leads to a balanced approach, ensuring that ethical standards are met while harnessing the benefits of innovative technology. As 3D printing continues to evolve, awareness of ethical dimensions will remain integral to nurturing patient trust and advancing the field altogether.
Key Takeaway: The ethical implications of 3D printing in dentistry must be carefully considered to protect patient privacy and ensure informed consent, promoting better care and trust in dental practices.
Culmination
The conclusion of this article critically underscores the significance of 3D printed dental implants in the broader context of oral restoration. This innovative technology has made substantial inroads in transforming how dental practitioners approach the complexities of implant placement and patient customization. The use of 3D printing not only facilitates the production of highly personalized dental implants but also enhances the precision of implant placement, thereby improving the overall success rates of dental restorative procedures.
One of the predominant benefits of this technology is the ability to tailor implants to the unique anatomical characteristics of each patient. This customization aims to reduce healing times and minimize complications, fostering better patient outcomes that are vital in today’s competitive healthcare landscape.
Moreover, as we discussed earlier, the integration of digital technologies in the design and manufacturing stages allows for efficiency in the workflow, thus potentially lowering costs. However, the journey is not wholly devoid of challenges, including regulatory considerations and the need for improved materials that ensure biocompatibility.
"The advancement of 3D printing in dentistry holds the potential to redefine patient care, offering tailored solutions that were previously unimaginable."
Summary of Key Takeaways
- Customization of dental implants directly correlates with improved patient outcomes, allowing for a unique approach to oral restoration.
- Precision in implant design and placement facilitates higher success rates in dental procedures.
- The integration of digital technologies improves workflow efficiency, reducing costs and time involved in traditional practices.
- Ongoing research is needed to address challenges such as regulatory compliance and material biocompatibility, ensuring a seamless transition into widespread clinical use.
Call for Continued Research and Development
To fully leverage the benefits of 3D printed dental implants, continued research and development in this field is paramount. This pursuit should focus on developing new materials that possess optimal properties for dental use. For example, enhanced ceramics or polymers could significantly improve the longevity and functionality of the implants.
Furthermore, the ethical implications surrounding patient data security and informed consent in customized treatments require careful consideration. Research into comprehensive regulatory frameworks will facilitate smoother adoption of these implants into clinical practice.